How to add the Continuous Servo Movement Panel robot skill
- Load the most recent release of ARC (Get ARC).
- Press the Project tab from the top menu bar in ARC.
- Press Add Robot Skill from the button ribbon bar in ARC.
- Choose the Movement Panels category tab.
- Press the Continuous Servo Movement Panel icon to add the robot skill to your project.
Don't have a robot yet?
Follow the Getting Started Guide to build a robot and use the Continuous Servo Movement Panel robot skill.
How to use the Continuous Servo Movement Panel robot skill
This movement panel controls two continuous servos, which have continuous rotation. Unlike a Standard Servo, a continuous servo has its internals changed to allow continuous 360° rotation. The two parts that are removed from a standard servo to create a continuous rotation servo are:- Mechanical Stop: The spindle will stop if you attempt to rotate a standard servo further than 180 degrees. That is due to a mechanical stop built onto the output gear within the servo. Continuous servos have that stop removed.
- Potentiometer: The potentiometer in a standard servo records the position of the output gear. A potentiometer can only rotate to the physical limits of the internal wiper. When the potentiometer is removed (or replaced with resistors), the circuit does not know its position, and therefore the ability to specify positions is gone.
Two continuous rotation servos are great for moving your robot. Attach wheels directly to the servos and watch it go! Rather than using a standard DC Gear Motor, a continuous servo provides you with greater speed rotation accuracy. Due to the variety of servo attachments, continuous servos make great movement motors for wheels and tractor treads.
This skill operates like the other movement panels and can be controlled by scripting or other skills that interact with it. Movement Panels are skills that move your robot forward, reverse, left, and right. The Movement Panel directions can be modified by other skills, such as camera, voice, script, joystick, and radar.
Main Window
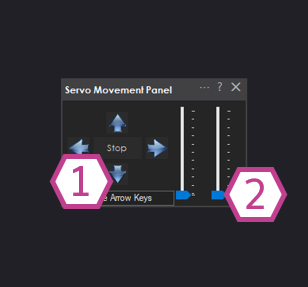
1. Movement Panel
These buttons will allow you to control the directional movement of the entire robot (left, right, forward, reverse, and stop).
2. Speed Sliders
You can select the speed of the servos with these sliders. Be aware that the speed range is (0-100%) and the default setting is 0% (OFF). These sliders can allow you to adjust for one servo being faster than the other. Note that not all continuous servos support speed selection.
Settings
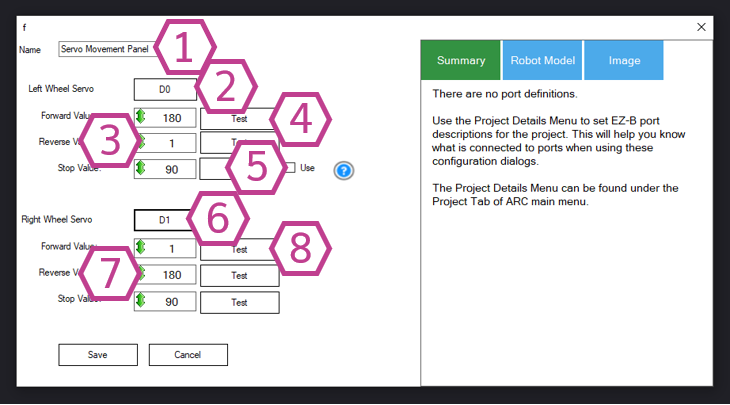
1. Title Field
This field contains the title of the skill. You can change it if you'd like.
2. Left Servo Port Drop-down
This drop-down selects the digital port that your Left continuous servo is connected to.
3. Left Servo Forward/Reverse/Stop Value Drop-downs
These drop-downs select the movement values for the Left Servo. A 180-degree signal causes the servo to move forward. A 1-degree signal causes the servo to move backward. The stop value for most continuous servos is 90 degrees.
4. Test Buttons
These buttons test the Left Servo Forward/Reverse/Stop values without returning to the main window.
5. Use Checkbox
This checkbox is unchecked by default and means that a PWM signal will stop being sent to the servo when the Stop button is pushed. If checked, this checkbox will make the stop button use the stop value of the servos. This is advantageous if you'd like your robot to break instead of coast to a halt instantly. Analog continuous servos tend to drift away from their stop value over time, so leaving the checkbox unchecked is beneficial.
6. Right Port Drop-down
This drop-down selects the digital port to which your Right continuous servo is connected.
7. Right Servo Forward/Reverse/Stop Value Drop-downs
These drop-downs select the movement values for the Right Servo. A 1-degree signal causes the servo to move forward. A 180-degree signal causes the servo to move backward. Notice that this is the opposite of the Left servo. The right servo is usually mounted in a mirrored configuration from the left. The stop value is 90 degrees.
8. Test Buttons
These buttons test the Right Servo Forward/Reverse/Stop values without returning to the main window.
How to Use Continuous Servo Movement Panel
1) Physically connect the two continuous servos to an EZ-B.
2) Add the Continuous Servo Movement Panel Skill to your ARC project (Project -> Add Skill -> Movement Panels -> Continuous Servo Movement Panel).
3) In the Settings menu, select the ports you connected the servos to (D0 & D1, for example).
4) In the main window, press the direction buttons to move your robot. If the directions seem reversed, you can swap your motors from each side or swap the ports in the settings menu.
Video
Requirements
- 1 x EZ-B I/O Controller
- 2 x Continuous Servos
Resources
Read more about how Movement Panels work here.
View the Servo Tutorial for technical details of how servos work.
Related Tutorials
tutorial
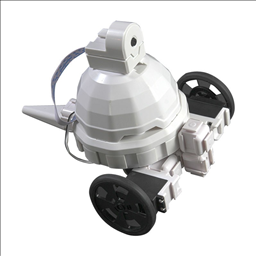
Calibrate Continuous Rotation Servo And Adjust Speed
How to calibrate the continuous rotation servos and adjust their speed. AdventureBot is used in this example.
tutorial
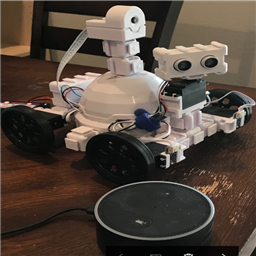
Using Amazon Echo (Alexa) As Microphone For Synthiam
In searching for a noise tolerant microphone for my EZ-Robot AdventureBot I checked out the Amazon Echo product which...
tutorial
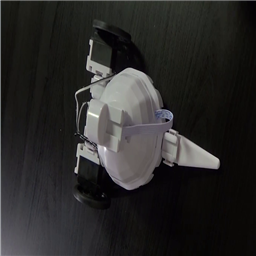
The Robot Program Episode 012: Getting Adventurebot To Move
This lesson will demonstrate how to connect to and move the Revolution AdventureBot robot. Follow along with The Robot...
Related Hack Events
live hack
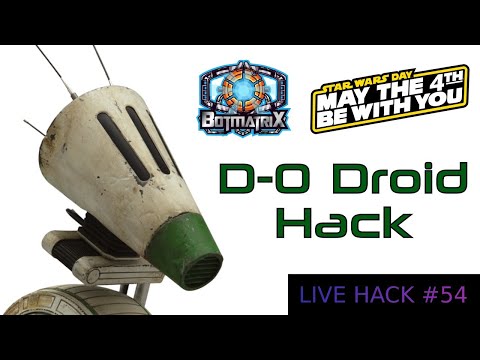
D-0 Droid Live Hack
Well, well, well look at me, so many unfinished hacks and Im starting another one! In my defense, May the 4th is coming...
live hack
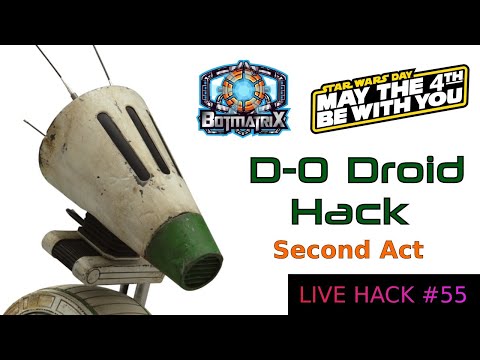
D-0 Droid Live Hack Part 2
May the 4th is tomorrow so Im gonna have to finish D-0 at the last minute! Join me as I scramble to complete him, and...
Related Robots
Related Questions
Upgrade to ARC Pro
Unleash your robot's full potential with the cutting-edge features and intuitive programming offered by Synthiam ARC Pro.
Is there a way to modify the controls to change the direction of the servos? To go forward, you have the right servo rotating clockwise and the left rotating counter-clockwise, and this works perfectly fine if the drive wheels are attached directly to the servos. However, since I'm trying to hack a Robie Sr. and I want to use its original FOUR wheels, this demands that I attach each servo to a gear that drives two wheels on either side in the opposite direction of which the servos are rotating. I thought that a simple solution to this problem would be to simply swap ports with the servos, and this DOES make the robot drive forward and backward with its respective Forward and Backward commands like it's supposed to... but when it comes to TURNING, the servos still rotate in the opposite direction just the same as if they were in their INTENDED ports. It drives forward like it's supposed to, it drives backward like it's suppose to, but the Left button makes it turn right, and the Right button makes it turn left.
Is there a way to invert these controls? Or would I be better off just using the TWO wheels that came with the developer kit and installing a couple of small caster wheels in the back for balance?
(I apologize for asking so many dumb questions, I don't know why I get so easily lost in here.
)
Change the values for the directions of each servo.
right now, the forward sends a command of some number. And reverse sends the opposite number. Those numbers are degrees. Reverse them
That was it. Thank you again!