Introduction To Servo Motors
This tutorial will provide technical information about servo-motors and how they work. We made it easy to get a robot up and running. However, there are many fun and exciting things to learn about how the robot works. The more you know, the more you can get your robot to do!
Table of Contents
- How To Move Servos In ARC
- What is a servo motor?
- Servo vs. PWM
- How does a servo motor work?
- Types of servo motors
- Controlling a servo motor
- How Does Continuous Rotation Servo Work?
- How is torque measured?
- PWM (hobby servos) vs. Serial (smart) Servos
- ARC Servo Robot Skills
How To Move Servos in ARC
We provided this support document for those who wish to learn how a servo works; however, press this button to learn how to move servos in ARC.
Learn how to move servos in ARCWhat is a servo motor?
A Servo motor (or servo) is a rotary actuator that allows precise angular position, velocity, and acceleration. Servos are found in many places: toys, home electronics, cars, and airplanes. If you have a radio-controlled model car, airplane, or helicopter, you are using at least a few servos. Servos also appear behind the scenes in devices we use every day. Electronic devices such as DVD and Blu-ray discPWMTM players use servos to extend or retract the disc trays.
Synthiam uses servos that manage the movement of joints, pan & tilt, and continuous rotational movement. For PWM Servos, the EZB sends an electrical signal that tells the servo what position to reach and how quickly to get there. Smart serial servos receive a protocol command by the EZB and the respective robot skill. Servos come in a variety of shapes and sizes for different applications. You may want a large, powerful one for moving the arm of a giant robot or a tiny one to make a robot's eyebrows go up and down. By linking many of these servos together, you can very easily create robots that perform complex real-world operations.
Hobby PWM Servo vs. PWM
PWM stands for Pulse Width Modulation. PWM is the process of turning ON and OFF digital voltage quickly to simulate a range of voltage. For example... If the digital output pin of a 5v micro is 2.5v, then the PWM is set for a 50% duty cycle. If the digital output of a 3.3v pin is 1.65v, then the PWM is set for a 50% duty cycle. The microcontroller turns the digital 3.3v pin on and off quickly, producing a simulated lower voltage. You can use PWM to vary the brightness of an LED, for example.
A hobby servo uses PWM as well. The "frame" of a servo PWM signal is 20ms. This means the signal frame repeats every 20ms. The signal is only 2ms, where the rest of the frame is empty (low). Many controllers, such as Arduino libraries, do not maintain the 20ms specification defined for servos. Because of this, challenges have been introduced to servo manufacturers when decoding incoming PWM signals. This has caused the need for servos to be "Smarter" by adapting to the unusual PWM transmitted by poorly written libraries that do not adhere to the servo PWM Standard. The EZ-B does adhere to servo PWM standards.
How does a servo motor work?
The simplicity of a servo is among the features that make them so reliable. The heart of a servo is a small direct current (DC) motor, similar to what you might find in an inexpensive toy. These motors run on electricity from a battery and spin at high RPM (rotations per minute) but put out very low torque (a twisting force used to do work — you apply torque when you open a jar). An arrangement of gears takes the high speed of the motor and slows it down while at the same time increasing the torque. (Basic law of physics: work = force x distance.) A tiny electric motor does not have much torque, but it can spin fast (small force, considerable distance). The gear design inside the servo case converts the output to a much slower rotation speed but with more torque (significant force, little distance). The amount of actual work is the same, just more practical. Gears in an inexpensive servo motor are generally made of plastic to keep them lighter and less costly. On a servo designed to provide more torque for heavier work, the gears are made of metal (such as with Synthiam Servos) and are harder to damage.
You apply power from a battery with a small DC motor, and the motor spins. However, unlike a simple DC motor, a servo's spinning motor shaft is slowed way down with gears. A positional sensor on the final gear is connected to a small circuit board. The sensor tells this circuit board how far the servo output shaft has rotated. The electronic input signal from the computer or the radio in a remote-controlled vehicle also feeds into that circuit board. The electronics on the circuit board decode the signals to determine how far the user wants the servo to rotate. It then compares the desired position to the actual position and decides which direction to rotate the shaft to get to the desired position.
![]() |
Figure 5. The circuit board and DC motor are in a high-power servo. Did you notice how few parts are on the circuit board? Servos have evolved to a very efficient design over many years. |
Types of servo motors
Servos come in many sizes and three basic types: positional rotation, continuous rotation, and linear. Regardless of the type of servo between PWM Hobby and Smart serial, the servo form factor can be in various configurations.
- Positional rotation servo: This is the most common type of servo motor. The output shaft rotates in about half of a circle or 180 degrees. It has physical stops placed in the gear mechanism to prevent turning beyond these limits to protect the rotational sensor. These common servos are found in Synthiam 's arms, legs, limbs, etc. For example, the JD or Six robots use these servos. Some servos, such as winch servos, will rotate their output shaft in multiple rotations (i.e., 270 degrees). The same signal (pulse width) is used for any servo regardless of the output shaft rotation. This means a servo of 270 degrees would have less resolution than a servo with a 180-degree range/
- Continuous rotation servo: This is quite similar to the common positional rotation servo motor, except it can turn in either direction indefinitely without any positioning ability. This means the servo does not know its position because it operates as a motor and spins continuously in either direction. There is no way to specify the position of a continuous rotation servo because they lack the hardware to do so. The control signal, rather than setting the static position of the servo, is interpreted as the direction and speed of rotation. The range of possible commands causes the servo to rotate clockwise or counterclockwise as desired, at varying speeds, depending on the command signal. If you mounted one on a robot, you might use a servo of this type on a radar dish. Or you could use one as a drive motor on a mobile robot. The Synthiam AdventureBot uses two continuous rotation servos with wheels. The center (90 degrees) is the center of a continuous rotation's STOP position. The further you move away from 90 degrees in either direction controls the speed of the continuous rotation servo in that direction.
- Linear servo: This is also like the positional rotation servo motor described above, but with additional gears (usually a rack and pinion mechanism) to change the output from circular to back-and-forth. These servos are not easy to find, but you can sometimes find them at hobby stores, used as actuators in larger model airplanes.
Controlling a PWM servo motor
A standard servo is what you usually find in R/C Hobby Toys. They are high-precision devices that can rotate a shaft up to 180 degrees. With the EZB and a Standard Servo, you can easily configure how many degrees to rotate the output shaft.ARC takes care of the electrical communication with the servo for you, whether PWM or Smart serial. You can use standard servos for the head or arms of your robot.
However, here is some technical information on how hobby PWM servos work. The servo is controlled using pulse control. The control pulse is a positive voltage with a length of 1 to 2 ms, which determines the angle of the shaft. The control pulse is repeated every 18-25 ms.
TO ACCOMMODATE ALL SERVO TYPES, the EZ-B has timing below 1ms and above 2ms. Some servos do not fall within the specifications and require unusual timing. When testing with your servo, make sure you recognize the max and min values and set them in the robot skill settings. If a servo attempts to move further than its maximum position, it may be damaged. Additionally, if a servo is rotated too far, it will consume a high current, and the EZ-B may reset.
Here are the timings for the EZ-B...
Position 1 on v4, Position 1 on v3
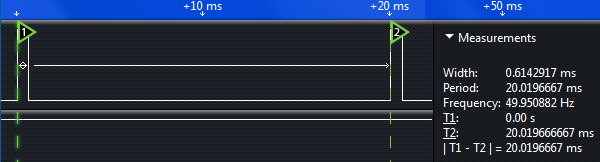
Position 90 on v4, Position 50 on v3
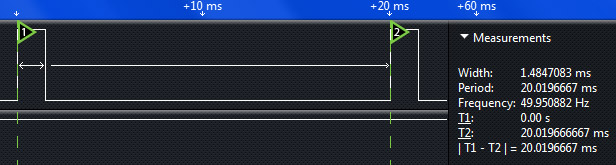
Position 180 on v4, Position 100 on v3
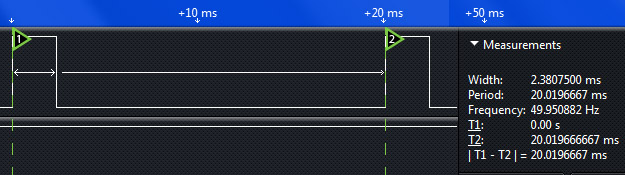
For example, the EZ-Robot EZ-B v4 has high accuracy, which results in 180 servo positions. The EZ-B v4 can control 24 servos simultaneously while performing other user-specified tasks. If your servos draw more current than our specification sheet defines, the EZ-B may run out of power and reboot itself. This is called a Brown-Out. To prevent brownout with many servos, provide alternate power. Check the manual on how to do that.
ARC handles the technical work for you. Merely specify the servo position, and voila!
How Does Continuous Rotation Servo Work?
As mentioned earlier in this lesson, a continuous rotation servo will spin the rotation shaft continuously in either direction. The continuous rotation servo will stop spinning when the servo receives a 90-degree position centered on a standard servo. The center (90 degrees) is the center of a continuous rotation's STOP position. The further you move away from 90 degrees in either direction controls the speed of the continuous rotation servo in that direction. The continuous rotation servo will have a POT (potentiometer) exposed, allowing you to fine-tune the STOP position with a small screwdriver. Click here to view a tutorial on calibrating a continuous rotation servo.100 < - Turning left faster
99
98
97
96
95
94
93
92
91 < - Turning left slower
90 <- Stopped
89 <- Turning right slower
88
87
86
85
84
83
82
81
80 < - Turning right faster
How Is Torque Measured?
Now that we covered the basics of how-a-servo-works, the next question is torque. Torque is how much power the servo has. Different applications will require higher or lower torque. In most cases, you can get away with using a regular average torque servo. The average torque of a plastic servo is 2-3kg/cm @ 5 volts, and the Synthiam Heavy Duty servos are much more (consult the servo product information).Something that is often overlooked is energy consumption. Consider this: there is no free energy. Torque equals energy and vice-versa. The Synthiam Heavy Duty servos will require more energy to move than cheaper plastic ones. Suppose too many high torque servos are connected to the EZ-B without a sufficient power source. In that case, it will "brownout" Browning-out means the voltage regulator could not keep up with the current draw, so the microchip rebooted itself due to low current. Do not worry; the Revolution Robots are powered by a strong LiPo battery and support up to 24 servos!
So what do the torque numbers mean? Let's speculate the torque value of a servo was 50 Ounces per Inch.
Well, if you had a servo arm that was one inch long on your servo, it would be able to produce 50 ounces of pull or push force at the end of the servo arm before stalling. What do you think the force would be if you had a 1/2 inch servo arm? Yup, 100 ounces of force. How about a 2-inch arm, 25 ounces of force - easy, huh?
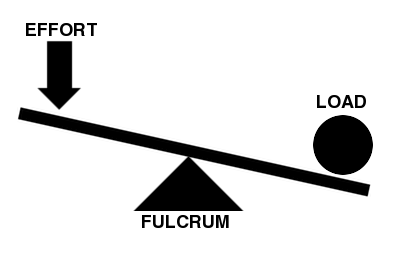
PWM (hobby servos) vs. Serial (Smart) Servos
The most common servos in robotics are three-wire PWM Hobby Style (power, GND, PWM signal). These servos have been around for decades and are the most cost-effective solution. The shortcoming of these servo types is they have only one direction of communication from EZB to the servo. This means the servo only knows its position when instructed to move. When these servos are first initialized, they will jump from whatever position is currently into the specified position. It will not transition slowly during initialization because it does not know the starting position before initialization. When robots use these servos, they will jump and sometimes cause damage preparation is not considered. The solution to avoid jumping is to manually move the robot joints into a position close to the initialization position so the servos don't jump. This is more effort than using Smart Servos, which will report their position to the software.
Smart serial servos use a communication protocol that allows the servos to transmit position data to the EZB. These smart servos have bi-directional communication to query the position when initialized and transition to the new position at specified speeds. This prevents jolting/jumping of joints that are experienced with hobby PWM servos.
When a robot is powered on, it is recommended to create an initialization script launched from the connection control. The initialization script will accommodate the type of servos being used. If the servos are PWM style, it is recommended to move the robot joints before executing the initialization script manually. With a smart serial servo, you can query the position. Therefore ARC will know the position, and your script can calmly move the servos into a pre-defined position.
ARC Servo Skills
ARC supports several servo robot skills.
Create frames and actions to animate the robot servos into pre-defined positions. This can be used to have the robot wave, dance, or display interactive gestures. A gait is the movement pattern of animals limbs, including robots, during locomotion. This robot skill allows robots to customize servo animations for gait locomotion and interacting with the world. Some robots (i.e., humanoids, hexapods, and more) use servos to move with gaits based on speed, terrain, maneuverability, and energetic...
This skill automatically releases specified servos after a certain amount of time from their last movement. This is very helpful to use when it comes to repetitive, quick servo movements. Main Window 1. Pause Checkbox This button pauses the application of the Auto Release skill. 2. Status Display This displays which port the auto release skill was applied to and at what position it was last in before the auto release was activated. Settings 1. Title Field This field contains the title of...
Unlike a Standard Servo, a continuous servo has its internals changed to allow continuous 360 rotation. The two parts that are removed from a standard servo to create a continuous rotation servo are: Mechanical Stop: The spindle will stop if you attempt to rotate a standard servo further than 180 degrees. That is due to a mechanical stop built onto the output gear within the servo. Continuous servos have that stop removed. Potentiometer: The potentiometer in a standard servo records the...
Use Vx virtual servo ports to control up to 99 servos on a custom servo controller via a serial protocol, such as Arduino Mega, with custom firmware. The Vx virtual servo ports allow you to control up to 99 servos on a custom servo controller via a serial protocol, such as an Arduino Mega, equipped with custom firmware. This custom firmware can be loaded onto an Arduino or a custom microcontroller, transforming it into a specialized servo controller. The robot skill will establish a connection...
Connect and control Robotis Dynamixel Smart Servos with ARC, including Arduino and Robotis controllers. This open-source plugin converts the Virtual Servo ports with any EZ-B (v0-v99) to control Robotis Dynamixel Servos. The servos supported are XL-320, AX-12, and XL430 compatible protocols. Dynamixel Servos are very different than regular hobby PWM servos. Firstly, they are considered much more professional due to their design, specifically for robotics use. Each Dynamixel Servo contains a...
Control Feetech serial bus smart servos over EZB UART or PC COM port. The selected ARC’s Vx virtual ports must match the servo IDs in the config screen - and voila, youre off to the robot races! Main Window The main window on the project workspace will display information about active connections and errors. To configure the servos, press the ... configuration in the title bar. (/uploads/user/DB763BE15E695777689418BE7364E0A3/c4r4n0sr.png) Configuration Screen The configuration allows selecting...
Control Feetech serial bus smart servos over EZB UART or PC COM port. The selected ARC’s Vx virtual ports must match the servo IDs in the config screen - and voila, youre off to the robot races! A Bus servo from Feetech has a model number starting with SC, such as SC215. Main Window The main window on the project workspace displays information about active connections and errors. To configure the servos, press the ... configuration in the title bar....
This servo skill allows you to drag the mouse horizontally (left right) on display to move the position of a horizontal servo. The horizontal servo will only move to the minimum and maximum limits you specify in the skills settings. The limits are both set to 90 by default. *Note: Like all robot skills, this does not save the last servo position used. To set a servo position when the robot connects, create an initialization script using the Connection Skill...
This Synthiam ARC Robot Skill is a powerful, customizable tool that provides advanced kinematic solutions for your robot arm. This tool allows you to define and manipulate the structure of your robot arm by adding joints and bones, providing a high level of customization to suit your specific needs. It is designed to be user-friendly and intuitive, making it accessible to beginners and experienced users. Whether designing a robot for industrial applications, research, or personal projects, the...
Control Kondo KRS smart servos with ICS 2 3.5 Protocol over the EZB UART. We cannot verify this works because we do not have servo hardware to test with. This plugin is in response to a community thread (//synthiam.com/Community/Forum/Thread?threadId=9961) regarding Kondo servos. *Note: This is experimental The servos can be chained together and connected to the EZ-Bs UART #1 on port D5. The baud rate must also be configured in the settings of the plugin. Each virtual port can be selected for...
Control the LewanSoul Digital smart Servos (i.e., LX-16A) with ARC. The servos must be powered appropriately and connected to the EZ-B v4 or IoTiny with the respective port. Visit the Config menu of this plugin to view the port configuration. This plugin will only operate on EZB Index #0. Demonstrated with IoTiny using Software UART Details ARCs Virtual Ports (V1..V99) can be assigned to the LewanSoul servos. - This plugin requires the RX signal wire of the servo to be connected to the TX of...
The Lynxmotion Smart Servos (LSS) are compact, modular actuators which were designed to be an evolution of the standard servo for use in multi degree-of-freedom robots, animatronics, custom robot projects and more. The servos form the core modules of the next generation Lynxmotion Servo Erector Set (S.E.S.) and a wide variety of modular brackets, mechanics and electronics have been designed around them. Smart means there is sensor feedback for Position, built-in safety features. The LSS...
Control servos using the Pololu Maestro servo controllers that come in flavors of 6, 12, 18, or 24 servos. The connection for this robot skill is USB, and therefore great for onboard computers. (/uploads/user/DB763BE15E695777689418BE7364E0A3/zxfy1gs0.png) This robot skill binds to the ARC Vx virtual servo ports. The index of each Vx port is directly related to the index of the Maestro servo port. That means if you send a movement to V1, the servo is sent to Maestro #1 servo. Configuration...
This control will allow hobby PWM servos to have positional feedback in ARC with a slight modification requiring a wire, soldering iron, and Philips screwdriver. This uses the ADC port on the EZ-B (v4, Arduino, etc.) Example In this video, we remote control a JD with another JD. The servo positions from one JD are read using this robot skill, and the positions are set to the other JD. This is like using one JD as a puppet to control the other JD. Video Tutorial Watch this video tutorial to see...
Receive servo positions in real-time over an Arduino and its ADC ports. This control connects to an Arduino over I2C and receives the values of the ADC ports. The Arduino requires firmware to be programmed, which can be downloaded below. Depending on your Arduino version, the code can be modified for the number of ports. The Arduino code available here is for the Arduino Nano, a tiny little Arduino that nicely fits next to an EZ-B or IoTiny. It connects to the EZ-B via I2C using its A4 and A5...
This skill is similar to the Horizontal and Vertical servo skills. However, the difference between this skill and the others is that it allows you to specify a Master Servo. The slave servos will move into relative positions of the Master. If you move the master servo from ANY skill, the slave servos will move to their relative positions. You can use scripting or the checkbox to Pause and Unpause this skill whenever you like, preventing the slave servos from moving. Note that servo selection...
Inverse kinematics calculates the joint angles to position the Robotis Open ManipulatorX effector to a specific desired location in 3d cartesian space. Inverse Kinematics Inverse kinematics is a computational process used in robotics to determine the joint configurations necessary to position and orient the end-effector (usually a robot arms hand or tool) at a specific target location and orientation in three-dimensional space. It involves solving equations that map the desired end-effector...
Move a servo using the mouth with an on-screen widget
This skill allows you to drag your mouse or finger (on a touchscreen) to move x-axis and y-axis servos. Its like a virtual joystick. This is a great skill to use when you have servos in a pan/tilt configuration. Main Window 1. Servo Pad Hold your mouse or finger (if you have a touchscreen) on this pad to control servos in a pan/tilt configuration. Swipping left and right will move the x-axis servo. Swipping up and down will move the y-axis servo. Settings 1. Title Field This field contains...
This plugin allows recording and replaying servo movements in specified speeds and direction. Trigger the recording playback and speed using ControlCommand() from scripts. Realistic Motions For realistic motion recordings, we recommend creating the recordings with the Servo Pad Control. Find more information about the Servo Pad here: http://www.ez-robot.com/Tutorials/Help.aspx?id=150 (http://www.ez-robot.com/Tutorials/Help.aspx?id=150) Recording You can store multiple recordings in this plugin....
This skill allows you to adjust the speed of a servo or PWM between two positions. It can be used for quickly identifying and experimenting with servo speeds for your application. This skill does not save the last setting or restore settings when the project is loaded. *Note: Before this skill can be used, the servo position must be initialized. To do this, you can simply set the position with a script command or a servo skill. If you wish to have your robot initialize a servo speed when...
This control is an all-in-one servo view. You can add servos to be viewed in the summary. The position and speed are displayed and both can be modified. The control can be resized to fit the number of servos added.
Adding this control to your project will connect to an SSC-32 servo controller. The connection can be direct via pc com port. Or through an ezb supporting the Hardware Uart or Software Uart capabilities, such as the EZ-Robot EZ-B v4/2 Wi-Fi Robot Controller or Arduino Mega. The Virtual Servo Ports in ARC, labeled V0, V1, V2... V31 will be connected to the SSC-33 and used to move servos through the SSC-32. The configuration menu on this control will allow you to specify the baud rate and how the...
Control up to 127 stepper motors as servos with any stepper motor driver or motor type. This robot skill requires a low-cost and small-profile Arduino connected to each stepper motor driver. Each Arduino is given a unique ID on the optional serial network, which matches an ARC Virtual Servo (Vx) port. All 127 Arduinos will share the same PC COM port via the first Arduinos USB connection. An optional end-stop limit switch can calibrate the steppers home position. For example, if the Arduino...
Control the UBTECH Alpha Robot Digital smart Servos (UBT-12HC) with ARC. The servos must be powered appropriately, and connected to the EZ-B v4 or IoTiny with the respective port. Visit the Config menu of this plugin to view the port configuration. The Virtual Ports (V0..V99) in ARC can be assigned to the UbTech servos. UART Ports - This plugin requires the RX signal wire of the servo be connected to TX of the selected UART or digital port (if Software UART is selected on IoTiny) - Hardware UART...
This servo skill allows you to drag the mouse vertically (up down) on display to move the position of a vertical servo. The vertical servo will only move to the minimum and maximum limits you specify in the skills settings. The limits are both set to 90 by default. *Note: Like all robot skills, this does not save the last servo position used. To set a servo position when the robot connects, create an initialization script using the Connection Skill...
This is a test to control waveshare bus servos with TTL or RS485. The buttons will perform different actions on a servo with ID #1. (/uploads/user/DB763BE15E695777689418BE7364E0A3/znbdqidw.png) - The RTS-enabled option may need to be used for some serial converter controllers. Try with and without this option checked. - The Set Position will move the servo. Make sure nothing is attached to the servo; otherwise, it will move and break whatever you have attached. This moves between positions 250...