A movement panel to control brushless motor controllers. These are used in hoverboards or many other robot types.
How to add the Brushless Motor Movement Panel robot skill
- Load the most recent release of ARC (Get ARC).
- Press the Project tab from the top menu bar in ARC.
- Press Add Robot Skill from the button ribbon bar in ARC.
- Choose the Movement Panels category tab.
- Press the Brushless Motor Movement Panel icon to add the robot skill to your project.
Don't have a robot yet?
Follow the Getting Started Guide to build a robot and use the Brushless Motor Movement Panel robot skill.
How to use the Brushless Motor Movement Panel robot skill
A Movement Panel to control brushless motor controllers. These are used in hoverboards or many other robot types. This uses generic (popular amongst DIY projects) brushless motor controllers. These controllers have a pin for direction, speed, and brake for each motor.
Configuration
The configuration menu has options to select the ports for generic brushless motor controllers. Select the ports that are connected to the appropriate connections between the EZB and motor controller.
*Optional: the brake port is optional as it may not be necessary for some applications. Some applications may leave this wire disconnected from the EZB.
Related Questions
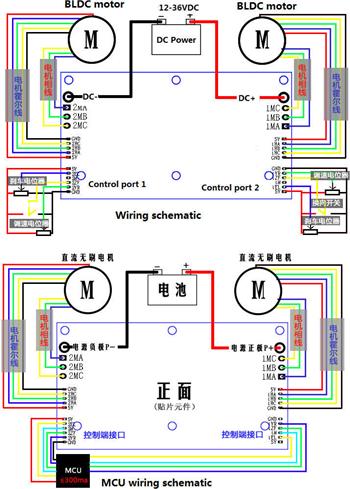
Brushless Motor Controller
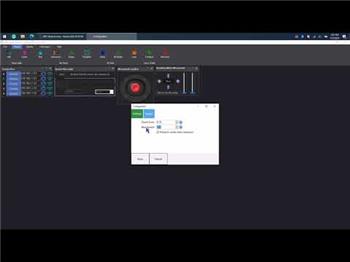
Brushless Motor Controller V3
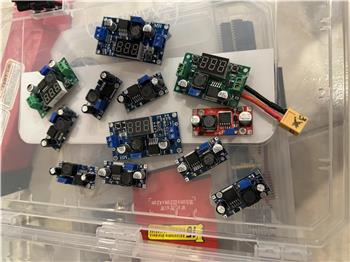
Powering Mini/Micro PC With Lipo
Upgrade to ARC Pro
Experience early access to the latest features and updates. You'll have everything that is needed to unleash your robot's potential.
Latest release bug fix for motors being reversed
First Hooked up with ez b v4 and Brushless Motor control worked OK. Using hoverboard motors for robot. today Ive been installing a LattePanda D and have it and the Leonardo working but the motor controller. Using same port setup, DTR set and its connected. Now wheels turn on only full speed, no speed change. Matter a fact wheels don't move till speed is half way. thought it might be another skill interfering so deleted everything but motor controller, same issue. Any ideas?
Verify the selected ports are correct, and the wiring to the controller. If needed, put a volt meter on each port to see if it’s the right one and mapped correctly. That’ll help ensure the latte panda’s Leonardo isn’t faulty
Checked and rechecked three times, sometimes I do mix grays and greens! Meter on pinD1 Moving left speed slider, o volts till just about half way, then it goes to 5volts. That is forward button pushed. 0volts if stopped. Also have reflashed Arduino twice. Not sure how to test code?
Looks like video didn’t send so, I checked and voltage goes from 0-5 volts with no pwm, I also had an issue when using zen v4 and that was to fast turning hard l or r.
Hopefully we can figure this out. Like I said earlier, have rechecked hook up and settings and as video shows, it’s not working on LattePanda with Leonardo! Thanks for any guidance you can give.
Scott
Doesn't look like this will help but ??
EZB 0: 2021/07/19 5:30:46 -07:00 Windows version: Microsoft Windows NT 10.0.18363.0 2021/07/19 5:30:46 -07:00 Screen Resolution: 1920x1080 (96x96 dpi) 2021/07/19 5:30:46 -07:00 ARC (Early Access) Version: 2021.07.01.00 2021/07/19 5:30:56 -07:00 TCP Server started on 5685 2021/07/19 5:32:27 -07:00 Attempting connection on COM6 2021/07/19 5:32:28 -07:00 Connected to COM6 at 9600 2021/07/19 5:32:28 -07:00 Reports CapabilityController 2021/07/19 5:32:28 -07:00 Firmware 'DJs Arduino Leonardo v1' on 'Arduino Leonardo' supports the following capabilities:
2021/07/19 5:32:28 -07:00 Connected 2021/07/19 7:46:09 -07:00 DTR Enable cannot be changed while connected. Reconnect for this setting to take effect. 2021/07/19 7:46:09 -07:00 TCP Server: Stopped 2021/07/19 7:46:09 -07:00 TCP Server stopped
EZB 1: EZB 2: EZB 3: EZB 4:
Your log shows that you enabled DTR 3 minutes and 14 seconds after connecting...
That message explains you would need to reconnect for DTR to take effect. You need to enable DTR before a connection is established. Always a good idea to read the log when experiencing difficulties. Additionally, you can verify the Leonardo works by checking one of the i/o pins and setting it ON and OFF with a digital port robot skill: https://synthiam.com/Support/Skills/Digital/Set-Digital?id=16094
Can this skill be used with a brush-less motor that has a built in controller? I am looking at using this motor: https://www.robotshop.com/en/36d-brushless-dc-motor-with-planetary-gearbox-12v-32rpm.html I will be using just one motor (not like a hoover board dual motor setup). If this will work, what do I connect each pin on the motor to on the control?