Hi all,
I'd like to share a video I just took of my full size Lost in Space B9 robot that's controlled by two EZ-B controller boards. Right now they are controlling limited movement and voice response of a few motors, lights and sound files played from a Sparkfun MP3 Trigger board. Although I'm just starting with the animation and have more building on the actual robot the result (mostly thanks to the EZ Robot controller board) is shocking. Please have a look at this (4 minute) You Tube vid and enjoy.
Please excuse some Technical camera lighting and sound issues. This is the first time I'd made and posted a vid online.
EDIT 8/2/13: Just realized I have no good pictures of how my B9 will look when complete. Here's one of the actual TV robots from the 60's TZ show Lost in Space and one recent shot of where I'm at with my build over 1 1/2 year after I started. Enjoy:
Thanks, Dave Schulpius
Other robots from Synthiam community
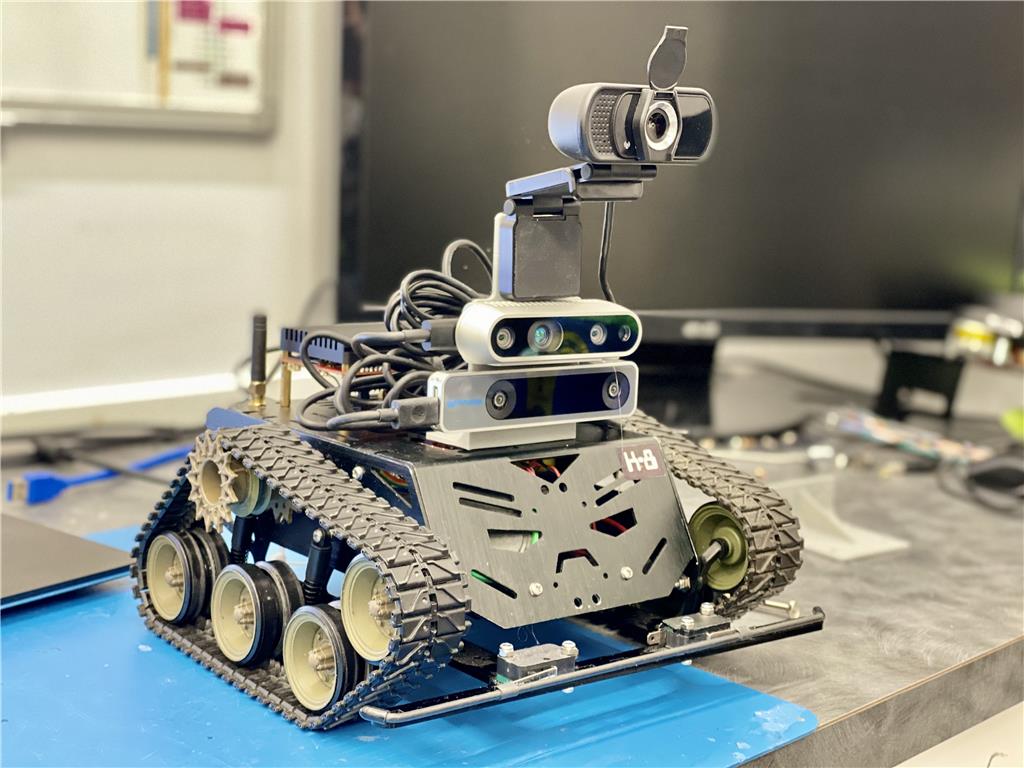
DJ's DJ’S Test Platform (K8)
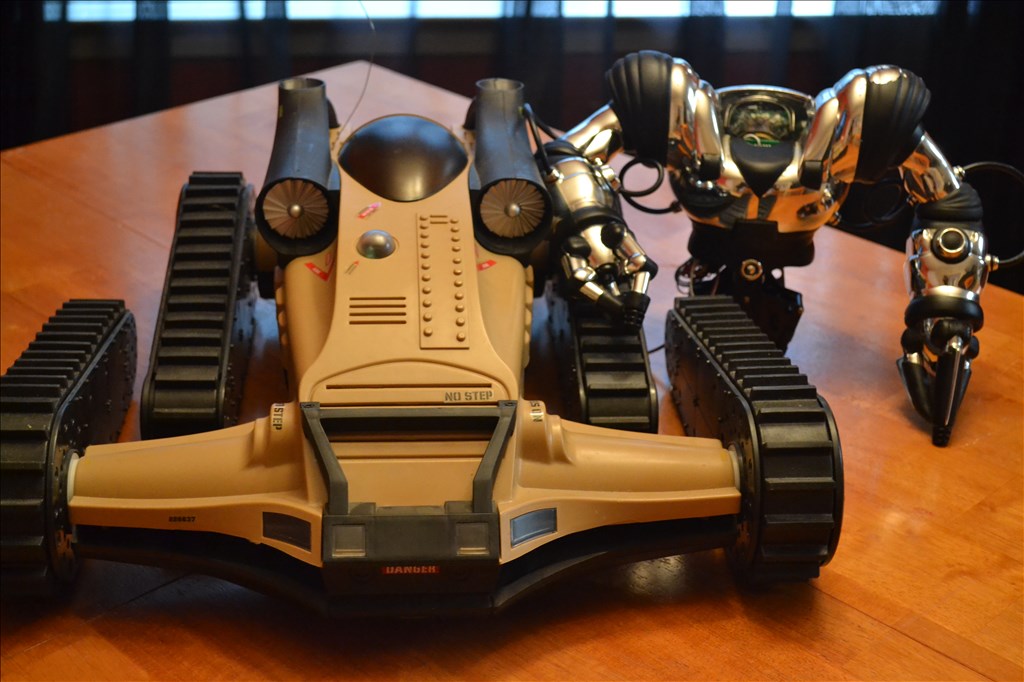
Joseph4760's Project X-Men Juggernaut
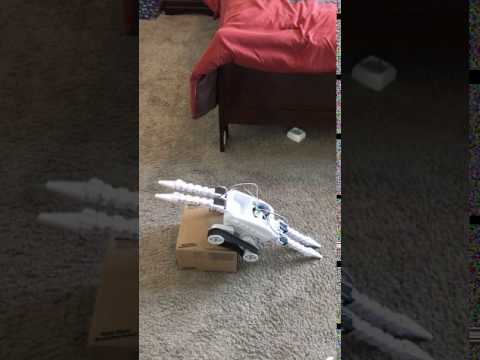
Dave, have you you thought about using something like this for feedback? I am thinking of puttng four into each elbow. Two might work, one for up and down - one for side to side, but they say that they do not work well bending backwards.
flex sensor
@Danger, I've never seen these flex sensors. They look very useful. With one on each axis (two per joint) a person could use a regular geared fast DC motor along with an H-bridge and Kangaroo X2 board and turn it into a servo. That would give us the best of both worlds! If Tony's motors don't work for me I need to look into these sensors. Thanks!
Dave You could try to run the motors at 24V that should give another good increase in speed. Its not like normal servos, that if they are given over-voltage its usually the electronics that burns out and not the motor, what we have here is just the DC motor being given over-voltage which is the armature windings (the motors electromagnets). These motor drives are for the automotive industry and are high specification so the winding may well run at 24V with no problems. You could just try to run one (at 24V) for a time period (loading it if possible) to confirm it will be ok. If this does burn the motor out, I will send you a replacement. As I mentioned before because of the worm drive in these motors the windings will only be drawing current when they are moving to the next position so most of the time they will be in zero current draw.
Another idea is to have a simple 2 voltage switch where you connect your main 24V for higher speed operation then switch in the 18V or lower (via a buck converter) by a relay to get the slower operation. The relay could be energised by another port line on the EZ-B, this way its only 24V when you want faster arm actions like "warning Will Robinson" and then back to 18V for general arm movements that are more calmer/fluid, this would be much simpler to do this than trying to introduce PWM into the Kangaroo x2 (in servo mode) setup.
The plastic gears are high impact and incredibly strong, I do not think you will see any problems here.
Tony
@Tony, this all makes sense. I love to push the boundaries and see how close to the edge I can get. "No guts, no glory" I always say. However I'd hate to put 6 months of work into a design only to have motors burn up or not perform like I'd want. I'll load up one of these motors and run it at 24v for at least 24 hrs to see how it holds up. I'll call it "the burn in period".
Maybe if I can pump the voltage to 24v I'll be happy with the speed.
I've found that trying to mate the Kangaroo to a regular h-bridge or motor controller is just to complicated for what I want to do here. Thanks to Tony (again) there seems to be a way to do it, although it's untested. He stated in a personal e-mail this morning:
The Kangaroo x2 is designed by the same company that makes the Sabertooth. It's used as a daughter board to add functionality and more ease of use to the Sabertooth. I could try to hack it to work with the pololu VNH5019 Motor Drivers I've been using but honestly I just don't want to go down that road. I have no wish to make this more complicated then needed. So I'm going to buy a few of the much less expensive Sabertooth 2x5 motor controllers so I can natively mate the Kangaroo to get my fluid servo type movements from these DC motors. The 2x5 Sabertooth can handle current up to 5 amps and there is no way these motors will ever pull that much. Also I really want to use the servo controls in ARC. I feel I'll get a lot better and smoother movements using them and be able to create more complicated animated movement routines.
@Toymaker very good suggestions! and @Dave we all hope your research is fruitful !
I can hardly wait for those B9 arms to start "waving" to everyone and exclaiming " danger, danger EZ-B Forum people, your not spending enough time playing with robots!" 
You're a scream irobot58!
I spent hours this afternoon ordering parts like brackets, hubs and Sabertooth boards for my arm build. It feels good to have a plan and somewhat of a design now. A lot of this will be building and adjusting on the fly.
Sabertooth has boards starting at 2x5, 2x12 and up. The Kangaroo X2 board says it works with 2x12 on up but says nothing about the 2x5. The board I want to use is the 2x5 so fearing that the Kangaroo wont work with the 2x5 I also ordered a couple 2x12's (just in case).
Now I wait on deliveries. No worries, lot of other things to do in the mean time. Fun times indeed!
@Dave, there are a few options on flex sensors on sparkfun.com website if you need another size.
Thanks Troy . I'll have a look. These Flex sensors are interesting. I wonder how acetate and consistent they are.