Hello all, I wanted to start my own thread to discuss my Inmoov and my conversion to EZ Robot. I appreciate all the work by the MRL guys but I struggle with it. I am indebted to the help they gave me but I needed something a little more along in development with some documentation.
So here is my guy. Pretty standard build as far as inmoov's go.
Here's the back. All the standard inmoov components. Dual 256 Megas, Nervo boards USB hub, Power supplys etc.
So the tear down begins. I need to clean up that wiring too. What a rats nest!
I just received my EZR controller and camera so I have no idea how to program it yet. I figured I would at least try to set up a GUI that allows me to manually move the servos like the MRL swing GUI. Five or six hours later and a few tutorials and I have this three screen model. I was easily able to add way more than basic servo control.
Here is the main control screen. Contains the face tracking speech functions and a custom Pandorabot for AI. Some MS cognitive stuff as well.
Here is the second screen. Head functions with a mouth control servo, neck, torso, and the 2 neopixel rings I have.
Third screen is for the arms and hands
So now I pretty much have all the same functionality I had in MRL give or take. I am pretty sure I am not doing this entirely correctly but it will come with time. Need to get into the scripting. I guess there are some tutorials to watch. So far my experience has been pretty good and in a day eclipsed my MRL progress of the last 6 months.
I'll update this thread with my progress and appreciate any feedback.
Other robots from Synthiam community
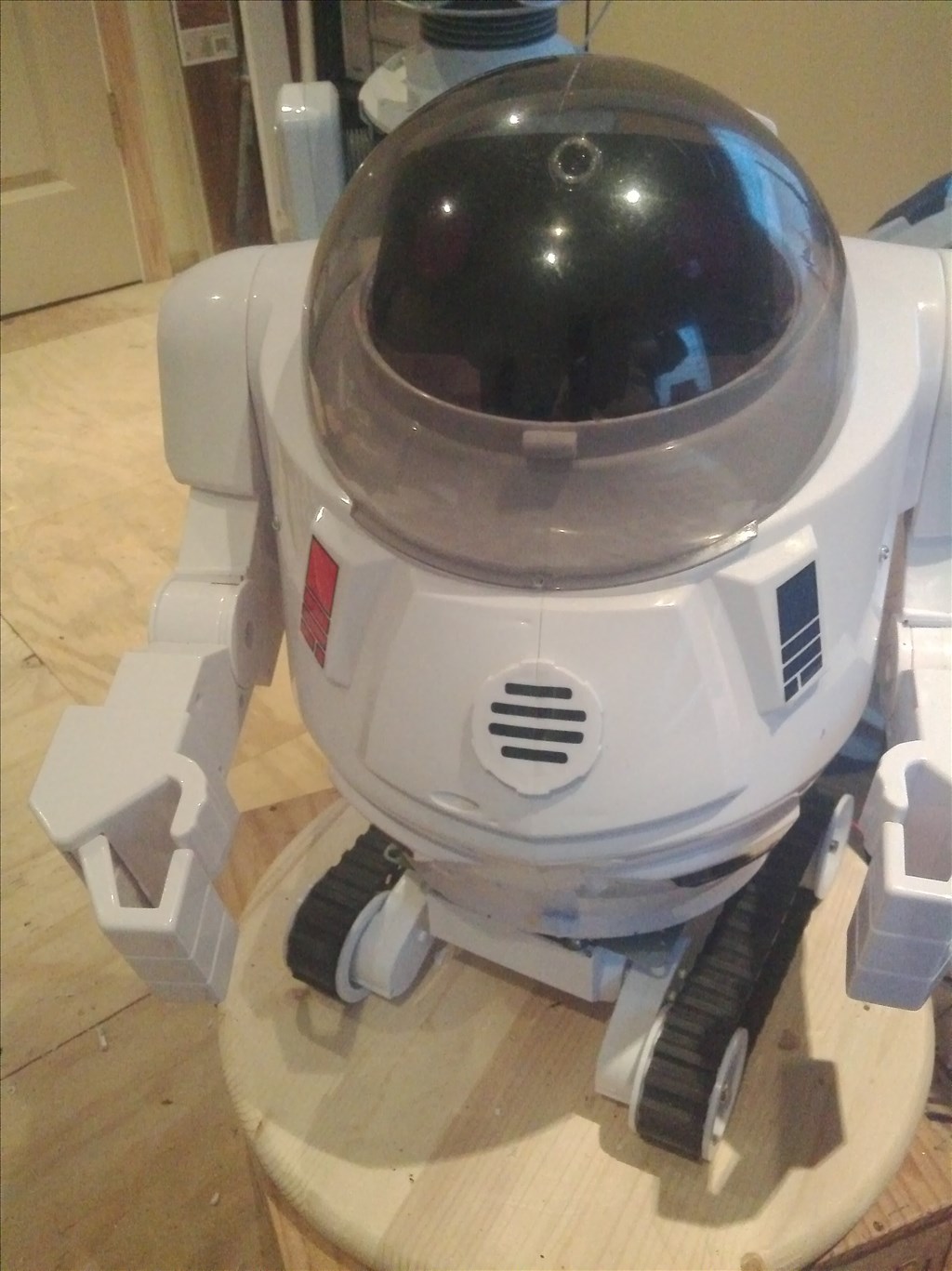
Rb550f's Ez Robot Rover
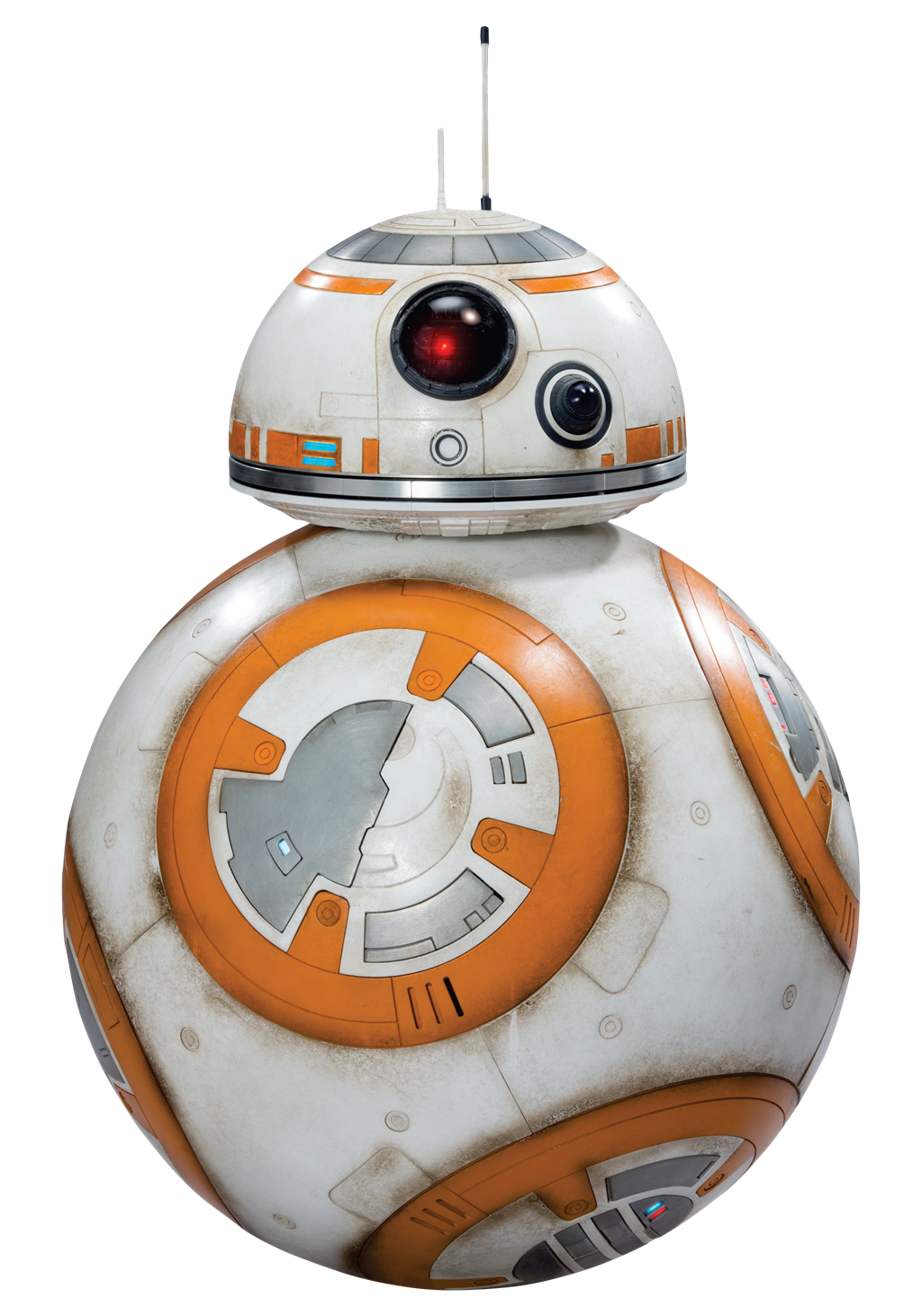
Johnnypipey's Bb8 On The Cheap Project
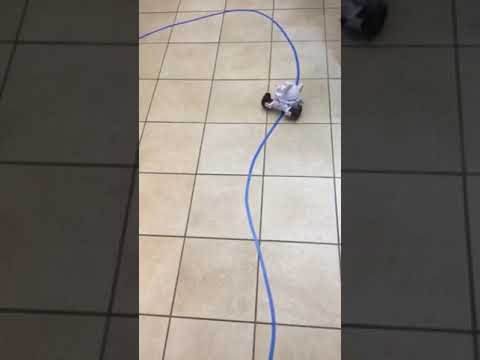
Awesome start.
Before getting into scripting, I would start looking at auto-position. It allows you to easily build animations of servos moving in concert rather than just triggering them individually. Then tackle scripting where you execute your autopositions based on various triggers. Much easier than trying to script servos one at a time.
Alan
Welcome to the club. Nice InMoov, I've seen it on InMoov's site. I too started out with MRL and then switched over EZ Robot. You are really going to like it here! As Alan said work with the Auto Position control - that's how I do all of my movements/animations - with some scripting as well you can operate everything very easily.
Alright, that's two people telling me to start looking at the Auto Position function. Sounds like my weekend homework has been assigned.
@Perry_S make it 3.. the autopositioner is a God send for creating inMoov movements and animations...
Just a bit of advise when using the Auto Position Control. Start out by creating a frame that has all of the servos in a position that would be the 'Rest' position. Then connect to the EZB. If you don't create this frame before connecting to the EZB all of the servos will go to 90 degrees when you connect to the EZB. Then to create other positions, start with the robot in this position, connected, then create a new frame and move the servos into the position you want. I learned this the hard way and broke some joints when everything went to 90 degrees.
My InMoov project is in the App store - Bob's InMoov
Thanks for that advice Bob. I have really bunged things up before with servo positions and scaling with MRL. Broke more than a few servos as they initialized waiting for the limits to be set. One of the main reasons I migrated.
Haven't had a chance to look... does Auto Position work with virtual servos i.e. Dynamixels? Thanks Chris
Yes! Auto Position Control works very well with Dynamixels.