This project has evolved some , the basic rundown is I'm modding two Omnibots , one a regular the other a larger 2000 model. I will have two ezb kits , rad base idea was thrown out because of so much noise but could go back on the table if the omnibot drivetrain is too weak to pull it.
By jstarne1
— Last update
Other robots from Synthiam community
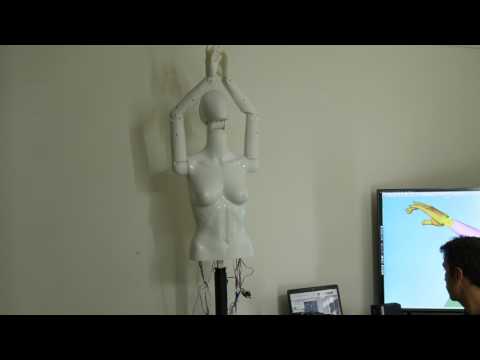
Zxen's Robomannequin
This is Eve. What do you guys think so far?
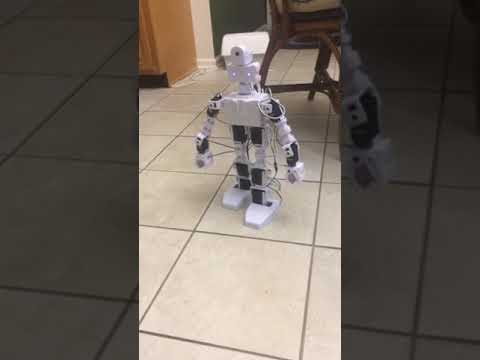
Ezang's I Am A. B. - J D's Bigger Brother
I am not 6 foot tall, but I am taller the J D, I have longer legs and arms Here is a pic: Added a servo for his head,...
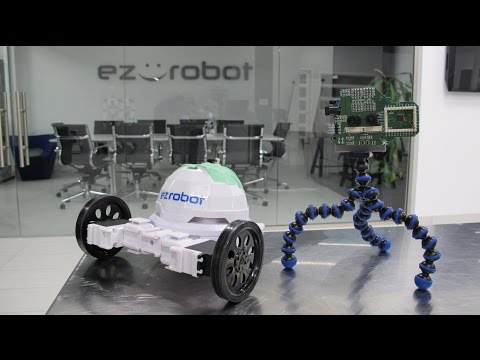
DJ's Ips (Indoor Positioning System)
For quite a few years, ive been mentioning that I have been working on a positioning system for ez-robots. I guess its...
Hey Josh, you could just epoxy a nut on the end of the plastic tube that matched the threads. Just a thought.
i think thats what he is doing with that design
Since its a worm gear (depending on how tight the pitch is) it may hold its grip when the servo is released. If thats the case, why not close it until stall. Use the stall sense idea DJ mentioned a few months (or year ago). For the multiturn pot, try to do like I did and use a standard pot near the shaft.
only problem with stall sense is that the mosfets (h-bridge) will burn up only way to do it is have a circuit that senses stall condition and remove the power from the servo easy way to test is simple get super cheap servo and apply stall torque for over a 1 min,and check the h-bridge for high heat or smoke
here is info on stall torque Electric motors [1] continue to provide torque when stalled. However, electric motors left in a stalled condition are prone to overheating and possible damage since the current flowing is maximum under these conditions.[2]
I remember somone had a 6 turn pot that would.be.ideal right?
need a multiturn pot,more turns better the accuracy
I was thinking of using the original screw , but I guess I could make a completely new one. A new one would be stronger.
Current sense can stop the servo if it sees a certain amount of current drawn. It's logical to say if full stall is 5 amps , and free turn is .5 amps then setting the stall sensor to release the servo as soon as it sees 2 amps that would protected servo.
Ok yeah, it WAS an H-bridge design. Over a year and a half ago. Feb 2011