Hello all, I am getting back in the saddle making robots now that I am moved into my new home and settled into my new job as a technician maintaining the Fiber Optics network in Chattanooga TN.
IM BACK !
By jstarne1
— Last update
Other robots from Synthiam community
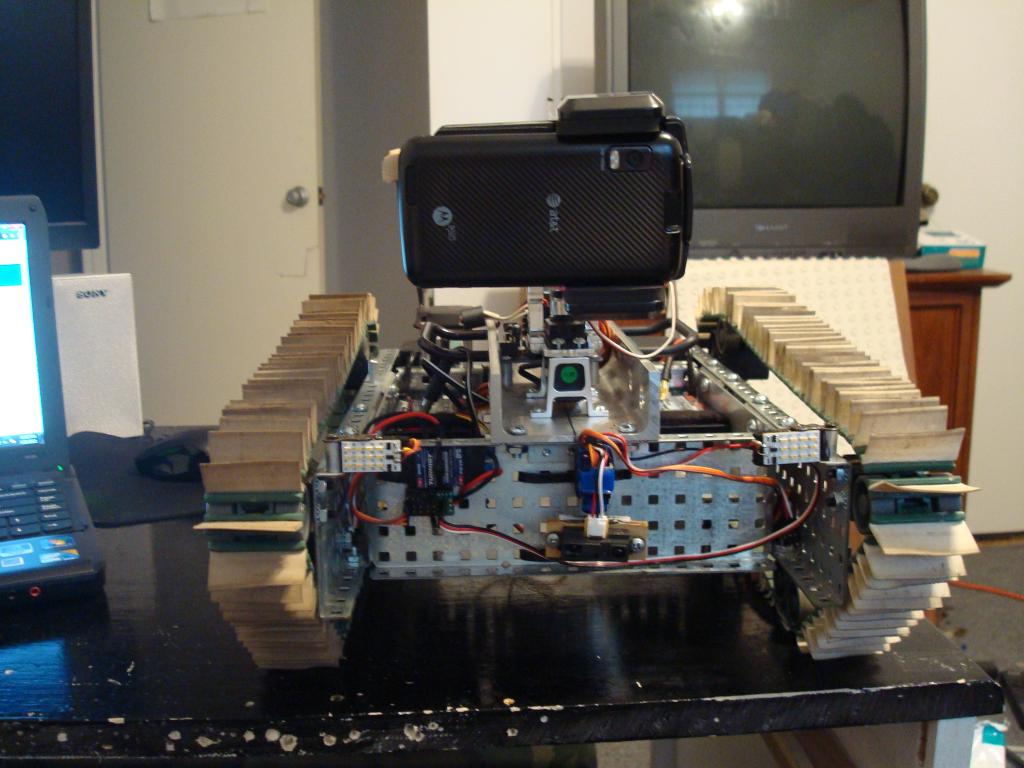
Imrisaac's Ez-B Project V3.0
This is sort of a survailence tank ive been building the past couple of days. At its heart is of cours the EZ-B...
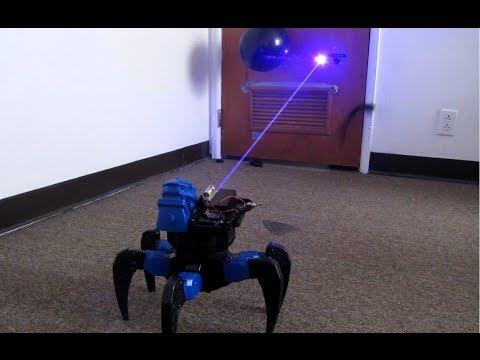
Nomad's Using Robosapien V2
hi all i finally got the v2 up and running.my idea was to use this one whit the ez-b4 iff possible.i also want to have...
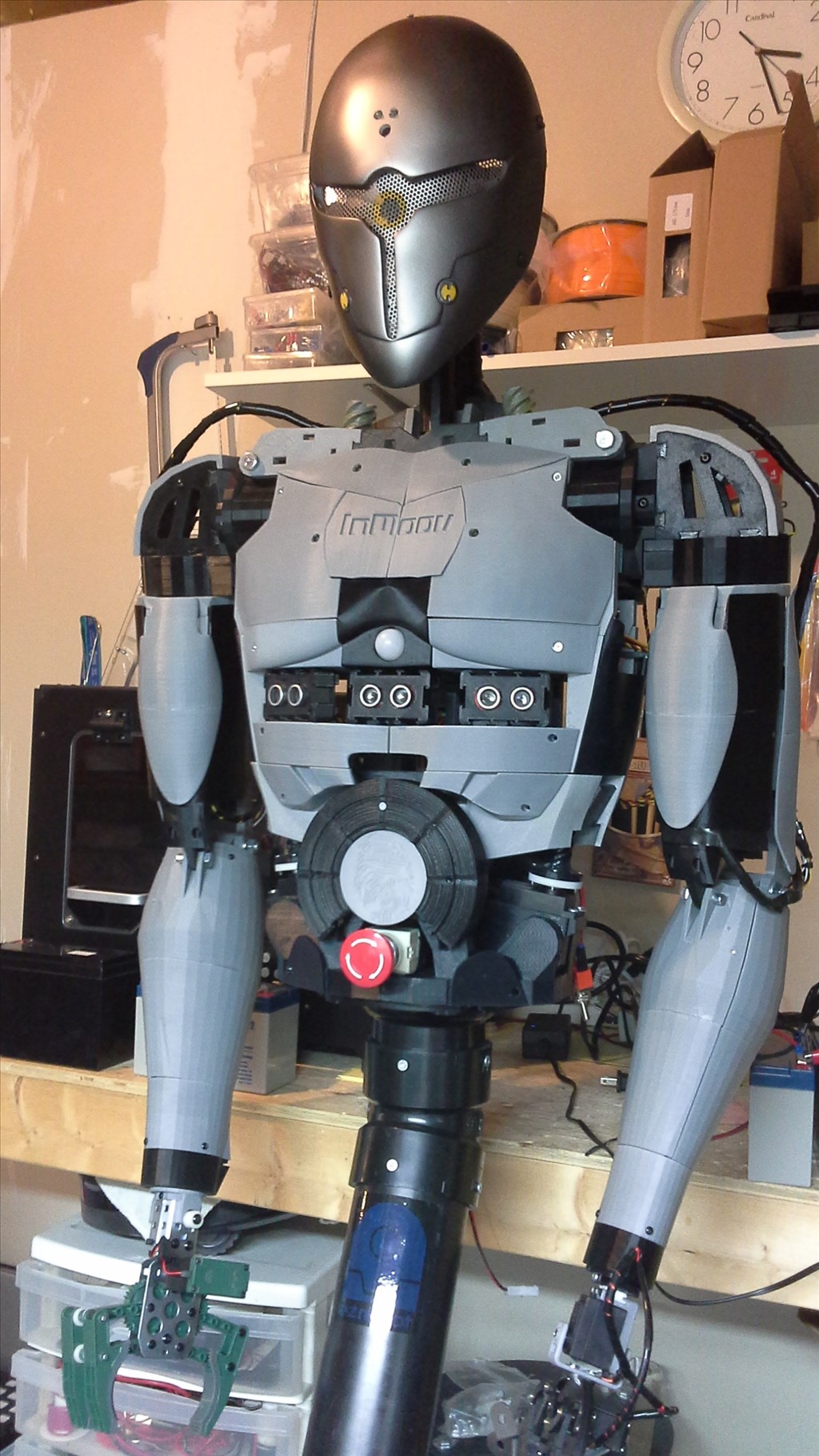
Dunning-Kruger's Is There A Halloween Contest This Year?
I thought I would lighten things up around here by giving you all a sneak peek of my possible Halloween contest...
A NINJA MOWER ..... Killer of Dandy Lions. Silent but Deadly !
Just think if it had 4WD it would make a killer monster truck.
Ok so I'm fitting the mower with 5/8" wide by 3 inches long zinc coated bolts as rear wheel axles. I used a saw to cut the original 1/2 " axle down to the flat spot that the original bearing was pressed against.
Here is the first zinc steel bolt being fitted onto the bung where the original 1/2" axle was tack welded on. It has a 3 inch shafts. I used JB weld Knicks for the flat surface to flat surface weld and next I will sand the edges that squished out and apply another 1/8" layer all the way around of high strength jb weld. Once it sets I will sand that and apply a third and final layer. The goal is to basically use a whole tube on each axle to handle about 30 pounds of weight on each wheel.
To prep both the bolt head and the axle face I sanded off all powder coat with 60 grit sand paper. I will update on the next layers and test fit tonight.
The next prepped face
Ok so I discovered that the JB epoxy weld cannot live up to this job , so I will move on to welding tommorow. I think the axle and the bung are both some kind of steel so I should be able to use my 90 amp might Welder on them. Sadly it's been many years since I have welded anything so I will practice of a scrap piece so I do not totally bugger it up.
First axle tacked on in 2 or 3 places. It feels solid enough. I will wait till later once the motor is mounted to make a bead. I need to make sure everything lines up well.
Ok second axle tacked on. Here are pics with wheels on and different height settings.