It's just a concept right now but I wanted others to see that the scale doesnt quite match. Right now its just stacked on there and neck is a little too long.
By Troy
— Last update
Other robots from Synthiam community
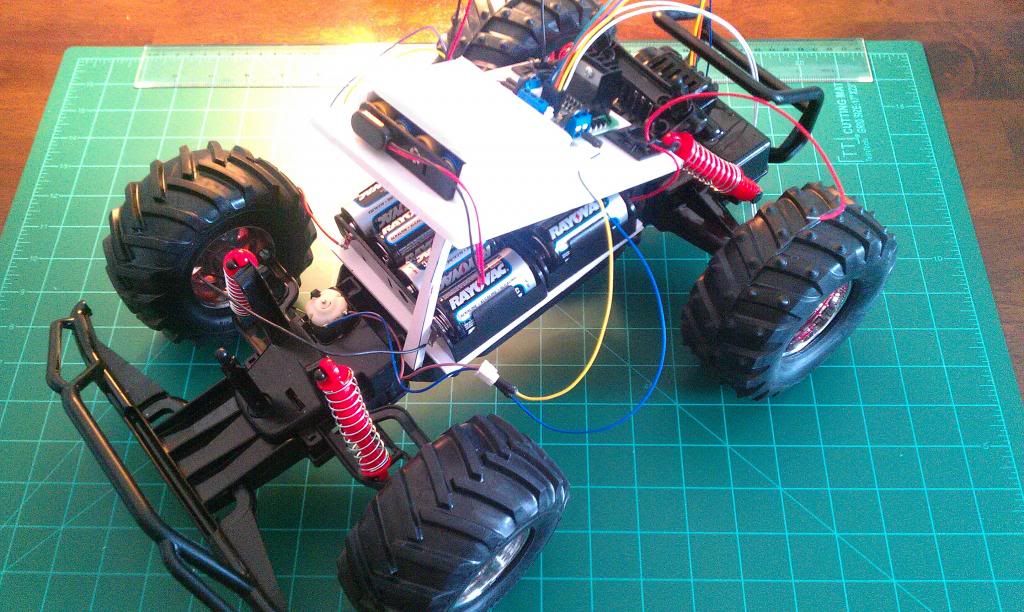
Leversofpower's Cutting My Teeth. The Floor Crawler
I had been so exclusively focused on the pre-design work for the Wowee Roboquad hack and waiting on parts to arrive from...
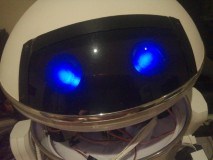
Rb550f's Meet Tk
I have started work on my 15th robot project TK . It is 31 inches tall and has a 12 inch diameter base. Weighs 12 pounds...
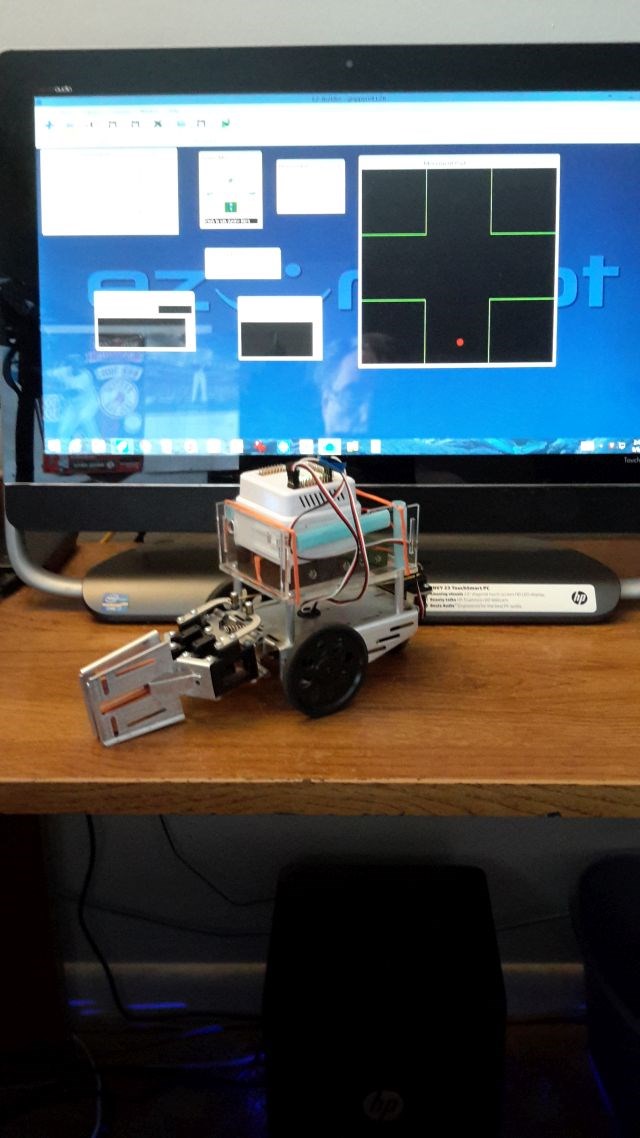
Jdebay's Gripperv4 Old Parts And New Parts
old parts and new parts make gripperv4. j update: added camera. j
Thank you Hazbot ! Most of the work was already there mechanically from the clock radio. The challenge will be the scripting and syncing movements.
Good work!
Looking really great!
Woo hoo... That looks like it works great. I wouldn't have thought to take a servo apart.
Thank you R2D2, Bret and Sam. It really wasnt a lot of work. I just got lucky that the gears meshed and the total rotation of the gear was nearly exactly the range of the potentiometer. I wish I had more time to work on it.
i have take so many many of them apart SAM ,its pretty easy and make a great servo contoller for any motor,,you put the pot on the last gear to give the highest feedback and most servo's use a standard h-bridge chip with 1 amp driving power,but to double the current you put 2 in parallel if need higher then use a higher current h-bridge ,simple to wire in only 4 wires most common servo ever used is FUTUBA S3003 if its hard to attach the pot to the last gear then get a gear the same as the last one for 1-1 ratio like i am doing on my omnibot hand design
GLICKCLICK there is another you may see,the chips on servo board may not handle 12 VOLTS may need 2 different power source for the chip,mainly servo chip ,most common is BA6688L if uses a micro,its a little harder,BUT on the h-bridge it can be done
i can put a schematic of the circuit used in most servo's except digital types
Do you think it will handle 7.2-7.4? Thats what I was going to try.
depends on the servo,what type are you using (model #)