It's just a concept right now but I wanted others to see that the scale doesnt quite match. Right now its just stacked on there and neck is a little too long.
By Troy
— Last update
Other robots from Synthiam community
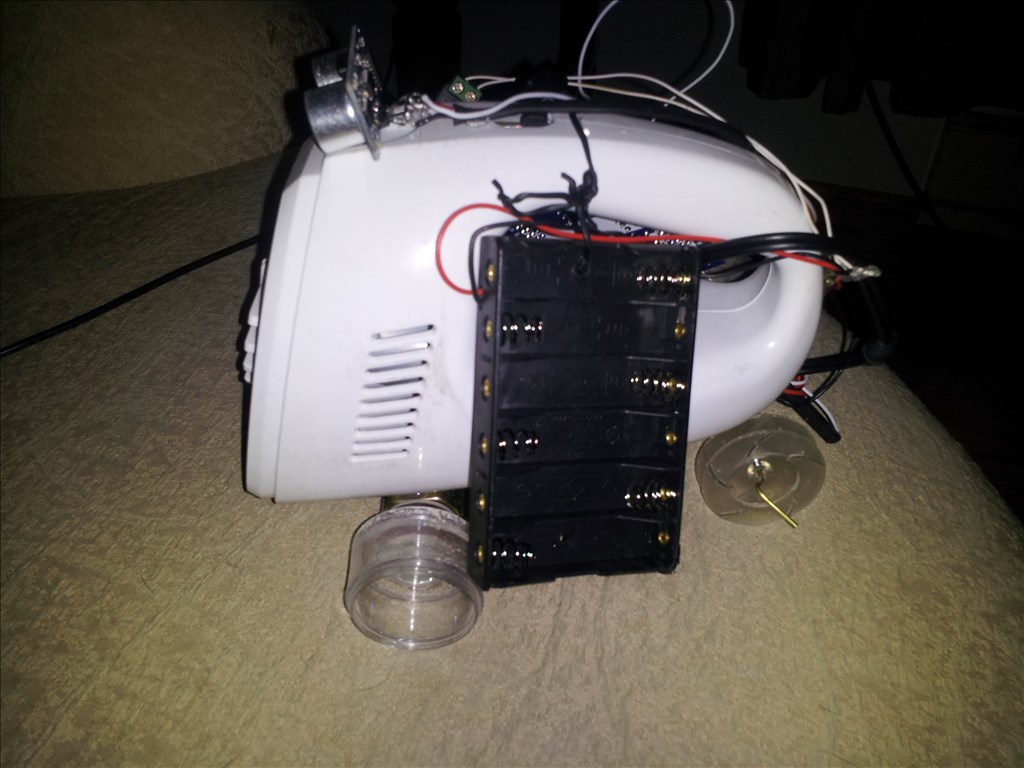
Derrick's First Bot
I finally purchased an EZ-B, I didnt go with the kit (on a budget) just the board. My Idea is to make an autonomous...
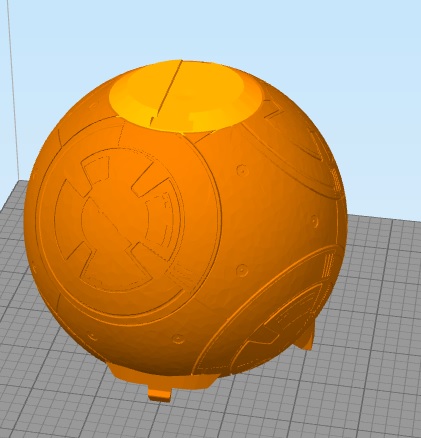
Justinratliff's Ez-Robot Bb-8 Hexapod Body
I made a BB-8 hexapod body to go with the head. You can use the mountable head with the EZ-Bit I made: Or you could...
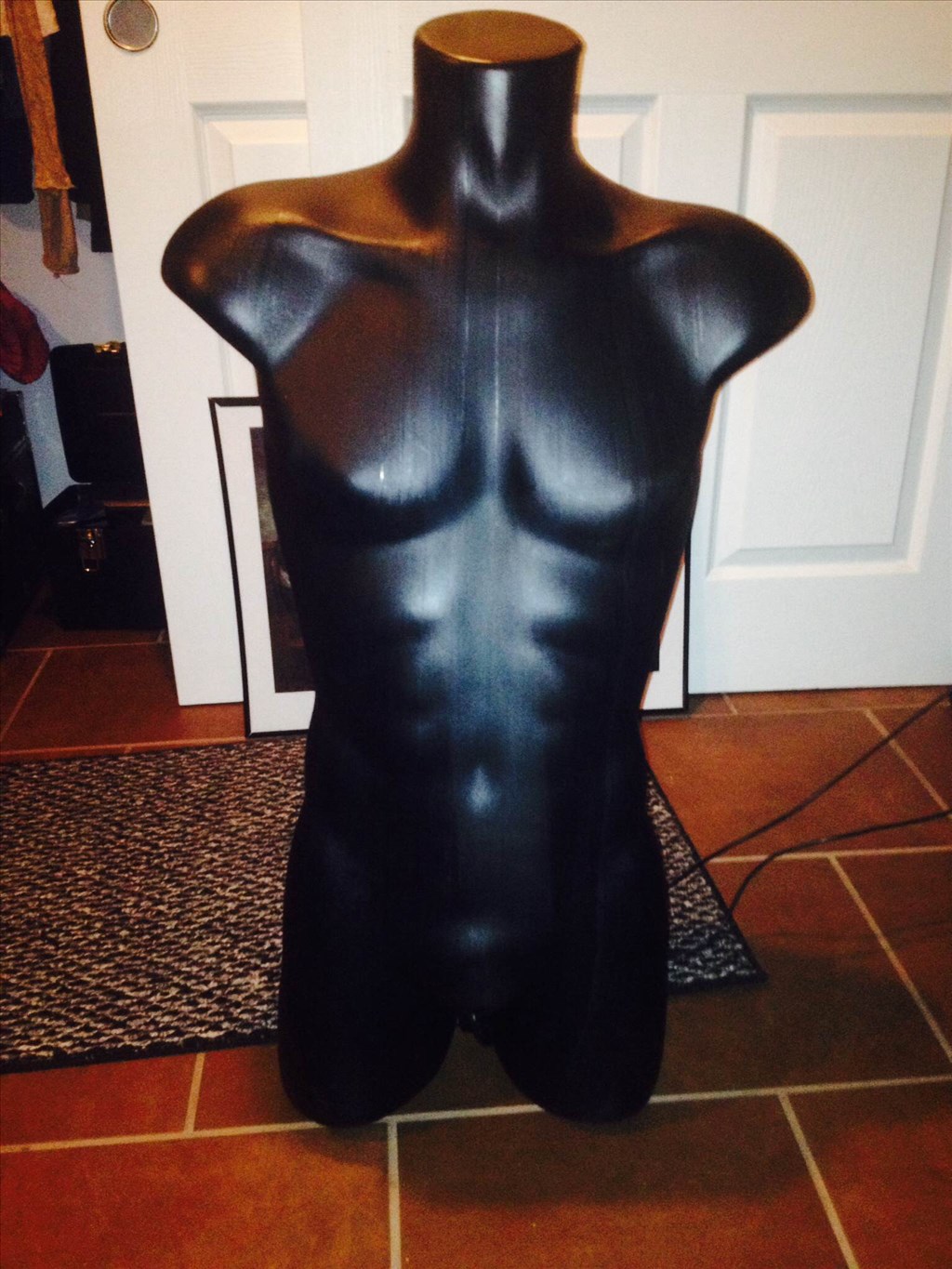
Kullthulu's J.A.R.V.I.S The Personal Assistant Bot.
So ive started constructing my Robot which ive named J.A.R.V.I.S I know there are several other bots that share this...
I think it looks good.
Mel
Thanks. It looks a little smaller than in this photo for some reason. Anyways I think it will add to his comical nature. lol
I really like it.
When I saw there was a headless Omni2000 on eBay I decided to go for it.
I thought it would go for cheap and it did. About $65.
looks very good,i kinda had a idea like it for mine too
@robotmaker They seem to be harder to find on eBay than Omni2000s. :/ I had an email alert for when it finally showed up. Also robotmaker I may be hitting you up later on recommendations for batteries and power charging system with an embedded PC board. It wont be as high end as Jstarnes though.
glad you where able to get him
@Glickclik - HEY! I was bidding on that headless Omnibot 2000 too! Oh, well, all's fair in love & eBay...
I'm just glad someone here won it. It was perfect to be EZ-B-ified.
btw, what is his head from again? What's it called?