I have decided to start my InMoov project. I think I will call him Spock out of respect to Leonard Nimoy who passed away on the day that I started this project.
I am editing this post so as not to confuse people with the current configuration. I continue to update this post with the latest photos. If you are reading this for the first time, don't be confused. There have been a lot of changes to the InMoov over the past couple of years including starting over.
https://synthiam.com/Community/Questions/7398&page=21 Post 203 starts the rebuild of the InMoov.
I have decided to use an onboard computer. I chose the Latte Panda due to it having an onboard arduino Leonardo and also because it uses little power.
I used 2 EZ-B controllers connected via the camera port to Adafruit FTDI friend boards. This allows the Latte Panda to have a non-wifi dependent connection to the EZ-B's. I use a powered USB hub connected to the USB3 port on the Latte Panda to attach other items.
The Omron HVC-P is used to identify people, emotions, human bodies, hands, age and gender. It is attached to the Latte Panda via an FTDI friend which is then connected to the powered USB hub. It is mounted in the chest of the InMoov. I also use a 3 element microphone which is a MXL AC-404 microphone. It is disassembled and the board and microphone elements are mounted in the chest of the InMoov. This mic board is connected to the Latte Panda via a usb cable which is attached to the powered USB hub. There is a USB camera in the eye of the InMoov which is connected to the Latte Panda via the powered USB hub.
I chose to use the Flexy hand with the InMoov. The design is far more rugged than the original hand and works very well. There are 4 EZ-Robot Micro Servos in the palm of each hand which controls the main fingers. The thumb is controlled by an EZ-Robot HD servo. The wrist waves and uses an EZ-Robot HD servo to do this motion. I use the standard Rotational wrist.
I have castle BEC's for power in the following locations set to the following voltages. Forearm's - 6.2 V - Controls fingers, wrist and elbows Custom power distribution board (2) set to 6.2 V controlling head, neck and Shoulder servos. EZ-B's - set to 6.1 V - it is mounted in the controller mounting plate and connects to the EZ-B fused power boards from a power base. Latte Panda - Set to 5.1 V and is mounted to the EZ-B controller mounting plate. Waist - set to 6.2 V and is mounted in the lower right side of the back. This provides power to the lean and pivot waist motors..
There are some custom power and signal distribution boards. These are in the forearms, lower back and in the upper back. The upper back or main board connects to these distribution points via USB cables to provide signal to the other boards for servos. The main board also has servo connector pins that are for the neck, head and shoulders. This allows the power to be distributed between multiple BEC's and also allows the servo signal cables to be shorter and more protected via the USB cables.
For power I use a LiFePo4 battery that is rated at 30 amps. It has the balanced charging circuit built into the battery and also has a low voltage shutoff built into the battery. This protects the battery and allows the battery to be charged with standard car chargers.
I put switches on the back on the InMoov which are rated at 20 amps at 12 volts. These are rocker switches that allow the user to pretty much slap the switch to turn it off. There are two of these switches. The servos for the elbows and fingers are on one switch. The latte panda, neck, shoulders, EZ-B's, waist motors and some lighting is on the other switch.
I also added a fuse block. This allows 20 amp fuses to be put in line to help protect things. The switches above drive the fuses for each of of the motors listed in that section.
Other robots from Synthiam community
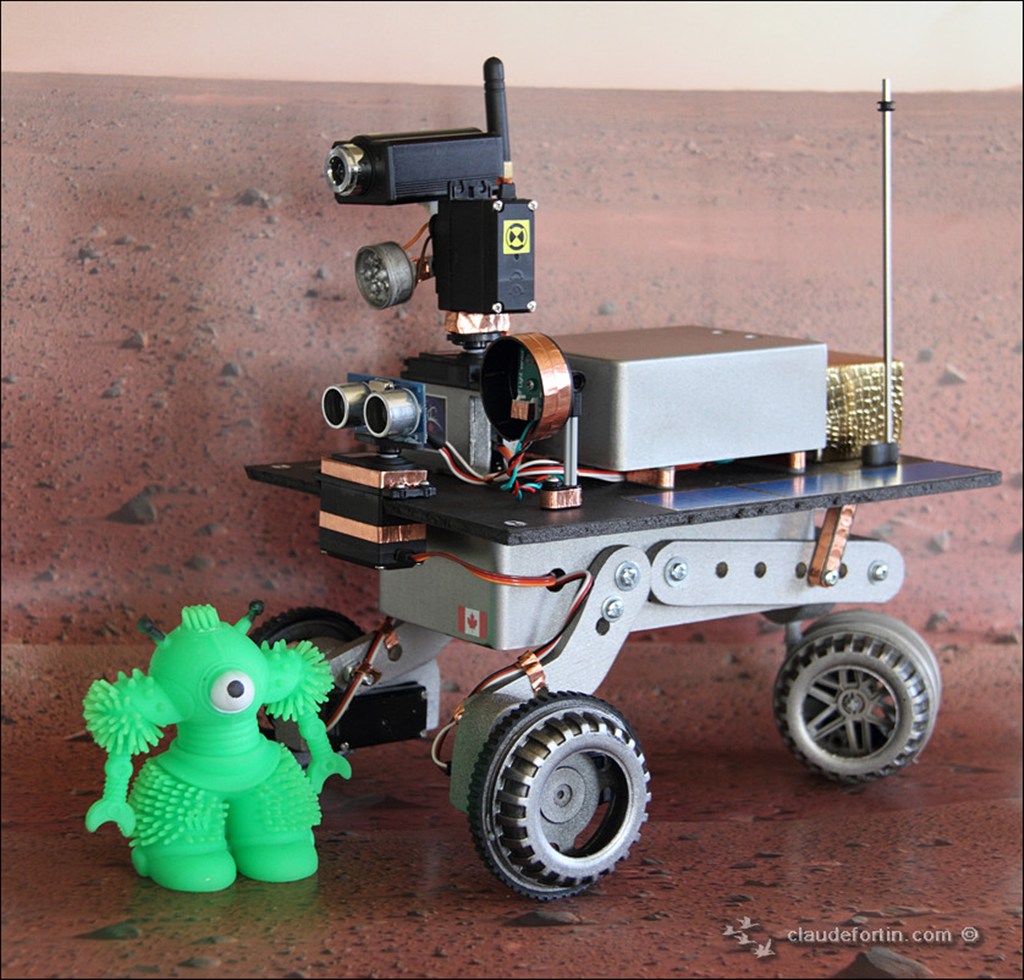
Clode's The Canadian Mars Explorer :-)
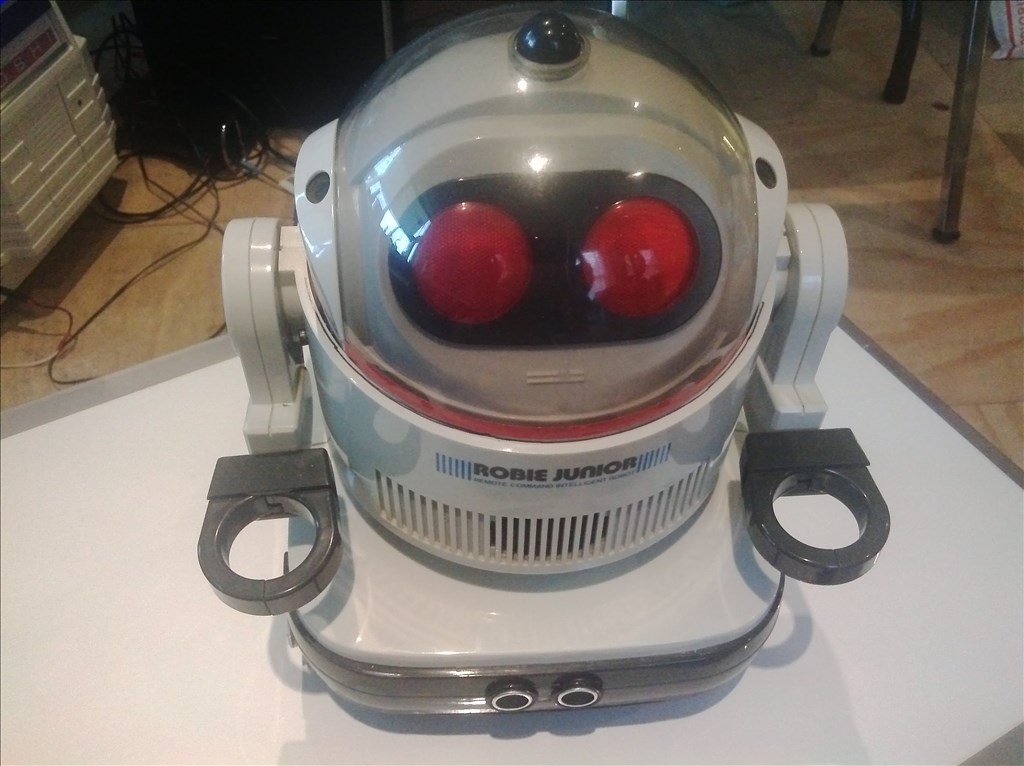
Rb550f's Romnibot
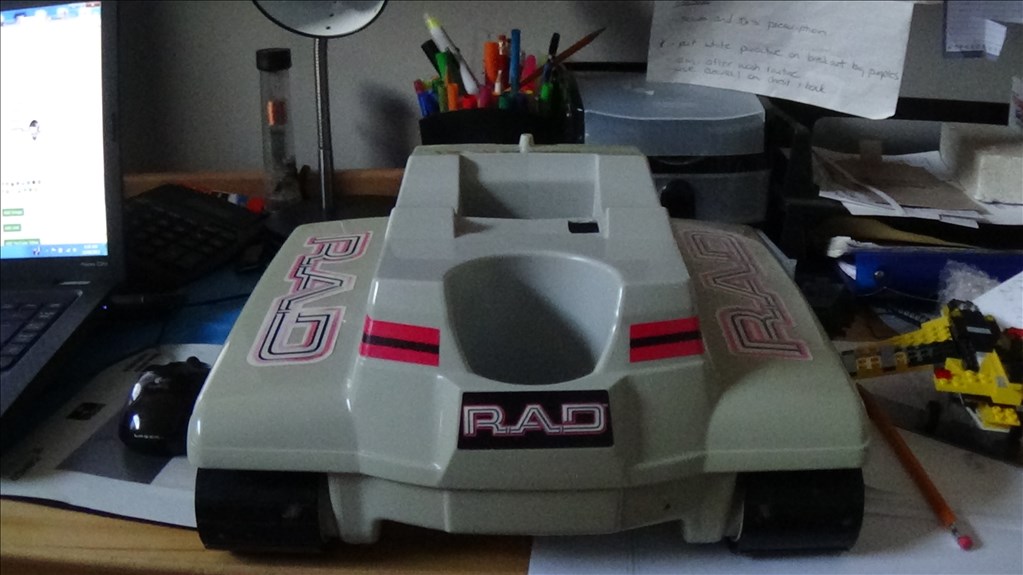
@David.... Looks like you're officially committed now.... Hang on while I make some popcorn then I am all yours.... This thread is going to be even better than watching old episodes of Macgyver
David, I am so glad that you are sticking with a robot build, your input into this community is great and I think a big build like this with your skill set will be awesome!
I am happy to donate Bosh servos, sensors, electronics and other stuff to your Inmoov build if you want? I think the Bosh servos (if converted for Inmoov) would make a fantastic improvement on the arms as the are virtually silent have zero holding current and have great torque.
If you want to make direct contact to discuss anything that you may need then here is my email address
toymaker(dot)tony(at)gmail(dot)com
Tony
@Tony.... The inmoov uses worm gear type gearboxes and a piston like corkscrew mechanism for the elbow joint... Although the Bosch motors would work better than the modified Hitec HS805bbs the arms as it stands now(because of the worm gear) don't really need too much current at all to hold their positions.... What would really improve with your bosch motors is the noise... Some of my large servos do buzz and it does get annoying after a while....
@richardr, The motors usually buzz if they are digital. Analogs have smoother action and do not buzz I understand. Of course, when I ordered a heap of them, I got digital. I always find out after the fact by making the mistakes.
@MovieMaker... No offence Mel, but you're educating me on servos? I was pretty much born with them in my hand.... The Hitec HS-805bb are analog servos and they are the ones that are buzzing... Their pots have been removed and relocated to the pivot point of the inmoov's joint... Because of this they don't position as accurately as they would if left unmodified... Hence the buzz... The digital servos I have in my inmoov's hands are dead quiet....
@Richard R, it's gonna be a fun build. I'm really looking forward to this.
@toymaker, thanks for the kind words and the offer. I will be contacting you later just to touch base. I would love to see what I could do with the servos. I love the design of them. I can think of multiple places that they could be used. I would also love to talk to you about the bumper proxy sensors you used. This robot will be used in populated areas around small children, and will be a mobile robot. That makes safety and a decent sensor array pretty important. These are all things you have already considered and handled.
David, I was also thinking about my ultrasonic array sensor hack for your Inmoov build. As the ultrasonics are from car reversing sensors they also work great outside and do a really good detection job.
If you do not mind me enabling code protection on the custom PIC for this, I could send you out a couple. I have to use code protect as I am doing this development commercially so cannot afford to just give away my work as it will probably end up getting used in competitors product.
What the PIC does is to convert the odd "bit bang" serial from the reversing unit's control box and converts it to I2C which can be easily read by the EZB v4 so you get the distance in meters for all four detection zones. These units are so cheap at around £10 (with weatherproof sensors) and good quality build, they work really well for a wide angle (4 zone) ultrasonic sensor array. My PIC also sends out all the distance data to a I2C LCD display as you can see below, this is very useful in setting it all up.
I not sure all the different car reversing units have the same "bit bang" serial, I get the feeling some may be different, so some may not work with my PIC. As the unit I used was so cheap, I did order 5 units off ebay and have a spare that I can let you have so you know it will all be compatible.
Richard R, same offer for your Inmoov build if you are interested?
Tony
@Tony, that would be awesome. I will definately take you up on this offer. I haven't even made it out of bed this morning yet. When I do, I will send that email I promissed earlier.
Turn on code protection. I have actually taken my source for EZ-AI off my site. It is getting pretty powerful and I don't know where it is going so, I might keep how I am doing some things a secret. I will always give away the compiled code or a version of it if it goes far.