5.5 foot tall humanoid robot that walks and talks.
56 servos controlled by 3 ezbv4 boards working together over wifi.
On board power supply lasts 1-2.5 hours depending on activity: 7.4v 5a lithium battery for logic and smaller servos and 11.1v 10.5a battery for everything else.
DOFs? all of them
Been out of the ez-robot loop for awhile, and I have to say I like were things are going with synthiam. Plan on taking full advantage of having an onboard pc, and will be converting to arduino in near future.
Very interested in bipedal gyro control and scripting if anyone has advise on the matter.
here is a link to my project design on grabcad: https://grabcad.com/library/hal-the-robot-1
By cliffordkoperski
— Last update
Other robots from Synthiam community

Thefoolmonty's Joc's Ucontrol Wall-E
Still a work in progress and I have not decided finally on some aspects. While this is basically the same implementation...
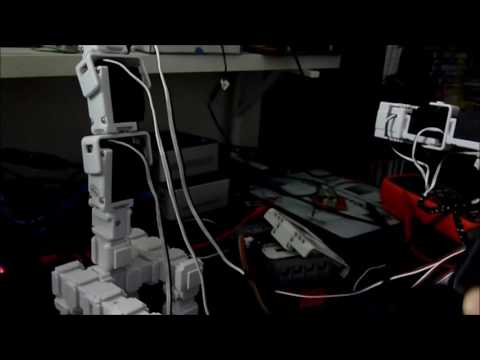
Fxrtst's ARC, Depth Sensor Plug In And Perception Neuron
A little back ground. Besides make up effects, I started teaching myself computer animation about 20 years ago. About 8...
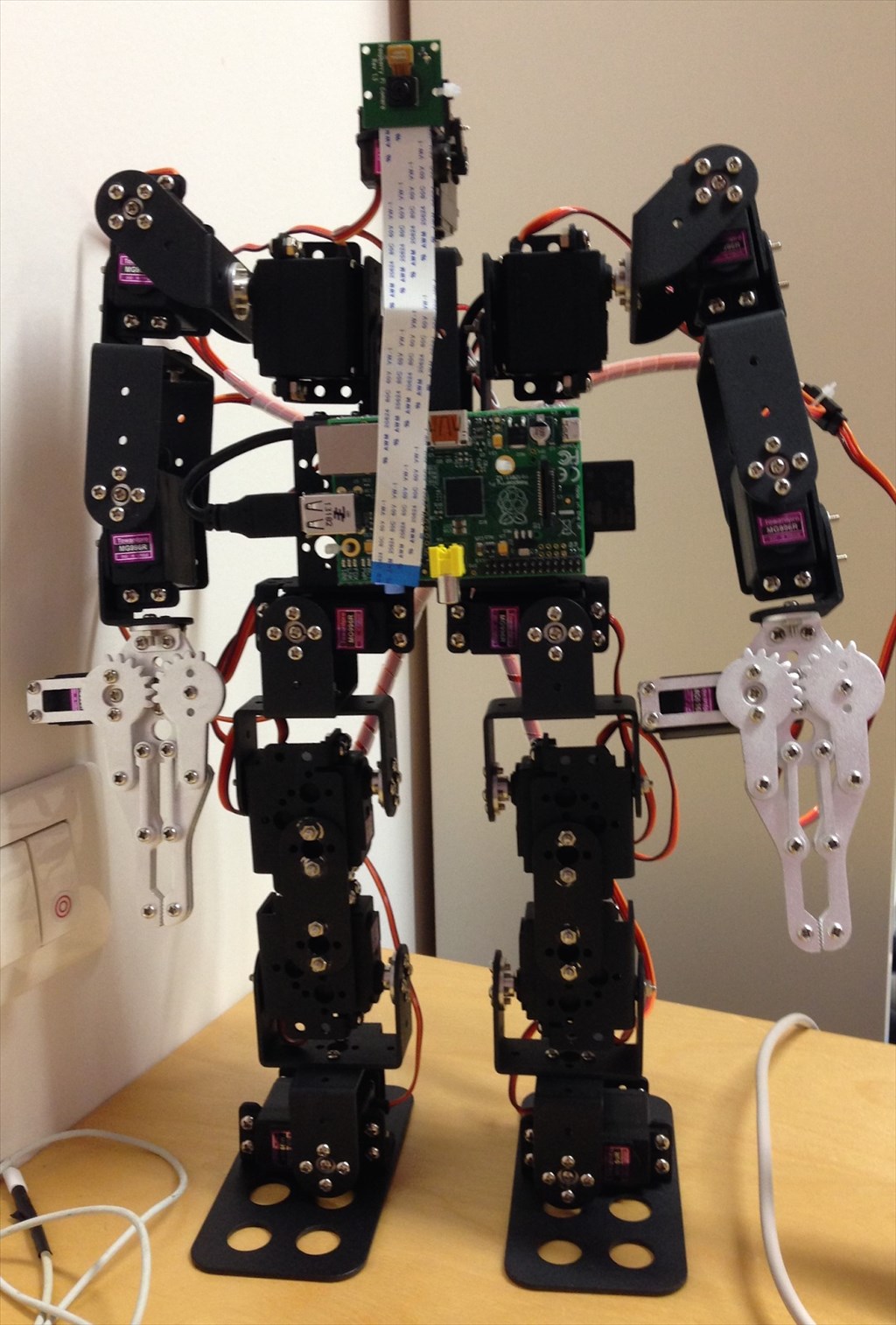
Crivellarodiego's How To Automate The Robot
Hello I state that I am using the product from very little, I would ask how I can create the project in ARC for the...
very good, nice work
@cliffordkoperski Very impressive, I was checking out Grabcad.com, I am sure there will be lots of questions, from the members, and yes Hal's walking would benefit from gyro control. but making first steps is still very good. more information about Hal's hand design would be my first questions.
Very cool robot. If you get some of the SSC-32 boards you can control 32 servos from each board using ARC. My robot Dave is much shorter and I never got him walking yet. I may need to build one about the same size as yours next.
Very impressive, and the linear actuators make the moments a lot smoother and quicker than standard Servos. Must of been expensive!!
Wow very cool bot,reminds me of the Terminator the way you got the legs! Hands are nice too and I know how complicated the walking can be with balance so congrats!:D
All I can say is WOW! This is one of the most ambitious projects I've seen in a while! Thanks for sharing HAL with us, I will definitely be following this thread for any updates.
I'm very interested in the back story of your creation, I see you had a thread back in 2016 about the arms, you must have been working on this project for quite some time. @Cliffordkoperski if you have some spare time please share the story of HAL with us.
Thanks for the positive feed back! The back story on this project started with some R&D work on producing a robust human proof industrial robot design, resulting in the 2016 thread on a arm controlled by hydraulics. The hydraulic concept proved messy, expensive, and overly complicated. Ironically about a month after scraping the project I found an article published by NASA back in the 60's on how they designed an entire human sized hydraulic robot which failed for the same reasons, wish I read that before hand. So in 2017 I decided to go electric, I bought some dc motors with a built in worm gear reduction box, and converted them in to servos using pots and syren50 control boards from dimension engineering. I also found detailed machining blue prints for making the hollywood terminator hand and forearm so I custom machined that out of 303 stainless steel and came up with this youtube video posted bellow.
Electric was definitely the way to go, but if I were to build an entire body with these motors the damn machine would weigh over 500 pounds. So I scratched my head till 2018, then decided to build "HAL" out of cnc machined 6061 1/8 inch extruded aluminum plate, and use hobby grade servos and actuators bringing the build weight to a little over 85 pounds. The HAL design is not as robust as I would like yet but the original goal is a few tweeks away. I believe the HAL robot design could compliment or even serve as an alternative to the inmoov project and can be easily 3D printed, cnc machined, or laser cut and I encourage others to copy my design and even perfect it as they wish. I can download cad models of individual parts if there is any interest.Very awesome machine! would be great to see how you desined it. Am workin on a project myself that is to have a 150 pound lifting capacity to aid in human care at home.