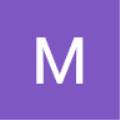
mbrooks
Australia
Asked
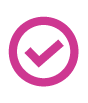
Hi .. I am new to ARC platform. I have successfully created a project and exercised servos. I know I can add DC motors via the Sabertooth controller .. my issue is that I would like to use Stepper motors (using a single Ez-b channel per stepper) .. I use the Pololu Tic T500 'smart' stepper controller which provides interface options:
- TTL serial
- I2C
- RC hobby servo .. so my thought is that I could 'add' this T500 + servo into my Ez-b project as either a:
- vertical servo or
- continuous servo .. and the Ez-b will treat the T500 + stepper as if it were a servo which is exactly what my hobby RC radio does.
Please advise if I am taking the correct approach here? Or should I be using this robot skill https://synthiam.com/Support/Skills/Servo/Stepper-Servo?id=21134
Related Hardware EZ-B v4
Related Control
PWM Slider
Please advise difference between ARC and ARC? I am only familiar with the ARC utility, do you have a link to ARC pls?
Actually .. pls disregard my last question .. I just found ARC and understand it to be the evolution of ARC
I don't know if this helps but:
Did you see my car
Parts: IO tiny, ARC, Ez-battery - L298N Motor Drive Controller Board Module Dual H Bridge DC Stepper on Amazon, you can get 5 of them for 12.99
https://synthiam.com/Community/Questions/H-bridge-for-4-motors-robot-car-18995
I also have used the A4988 StepStick Stepper Motor Driver Module + Heat Sink
Details of ARC are posted here: https://synthiam.com/Products/Releases/ARC-Beta-2020-01-27-00-19052 Download is from the same page as ARC.
microcontrollers generally have 1 uart, if at all. Multiple aren’t usually needed unless you’re talking to many different things. In your case, the documentation of the Tic allows multiple to be assessed. That makes it possible to use one uart to control many Tic’s.
you will have to modify my code example to use the 32bit block commands? Something like that... again, they’re documentation is super wordy and isn’t direct like a normal data sheet would be. I don’t think I’ll have time to read their novel haha but I’ll try to help as you go along. See if they have a forum that you can ask.
ideally, an ARC skill plugin for the tic would be easiest because you wouldn’t need any code at all.
I agree the documentation is verbose and the controller is a smart allows multiple configurations.
@EZang: Does not help your setup does not use stepper motors, and the cheap/affordable controllers can't be used with EZB to drive step motors, although you can use Arduino code, we are discussing different setups.@All: Maybe I missed something, if the goal is to drive the step motors like DC motors (with velocity control) it's not easier to configure the controller for PWM and use the Continuous servo control ?
If the goal is to emulate an absolute position servo, then you have 2 setup options:
ptp, you don't require a potentiometer with a stepper motor - that's why it's not mandatory for this application. If the physical design doesn't account for a potentiometer to be installed, then a stepper motor can still operate as a servo. This is because it moves via steps. So you instruct how many steps to move in either direction. Keeping track of those steps and related them to a servo position works.
For example.. Servo 1 degree = 0 steps Servo 180 degrees = 100,000 steps
So if you move to a specific position, you'll need to keep track of where you were and how many steps to get back.
@DJ, the main question is how you want to control the stepper motor ?
velocity control you can emulate Continuous servo
positional servo
Pololu offers 2 different methods:
2.1) add a potentiometer can be a multiples turns connected with gears and you have absolute position and then you emulate a servo configuring the PWM interval
OR
2.2) add home switch, and the controller handles everything for you:
Continuous/Velocity servo or a Positional servo (with additional hardware) you can emulate a RC servo and connect to an EZB digital port without any extra code (JavaScript or EZ-Script) so the question still stands the OP has one smart controller and can emulate a PWM servo makes sense more advanced scenarios (e.g. UART or scripting) ?The application of the stepper motor may help determine the best way to drive it.
Is it being used for driving wheels on a mobile robot platform or on a rail system where limit switches can be used?
Is high torque a requirement? Steppers usually have low torque unless a high voltage (24V) is applied. High voltage is difficult to use on mobile robots.