As promised I've started a separate thread on this. I had mentioned over at my Alan thread that I was thinking about using hoverboard motors for a rolling base for the full bodies of Alan and Alena. These motors are super cheap at about $25 a piece on ebay. They are 3 phase just like the 3 phase hobby motors for cars and planes. So there should be driver support for them.....well yes and kinda no.
I have been watching a motor controller called the ODrive. Its all open source (hardware and software) and its a dual motor driver. I posted a video of these motors on a grocery cart driving around using hoverboard motors. So I bought an Odrive. I ended up buying a whole hoverboard so I could use the charger, battery and some of the connectors. This one came from Frys and cost $100. Its good upto 265 pounds.
Well now the bad. The ODrive is still a work in progress and not too intuitive. But they have a good write up on how to set them up with the hall effects encoders. All went well until I tried to save out to the board. Over and over again i could not get it to work right. I posted on the forums and got no reply back as to what the issue could be. So after days I began looking for another solution.
I found a great source in china that is making opensource stuff for skate boards. The got 2 single motor drivers. Each one has a standard servo connector and i can use two of them for mixed mode (tank mode). Each board costs $85. So its a bit more than the ODrive ($150 with shipping for the 48 volt ver.)
The name of the board is the FSESC 4.12 50A Based on VESC 4.12 from Flipsky ESC. And can be found here: Flipsky ESC
This controller can be completely programmed with their really great software..automatically figures out all the poles for the phases. Set up the frequency for the pwm and even have shut offs for voltage mins etc. They have a good youtube channel with vids on how to set up everything.
I have the video of the break down of the hoverboard done. As soon as I get these control boards I will be doing tests with the ezb to control them. Then I'll put together a final video and post here.
Other robots from Synthiam community
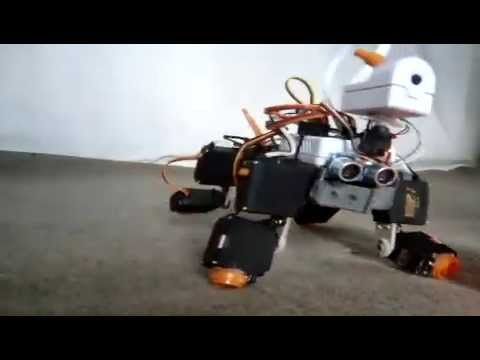
Ericez's Dog The Little Robodog Ez-B V.4
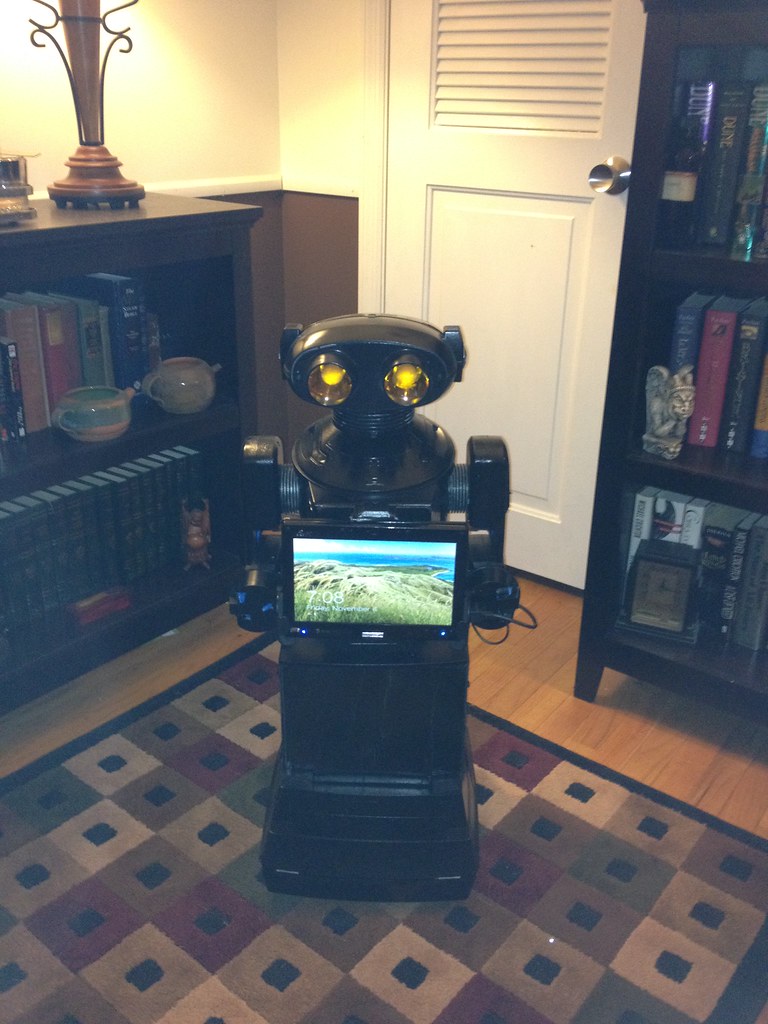
Confoundedhound's Modified Omnibot 2000

Oh man!!!! I’m so jealous you’re doing this robot hack. I’ve had my eye on something like this for a while but time has been a rare luxury these days
in the meantime, I’ll continue living vicariously through you!
You think its legal to strap your kid to this as a go cart and drive him (with a helmet of course
) as fast as i can down the road controlling from my Iphone.....lets find out!
Hi Will, Brave kids with a fast go cart controlled by Dad ? Sounds Great ! Normal to me... Thanks for starting the new thread. Are the motors normally 48v? I thought 12v. The controllers sound interesting. I am looking forward to your progress. As soon as my work projects let up, I hope to begin with the base unit also.
Will, we have no Fry's near me here on the East Coast. Could you tell me what the Manufacturer name of the hover board you got is? This way I will be able to share my ideas for the base using the same components.
@Andy The motors are actually 36 volts. The controller I got from Odrive was rate at 48v...meaning i could use motors up to 48 volts. . The voltage is higher than 12 volts because those hoverboards carry 200 pounds, 7 miles an hour for 6-12 miles! Its incredible when you think about it. I can hold the lipo battery pack in one hand! The Flipsky controller allows you to use motors from 8v-60 volts upto 50 amps per channel.
I'm using a hoverboard called the Prime R6. Its some generic hoverboard...but i got it because it was on sale and it can carry 265, which is about 40 pounds more than most. The manufacturer has it on sale for $144 reg $349. But you might be able to find a better deal elsewhere like I did.
Thanks for the info Will. I haven't done my homework on the motors, battery or esc. I am hoping for some free time soon to start reading up and ordering. I think I have seen the hoverboard locally and will check it out. My end goal is to build a base with navigation (hopefully based on the unit DJ will release soon).
...yes we are thinking along the same lines. In fact this should be a good demo for InMoov, and any robots that require a basic mobile base to build upon.
Hopefully with the hall effects encoders there can be some good positioning. My biggest fear is not being able to control both motors equally. Meaning if one motor moves slightly faster than the other it will not drive straight. So there will be some challenges ahead!
To carry 265 pound loads and travel many many miles was the plus of what I saw too but then got put off at the extra costs and complications as this is new ground for using in a robot but glad you are doing it,lets see how it can be done!
Speed matching vs slippage is always an issue on something like this. The sensitivity of DJ's Nav system should compensate. Update timing can also help. I know the top speed will be relatively low so the heading refresh should be able to adjust. I also need to refresh my brain about PID loops? They may help with this? Ptp may know.