Now I have the EZ-B kit and the Hearoid it's time to start my Showcase thread.
I still haven't decided on a name for him yet, all suggestions are welcome.
I won this robot on ebay weeks ago, for the past 2 weeks he has been waiting for me to collect him...
Today was the day, a road trip to pick him up and bring him back to his new home...
In his new home (with Omnibot and Wall-e in the background totally unaware they are next in line to be opened up)
It wasn't long before this happened...
Now waiting to go in the dishwasher to get nice and clean.
The plan is to make him autonomous, running 24/7 (except for when he knows to go charge himself up) but will also be adding in the various image tracking options.
The only other slight modifications to be made to him are to convert the head to tilt & pan which will involve having to give him a small neck.
The head will include the camera. I haven't yet decided to fit it in one of his eyes or to make it his nose. The issue to overcome with this is the blue tint on the bubble head. The mouth will have a light or some lights in which flicker when he speaks.
The arms will be given some life with servos at the shoulder joints and the elbows provided I can get them to fit in there nicely.
Ultrasonic sensor will be in his chest, probably on a servo to give a wider view.
Original drive wheels and gearbox seem to be in very good shape so will plan to reuse those and just replace the existing motors for the modified servos if they can manage the task.
Speaker and microphone will be in the original positions - if it's not broke why fix it?
Not too big a project but enough to give me a test, help me learn and bring an old robot back to life.
Other robots from Synthiam community
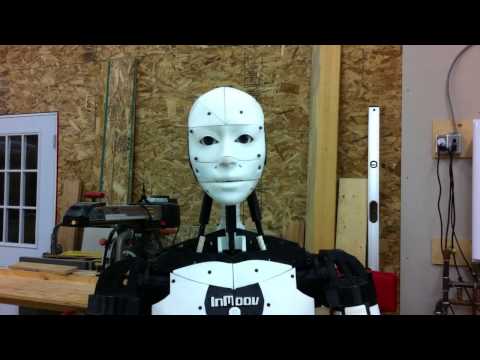
Bhouston's A New Dof For Inmoov's Neck/Head
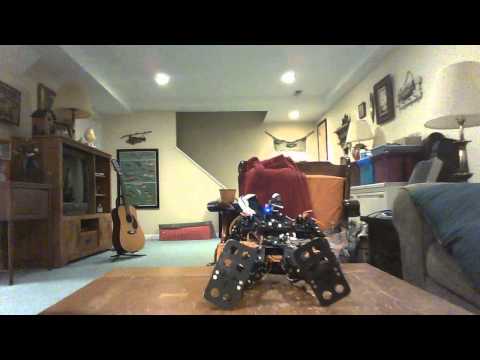
Cliffordkoperski's Cliff Robot
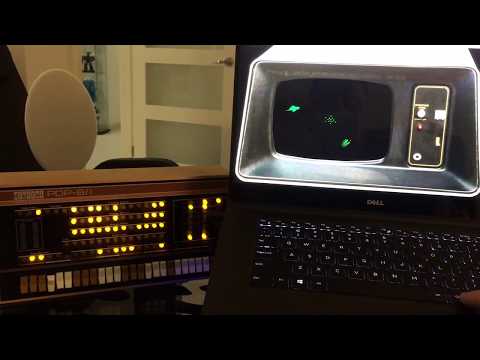
Let me be the first to say thanks for posting this thread. I really like that model robot and you got a nice one! He has a really cool looking face. I am looking forward to seeing what ideas you come up with and how you impliment them. Good luck, have fun and we will be watching!
I love this style robot and the rad robots too. If your going to run him for long periods then a larger battery is in order. If you stay with 6 volts power sonic and other brands make a 6 volt battery that you can easily fit two of in the bottom of your robots torso. Two 6 volt 12ah batteries means 24ah of capacity.given the original battery powered the omnibot for almost an hour you could have 2 to 4 hours constant run time between charges
. Also I've seen great success from other members telling the robot to follow a glyph and getting it to dock like a roomba face first.
The battery is what I'm currently looking in to although it's the last item on the shopping list - for now my ez-b is powered by a mains transformer for testing everything. Once I've got the robot back together with everything else in there I'll have a better idea of the space available for the battery/batteries but it looks like there is going to be more than enough space for them.
The batteries and charging station will be the last thing I look at though. I'm more interested in getting the robot back together, looking like new and moving around again.
My biggest problem at the moment is the face. The blue tinted visor is no good if I want to use colour tracking as the camera will be behind that. I need to either find a Robbie Sr. head (if it's the same size which I believe it is?) and use the visor from that, see how it looks without the visor or attempt to mould my own which may be beyond me.
Besides, the blue visor is scratched and washing it has showed those scratches up even more. I may try to polish them out if it's possible but I have limited experience with that.
I've ordered a mini tilt/pan bracket, it uses mini servos but hopefully they will be powerful enough to move the head, if not then I'll find another way of doing it.
Have rewired the camera from the EZ-B kit to be powered and switched by the EZ-B, although my soldering iron was playing up and only getting hot enough to just about melt the solder so I'll have to redo it. It works but I'm not happy with the soldering. I think it's time I invest in a better soldering iron (mine is just a cheap gas powered thing).
Half of the robot is now clean, the other half is in the dishwasher being cleaned now (small dishwasher).
And I've got a bunch of servos, mini servos, cables etc. on order now too so plenty to play with.
Welcome to EZ-B! I love the Hearoid, but could not find one so I did the omnibot. Here is a link to my build - it may give you some ideas.
Bob was completed and now I've gone back into him to make Gunslinger Bob. Good luck with your build!
@Bret your project is going to be a great help to me as are all of the Omni projects, the body is the exact same so other than my pan/tilt head modification which I think I have figured out.
The Hearoid wasn't my first choice, the Omni was. But when I bought my Omni (after over 25 years of wanting one) he was in such good condition I didn't want to take him apart. Looked for another Omni to modify and come across the Hearoid... I love the head, it just makes him look that much more human like, which is why I really want to figure out a way to make the blue tinted visor clear (well, either make a clear one or find a Robbie with a good condition one).
I love your idea of the EZ-B in the cassette drawer, that's an idea I may be looking at "borrowing"...
I'm currently trying to reuse the original drive but replace the motors for modified servos... I'm thinking opting for a HBridge would be the easier option... But I haven't given up yet...
Rich email me real quick [email protected]
@Josh - head swap?
Maybe so , trades are great