Other robots from Synthiam community

Drephreak's New Robot
Hi Fellas. I havent been here for a while but have been keeping up from time to time anyways I wanted to introduce my...
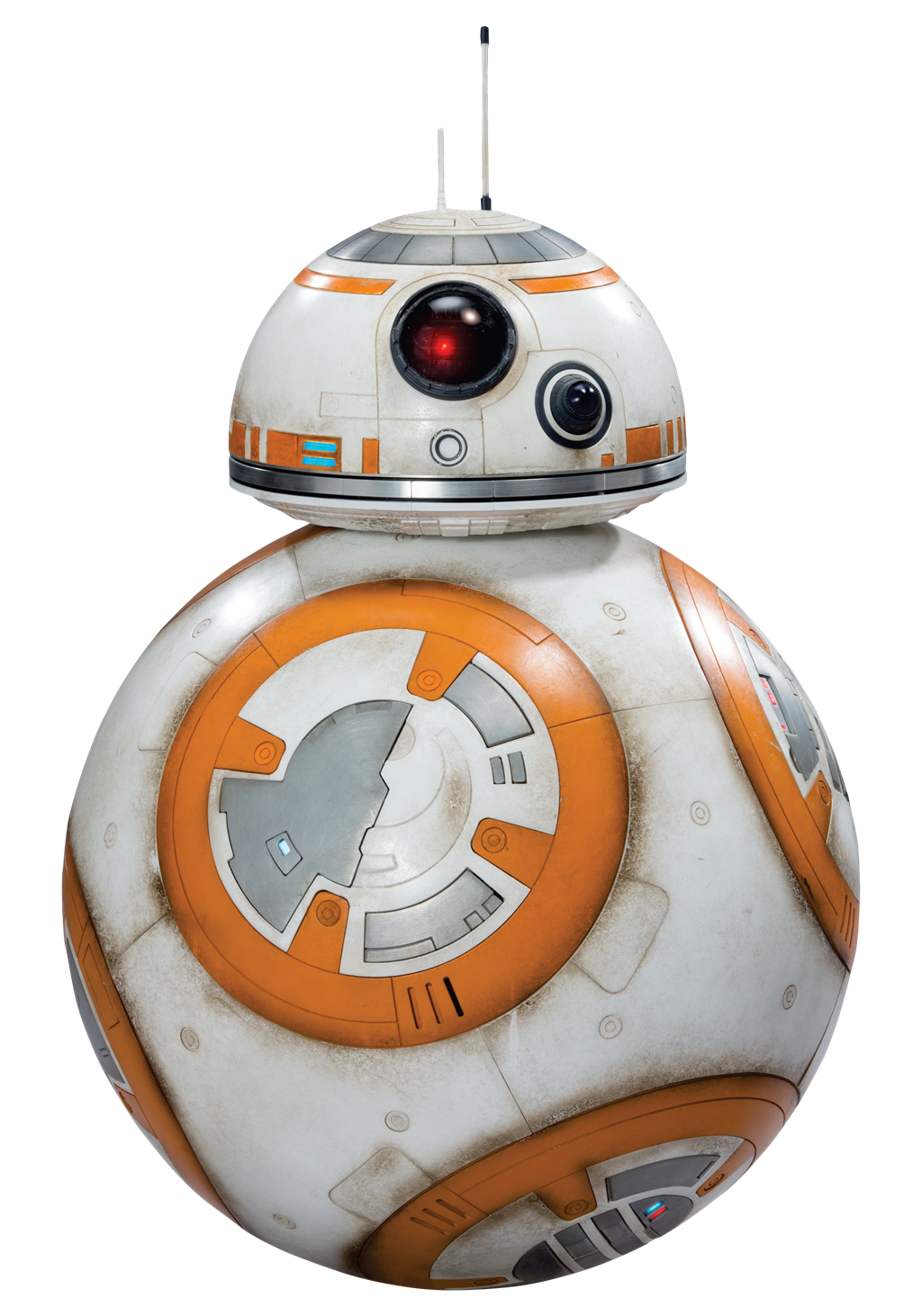
Johnnypipey's Bb8 On The Cheap Project
Hi This is my first Real EZ robotics project (other than just playing around with the system) Aiming to recreate BB8...
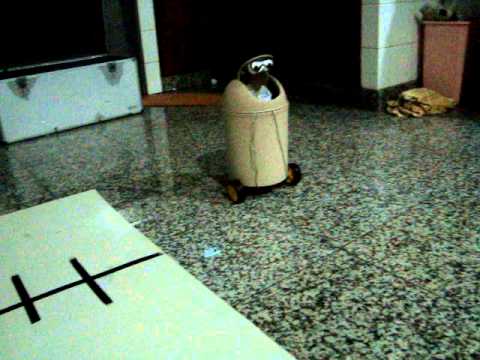
Ericez's Smart Cute Trash Can
not finished, but it was my idea to make smart trash can, This is just an experiment, later I plan to make a trash can...
You have Eve and the Apple, where's Adam ?
:)
I think it's a good idea for window display although the price is prohibitive.
That's a neat idea for interactive clothing displays. I really like that idea and hope this business product works for you.
To start, it may be useful for video demonstrations which will provide visual example of how the product looks in a retail setting. If you could locate a local clothing retail company to be your test pilot, that would be a good start for a video.
Having the robot move into different positions or follow motion through the display glass. Or introduce the outfit and explain to the user with a recording why it is comfortable, etc...
Or even have a tablet control the robot so customers can pose the outfit manually to see what it looks like.
I remember to see a youtube video they used a few mannequins, some sensors and or cameras to create an interaction with the shoppers.
It was very cool.
Thanks for your ideas guys. I don't think the price is prohibitive. It would come with a warranty. I wanted to sell them for $2500 when I began but I was dreaming. I've spent thousands of dollars and thousands of hours on it. Even now, each one costs me around $6000 to make (not including labour). Shipping parts from the United states and our bad currency exchange rate as well as import tax make the costs add up. Some parts take 8 weeks to arrive from China. My parts are 3D printed but I want to make them either aluminium die cast or injection moulded. There are around thirty housing pieces even without legs and fingers and faces. Each mould costs at least $15,000 to get made before a single printed part has been fabricated. To make these en masse I will need hundreds of thousands of dollars. Think of how much Zara and giant retail outlets spend on signage, not to mention fashion shows and expos. These robots will have swagger when I finish with the hip rotation and legs. And yes, I'll definitely make an Adam. He'll probably be a fighting robot in some kind of Arena Wars gambling situation. I'm still tweaking Eve at the moment. I wouldn't mind making a few for Disneyland, either. The pan servo gears are difficult to centralise in a 60mm cylinder. That's why I've commissioned new servos to be created from scratch with centered shafts and other cool features.
Here are some mannequins who aren't even dancing. Let's cheer them up.
Earlier prototypes:
Noise levels: https://www.youtube.com/watch?v=t_racaVZKNc&feature=em-upload_owner
Replacing desktop computers with a household butler and a projector screen is the ultimate idea. I'll use pandora and allow the online community to vote on a growing library of responses.