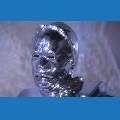
RoboHappy
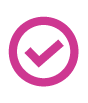
Hello folks, Figured Id throw this out there and see what others think...Has anyone ever had to install the EZB Ultrasonic sensor (or any other sensor) far away from the EZB? for my current bot project I am working on, I need to place the sensor far away from the EZB, like 40 inches away, due to the current size of the robot. I know the short 3pin servo wire that comes with the sensor works fine, and the signal looks good on a scope. Next I tried a longer wire, some 36 inches. It still worked, and still gives readings on the EZB software (the latest and greatest version). What I did noice on the scope was a lil bit of noise on the echo/trigger line, about 1.6V yet it still produces a typical 5V square wave, but the accuracy of the readings is a lil off. Just wondered if anyone ever tried a longer cable and maybe had to add some filtering to the power or signal lines of the sensor to clean things up. The robot is over 5 feet tall. this one sensor is to be located at its tracked base, and am planning to put the EZB in the head.
Use a twisted pair cat 5 Ethernet cable. Inside a twisted pair are many sets of two wires twisted together. Run a gnd wire on each of the one pairs. Run the signals and power on of the other pairs.
that way, every signal or power wire is twisted with a gnd wire.
you won’t have any noise... and it’s cheap wire to buy build with no end connectors
.
Sweet, I will give that a try next, thank you DJ :-) I know its crazy that I am running such a long wire but its what I need. I will be posting a pic of the robot soon too.
Great I ran into a problem running a very long wire for the ultrasonic sensor for a garage project. It just wouldn't work with that long of a run. Please let us know if this works for you RoboHappy.
Here’s a good discussion on the magic of twisted pair: https://www.researchgate.net/post/What_is_the_basic_idea_behind_the_twisted_pair_Why_are_the_two_wires_twisted_How_does_this_arrangement_compensate_undesirable_disturbances
remember, this only applies to maintain the differential voltage. That means each pair needs at least one ground, while the other wire of the pair can be used for signal/power.
@DJ, That makes sense with differential communication like Serial communication RS485 (Dynamixel), Ethernet/Lan, DMX, but, the question how do you apply a differential concept that to a single PING RX and/or TX Line ?
It’s the same. The difference between reference voltages. Which is exactly how serial and binary communication data works. Even if it was analog it would still apply. Because the system needs to recognize differential between reference and high.
again, ground on every one wire of each twisted pair, with a signal or power on the other of the twisted pair. I can’t repeat or stress that enough or it won’t work.
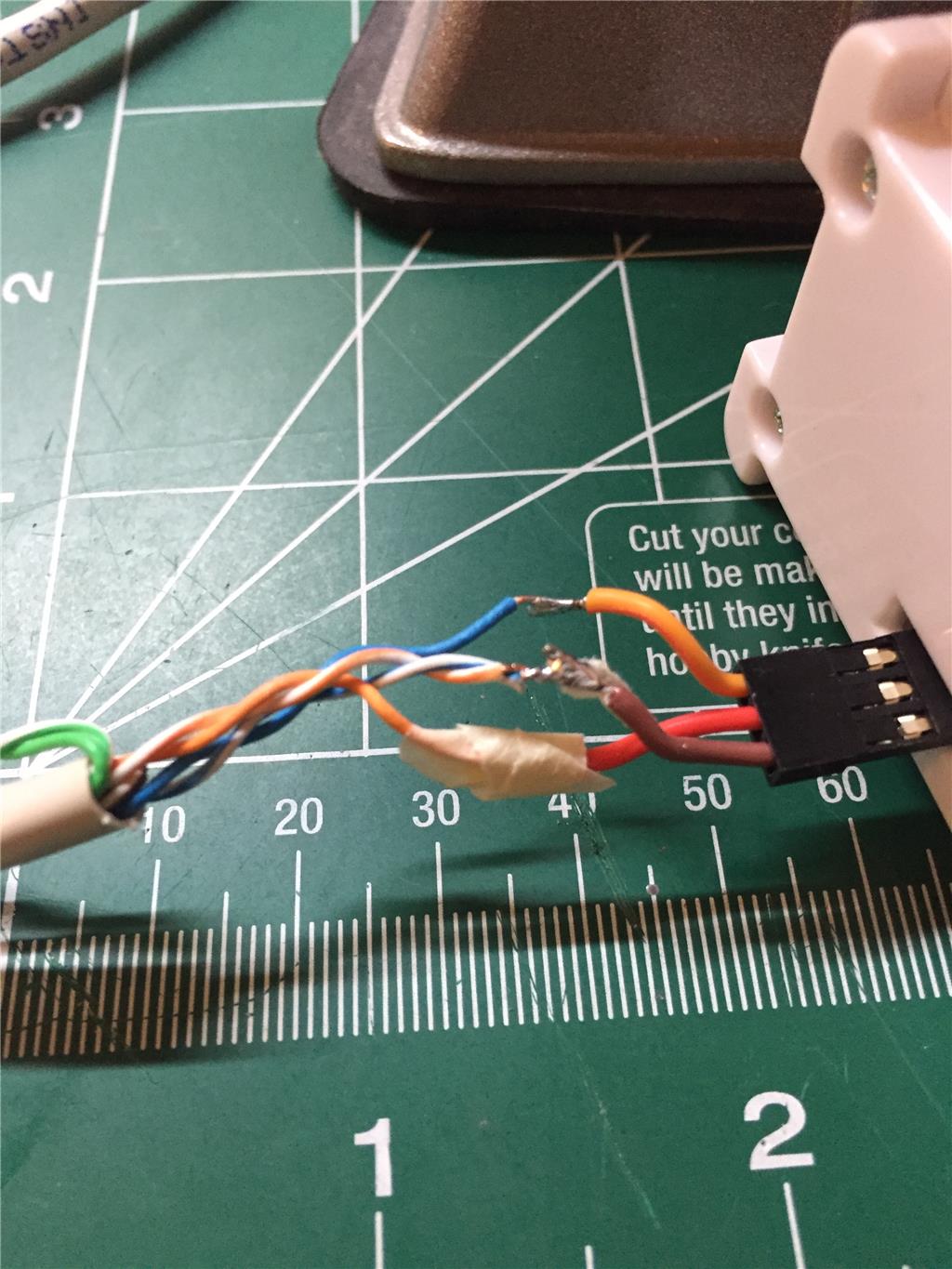
Hey folks, So taking DJs advice, I could not wait to get home and try it, The above picture shows how both ends of the 3pin servo connectors get wired per DJs recommendation (please excuse my sloppy soldering,lol)using some Cat5 , The wire length I used is 6 feet (72 inches) and yes was pleasantly suprised at the results. My scope showed a nice 5v square wave, each time the sensor was aimed at something, and the noise I first experienced was only 720mv on the data line. So yea... This worked and is what I was aiming for. Thanks again Dj :-)