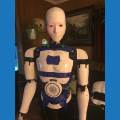
Perry_S
USA
Asked
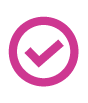
I have been rethinking this company as they evolve. I see a trend to supporting other hardware platforms which is awesome. I always just associated the software with the EZB project. So as the software morphs and has been doing, what is the best optimum hardware to run it on now? Is it still EZB or Raspberry Pi, or Arduino, or whatever? What if I wanted a really high performance system that ran ARC. What would I use? How far can this be pushed?
Related Hardware EZ-B v4
Guess it depends on how the computer and i/o controller (ezb) are connected. We're working on a Docs section that includes a Getting Started guide that presents a few scenarios based on this question. Meaning, is the computer remotely connecting to the io (ezb) controller via wifi? Or is the computer installed inside the robot and connected to the controller via USB?
The new Docs section should be up by the end of this week. We have two staff working on populating it now - and they'll continue to add content to it over time. The idea is to present more technical details, such as questions like this.
Personally, I've been quite fond of the Up Board because it is so affordable that it's priced similar to the raspberry pi - with 10 times the performance. We're most likely discontinuing the raspberry pi version of the software in the next few weeks.
The EZ-Robot EZ-B v4 is a great controller, but if you're installing a computer in the robot, there isn't much point to the ez-b v4. The only advantage to the ez-b v4 is having connectors directly for servos. The alternative is using any USB servo controller (such as the ssc-32, etc). Having the PC embedded in the robot also means using a real sound card for high quality sound with proper speakers. That's something the ez-b v4 doesn't offer.
There's a number of other things we're working on - such as a new servo animator that Will has been asking for. It allows moving the servos in various algorithms to obtain realistic movements by varying the speed. A few other things is a universal lidar and slam component, so any lidar's can be added. And the aiml2 control. And a few other things... So having a PC inside the robot is going to be very useful.
Oh, and another alternative to the intel up board is the latte panda. It's good to but a little harder to get hold of. Always seems to be out of stock
Hi @DJ,
Just adding my two cents to the discussion.
I am a little disappointed to hear that. When my Latte Panda card died (it is a really fragile little beast), I bought a RPi because it was supported by ARC and I thought it was a great idea to associate ARC, one of the most powerful robotic software, to the most widespread mini computer, with a very active community. I agree that the UpBoard is an interesting and powerful solution, but it is not really the same budget than a RPi (for the same quantity of memory and storage, the UpBoard is twice the price of the Rpi 4) and not really the same positioning (the RPi offers other opportunities outside ARC for robot builders). So I don't think it would be the same "market"But I fully understand what can be the difficulty to maintain two different versions of ARC on the long run and that you have to make strategic choices for Synthiam.
It is just that I liked the idea to have a fully functional ARC software on the Pi (and more globally on Linux platforms)...:)
Personally, I like the ease of the EZB. You can hook up to 24 servos and a cam and off you go for a quick test if need be.
I'd say the EZ-B 4 and the EZ-B IOTiny are the best ones for ARC
Fedebec - the pi version isn’t fully functional either. Many of the skill plugins aren’t compatible with Linux. The difficult part of the pi version is the setup and maintenance effort. Lastly, the CPU on the pi is so slow that it greatly affects the user experience. The up board costs similar to a pi with comparable memory, maybe not the same but it’s similar priced - I also take in count that the up board is 10+ times faster than the pi for a similar price range. Albeit, costing a little more but what you get is superior by a huge factor in performance and experience.
@DJ What are your thoughts on android/ios tablets ? The specs are getting better. Do you have plans to improve the mobile apps to support more features ?
@DJ,
I haven’t posted in a quite a while, Dj I’m a little confused. Are you saying that Ezb v4 or iotiny is no longer needed with the new ARC software?
Thx
@ptp - no plan to progress the mobile version. I'm pushing to break into more advanced robot features. So many people are remote controlling robots with tablets and doing the same thing that we did 5-8 years ago. It's time to progress into more advanced robots with autonomous capabilities incorporating human assistance etc... I'm here to advance the industry
. The mobile version of the software is merely to support ez-robot products used by children in school.
@merne - last year in 2018 the software became compatible with arduino and many other controllers. Check the Products -> ARC page for a list of supported controllers. You will find information on this website (synthiam.com) homepage or other product pages for compatible products. Lots of info for you to read
Keep you busy for days