Asked
— Edited
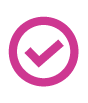
Anyone building a robot dog? I am looking for Servo's to build one that will work with ARC...
Related Hardware EZ-B v4
Related Control
Servo Speed
Nice, I did find someone also building a VESC controller over at Hackster...but I am not sure about how good this is for actually getting accurate positions! I mean we are in the robotics department and not up to be driving a remote controlled car, right?
But I guess @ptp will know...I am really bad with this kind of hardware evaluation stuff!!
Btw...I just finished the assembly video of my gearbox, and will put all the files up somewhere, just in case anyone wants to follow along!!
Uploaded all the files for printing, also included a parts list...
https://www.prusaprinters.org/prints/53681-cycloidal-drive-3d-printed-gearbox-401
First I'd like to say that I spent my life growing up in my grandfather's motor rewind shop, which was our family business (and also a commercial wiring company). So I spent a lot of time around motors. Some small enough to fit in my hand, to motors so big, I could walk inside the stator at 9 years old! (motors 1.5 meters in diameter! ) I would play with all the steel ball bearings and mess around with reels of copper wiring. So all this new tech of FOC motors and windings, magnets and phases is exciting as it takes me back to those old days.
I thought I'd add what I've learned researching these BLDC FOC motors and controllers.
Most of the BLDC FOC motors we are talking about, are built for drones. Their main purpose is to spin props at high speeds.
The controllers we've talked about here, are to convert these motors into low velocity and closed-loop positional motors so we can use them like servos.
These motors are rated in KV. KV refers to the constant velocity of a motor. It is measured by the number of revolutions per minute (rpm) that a motor turns when 1V (one volt) is applied with no load attached to that motor.
4) Torque is determined by the number of windings on the armature and the strength of the magnets. A low Kv motor has more windings of thinner wire. It will carry more volts at fewer amps, producing higher torque. A high Kv motor has fewer windings of thicker wire that carry more amps at fewer volts.
We will most likely be using these motors as actuators, so look at a lower KV value (100 KV or below). This will give more torque to move heavy objects/robot parts. If you go with a gearbox, you can pick a higher KV rating, which has a smaller physical size compared to the larger lower KV motors and can often deliver more torque. But you gain backlash and noise in the gearboxes.
Cogging. This is something to avoid and is due to fewer poles and magnets in a motor. The result is chunky moves at low speeds and the inability to makes small incremental degree movements. But, some developers are writing software for controllers to avoid cogging on these lower pole motors! A fascinating workaround.
Anyways hopefully this is helpful.
Used this ancient toothpuller to move my motor shaft...so now I will be able to mount the encoder on the other side of my BLDC!!
I will make a branch for this design, with the encoder to the back...and upload the files as soon as I am happy with them! There will also be a mount for the AS5047P-TS_EK_AB...
Tooth puller hahaha. That I know from my childhood is a bearing puller.
Everything is looking good. I look forward to seeing all axis work together. Is there much noise when they work together?
Actually everything is pretty good, considering the noise and the vibration... I will try and make a torque, speed and precision test asap!!
But today I was having to deal with a clogged nozzle, you know the drill!! Man am I happy, I did not lose some screws on the way...
Haahahha lots of fun....!!!