Asked
— Edited
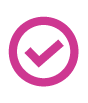
Anyone building a robot dog? I am looking for Servo's to build one that will work with ARC...
Related Hardware EZ-B v4
Related Control
Servo Speed
Hey @fxrtst have you played with those 60kg servo yet? I see a lot on eBay for really cheap but I haven’t purchased one yet. $30 versus $300 for a dynamixal seems like a good deal. I wonder if you can do a potentiometer hack on these as well?
These are my new favorite servos..I purchased directly from AliExpress....and I can say is they are incredibly strong, one of the quietest servos I've ever used (comp Dynamixel)...also great hardware available for them too. My drink droid has this servo at the elbow and can lift the entire load of the forearm and hand. Because, of their success I chose them for upgrading my Hexapod, Gar. I couldn't see why you couldn't do the hack..as long as the pot is accessible. Then you have a cheap $30 servo with feedback.
Just be aware...these are 1/5th scale servos...so they are not the same size as a standard servo...must bigger.
@Will, your such a tease. Can you give me a proper name or a link for these wonder servos? I've seen you use them on your videos but if you pointed to where to get them I can't find it. So much info, so little time. LOL. I don't have the patents to wait till your next fab Feb video.
Here's a picture of the $350 servo I'm using now. (It's no longer available)
aaaahhhh I remember those Seiko servos..I think I even still have one I purchased in the 90s....been around a long time. Those Seiko are still available...I think you have the PS-050, they have the super massive one for $550! the PS-105 I think that's the one I have.
http://www.hobbyclub.com/index.php?main_page=index&cPath=24_225
The servos from my hexapod and the drink droid: 60 Kg/cm servo from Ali Express I'm pretty sure this servo is not strong enough to lift the bubble section...maybe two working in tandem?
Great thanks @will. I’ll give them a shot. I see you purchased metal horns. Why on earth do they sell a 60kg servo with a plastic horn. My next project I was thinking about a robot dog. I refuse to (and can’t afford to) pay $70,000 for a Boston Dynamics (now Hyundai) Spot. Pretty sure you could build a pretty good dog with those servos and the T265 for ~1000
Yeah I think so too. I’m not sure of the speed of the servos.. for the lower leg and forward stepping you would want snappy fast speed to get that leaving the ground steps that Spot does. Buy three servos and experiment with a single leg set up. Btw you can run these at 8.4v giving you a bit more speed and torque.
i have a dog on the drawing board...you’ve never seen anything like this before. I am experimenting with the CANBUS 3 phase motors. They are pricey but even with these Motors and controllers ($400 per axis) your looking at about $5000 for the project.. well below $70,000 and even some of the smaller dogs that are about $30,000 from other manufactures.
Moved this convo out of the intel realsense thread into here
The Lynxmotion ST1 servo's are pretty snappy but they can't carry much of a load. Nice build though.