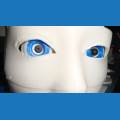
Aerius
Canada
Asked
— Edited
Inmoov Legs
Some extra filament rolls and servos....
Picture from the official InMoov site under activity members
Some extra filament rolls and servos....
Picture from the official InMoov site under activity members
There is no way in hell he will be able to walk, but my printer(s) is/are ready...
its awesome robot.whit a gyro and feetsensors he can walk. look at darwin-freddy-nao they all walk.
@nomad... Nao is less than 2ft tall... A full sized humanoid will need serious processing power, special joint motors and the backing of a well funded University in order to get it to walk... No offence dude, but you don't know enough about robotics and programming to understand how difficult it is to get a full sized human biped to walk... Just ask Honda....
Even just upright balancing would be a serious challenge...
If they give inMoov feet the size of snowshoes then maybe I might be able to get him to walk...
Yeah - that won't walk. It's legs are also very small compared to his body. Sort of dwarf-like. I hope someone makes a version that looks less like a hobbit android haha
this is a big robot.and small one.its all about money. now they can let any robot walk.
Nice! Great balance and movement. Full walking gait, left and right shift is smooth.
you say ,you need a well funded institute to make a robot walk.thats thru. but why do you want to make the legs for your inmoove iff you never , ever be able to let him walk,cause you say you be reddy to print them. and you also dont have the knowledge to do so.nobody has ever seen, the data or any to let a robot walk.we just see video's. if you see on FB there is a robot walking backwarts the stairs up.
well it looks like inmoov is steping up his game lol yea i agree those legs as well as his waist support don't exactly add up to his upper body structure, they need to be bigger in order to be able to adjust to the body aspect ratio and a gyro, acceleromator, and possibly a inverted pendulum, (no sure about the pendulum or not) distance sensors and pressure sensors in the feet to adjust to the distance and pressure of the ground underneath him. but at least the inmoov is making some really progress. bravo inmoov team.