Asked
— Edited
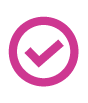
Hello,
PLEASE describe to me exactly how to control an AR-1202MG servo using an EZ-B v4 wifi controller.
AS of now, when I plug in the servo to D0 and use the vertical servo control, the servo does not move and an LED quickly blinks. I can feel the servo and I know it is receiving power. Sometimes the EZ-B resets itself and I have to reconnect.
https://www.bananarobotics.com/shop/PowerHD-AR-1202MG-Standard-Analog-High-Torque-Robot-Servo-60g
Please advise on what to do.
Sincerely,
Dave Lawrence [email protected]
David, After you added the vertical servo in ARC, did you set the Min. and Max settings? Do other servos work?
also D0 is horizontal servo
A few things to check.
What is the voltage of the battery your using in the EZ-B? Is it adequate to run the servo without giving it to much or not enough power? The specs say the servo runs on 4.8 to 6 volts.
Also does the servo move when you change its values in the vertical servo configuration screen (small gear icon)? The min and max values will be set to 90 as default, so changing minimum to under 90 and maximum over 90 by click and dragging your mouse over one of the numbers, you should hopefully get some movement.
Have you selected the correct port in the servo config screen to what your servo is connected to?
Is the servo lead connected to the EZ-B digit port the right way, i.e brown lead to black/ground pin, red lead to middle pin, yellow lead to white/signal pin?
And if all else fails, try another port and try it again.
Hope some of this helps and report back if you still have no luck.
the tutorial section has all the information you will need. Here is a direct link to the tutorial for moving a servo: https://synthiam.com/Tutorials/Lesson/49?courseId=4
When you load ARC, there is a window that explains how to press the ? (Question mark) next to the X (close) on every control. Pressing the ? (question mark) will load the help for that control. The help for that control is here: https://synthiam.com/Tutorials/Help.aspx?id=13
The help for that control lists a tutorial to move a servo.
Here is the window that shows what button to press for help on controls. Hope that helps in the future!
First off, the ez-b shouldn't reset itself. there's something wrong there with your power supply.
Second, make sure you have the servo plugged in the right way.(gnd closest to centre)
Third, make sure you set ex-builder to the right port and to proper min and max values.
If the led on your ezb is blinking your servo will never move no matter what settings you adjust... A blinking blue or green led means you are not connected to ARC.... As mentioned, you also need a good battery ... Lipo or niMh batteries, not alkaline.... Check out this tutorial Connecting to your EZB4
OK well so far I have been able to reduce the voltage going to the servo down to 6Vdc. Now the EZ-B does not reset constantly.
I am still not able to move the servo using either the vertical OR horizontal controls.
I believe what is happening is that this servo requires a different pulse width than the one supplied by D0 inherently. I am going to attempt to change the source code to modify the pulse width.
Dave
Do you have another servo to test.... Does it work with anything else you might have like a radio control or arduino?
Also are your servo controls set for 1 min and 180 max or are they still set at 90 min and 90 max?