In an earlier thread Doombot had mentioned he may put a ping sensor on his robotic claw to sense and pick up objects automatically... Well, I had a moment of inspiration so I thought I would try and knock up something... So check it out... a simple prototype of my version of object detecting robotic claw...
By Dunning-Kruger
— Last update
Other robots from Synthiam community
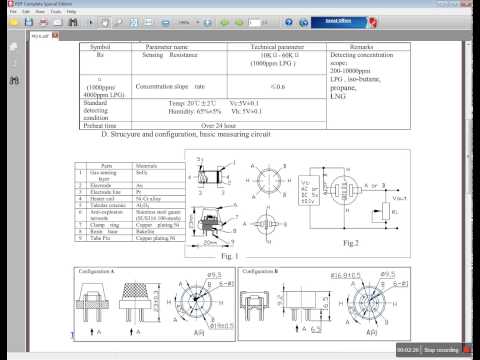
Luis's Using A Mq-? Sensor With The Ezb4 And ARC
Hello everyone.. Again I placed the demo into a video. Hope you enjoy. I will be happy to answer any questions you may...
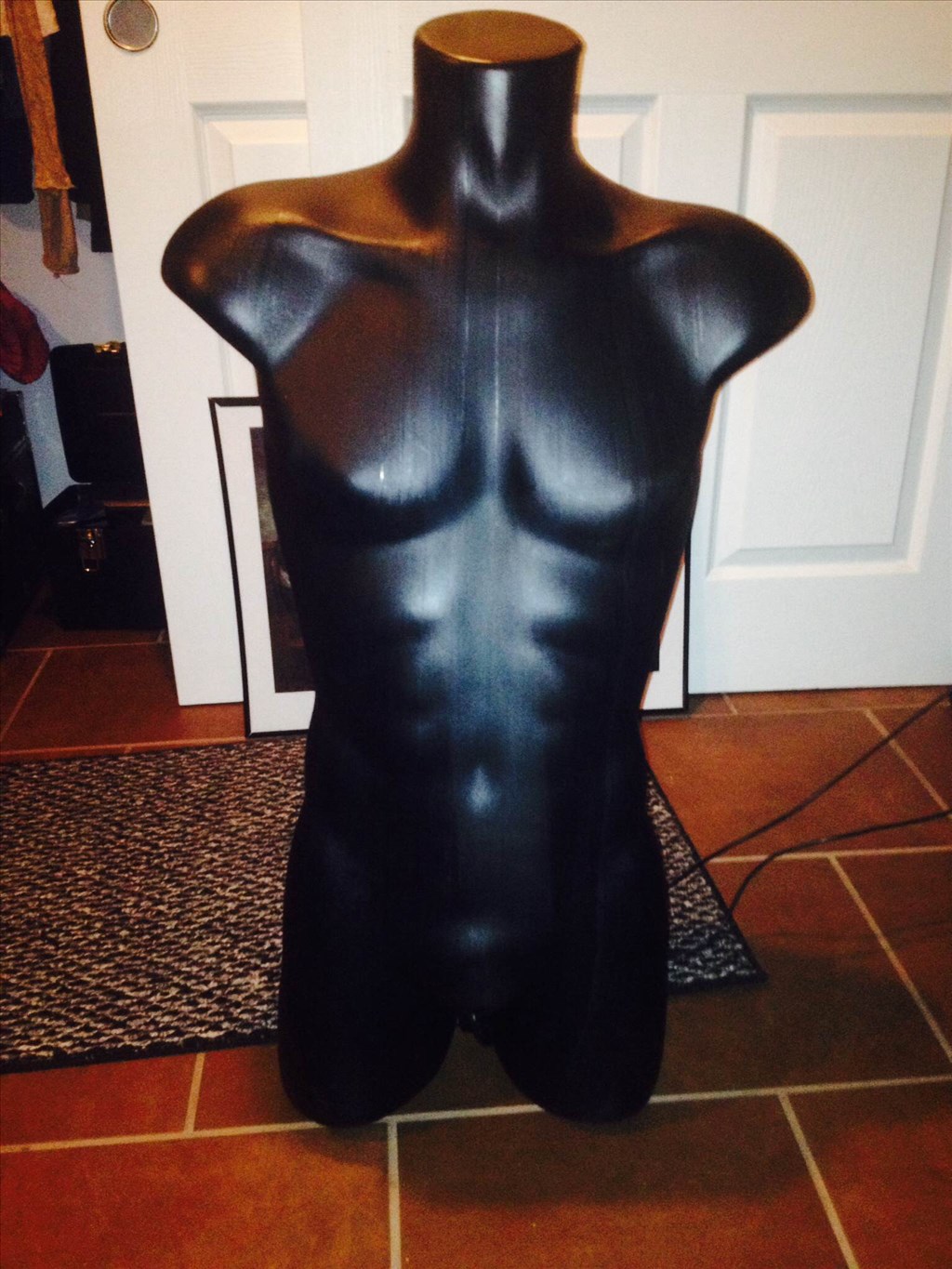
Kullthulu's J.A.R.V.I.S The Personal Assistant Bot.
So ive started constructing my Robot which ive named J.A.R.V.I.S I know there are several other bots that share this...
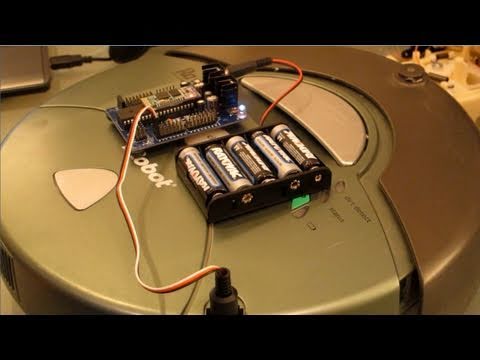
DJ's Irobot Roomba Hack
DJ modifies an iRobot Roomba to be wirelessly controlled with the EZ-B. He also adds a webcam and voice recognition!...
@Richard , Those Vex Turntables are cool and look like they may help a lot of builders easily make movable joints. They sat they are made for high load but I wonder just how high. What kind of servo are you using to move them? Looks like the servo needs some type of gear attached that sticks down into the turntable to mesh with the internal gears?
@Tony , Your amazing. You find all the cool toys.
These sensors only tell when an object is within it's gaze not how far away it is. How do you let the robot know when the object is actually within the hands grasp area?
I am using vex 393 motors (two per shoulder) and limit switches to prevent over rotation. The arm can lift 3lbs easily at 75% power (haven't tried heavier yet). I am using a sabertooth 2x5 motor controller to run the motors...I am now working in a elbow joint using a single motor and a jack screw assembly... Albeit slow, the elbow joint with a single vex269 motor can also easily curl a 3lbs weight... What geared dc motors lack in precision (compared to servos) they make up for in power.... Besides, with limit switches and coding I am doing a pretty good job of precision movements.... pics and more videos are coming...
Thanks for your comments Richard
@Dave, these object detection sensors flag the main controller when an object comes into range of its view. with the GP2Y0D810 the range is 100mm (4 inch) and with the GP2Y0D805 the range is 50mm (2 inch). There output is normally high and driven low when an object comes into range, so you just need to connect it to one of the EZ-B port lines. I use the 100mm type which senses outside of the fingers (they have to be slightly open) so a signal on this port line shows that something has been placed in front of the hand.
@Anthony, For my EZ robots I use QTC (Quantum Tunnelling Composite) pills for touch/pressure sensing.
www.rapidonline.com/Education/QTC-Pills-each-06-1298?sourceRefKey=EmIZWpHyh
Its a pretty amazing material, the finger sensor can sense the slightest touch/pressure to full compression (power grip). I make the sensor by sandwiching the pill between two thin conductor plates with soldered micro connect wires then I heat shrink the whole thing. They are then installed under rubber finger pads with the micro connect wires going down the hollow fingers, they then need to be connected to the an EZ-B analogue port via a potential divider (resistors).
More details here on QTC robot applications
www.peratech.com/mit.html
Tony
I was going to try this... Simple analog force sensor
Connect to an ADC port via a potential divider (look at my LiPo monitor circuit for details for a divider). When the pressure increases, which causes the resistance to increase/decrease (depending on how the part works) the voltage on the signal of the ADC port will change due to the divider circuit. This can then be read in a script with GetADC() and the value used to determine the pressure.
The pressure value can then be used to enable/disable ports, run controls or other scripts, pretty much anything.
If you search the forum for someone asking about using an LDR the method I eventually explained is very similar but rather than light altering the value pressure does.
Pics of the Vex turntable for the shoulder joint... and my bots jack screw elbow joint...
Richard R, Thanks for sharing your very interesting build. I enjoy your straight forward approach and comments! Steve S