Hey Guys,
I've read lots on the forum, and posted a hand full of times, but I thought it was about time I launched my first major project (well, my second really, I converted a wall-e, but I thought there was enough of those on here).
So here is announcing OmniMC, an Omnibot 2000 media centre
The idea is to make him all RC and to also house a Raspberry PI running RaspBMC as the media centre bit. I'll then add some speakers and maybe some under-bot lighting
I'm wondering if then I can control the whole thing with one of these:
Other than that, I'm kinda just winging it and seeing what other bits and pieces I come up with.
To start with though, I've done the usual thing of gutting him and sticking him through the dishwasher
So right now, he is prepped and ready to go.
I've already got my EZ-Robot kit, and a few components such as 6v battery
Some blue replacement bulbs
My Raspberry PI (which arrived today) and I've just won a screen for his chest
While I'm waiting for some other bits, I've also been looking at making some replacement tires which you can see details of in one of my other posts
So that's pretty much the state of play at the moment. I'm pretty much a novice at all this, so I'm looking forward to the challenge. Lets see if I've bitten off more than I can chew
Other robots from Synthiam community
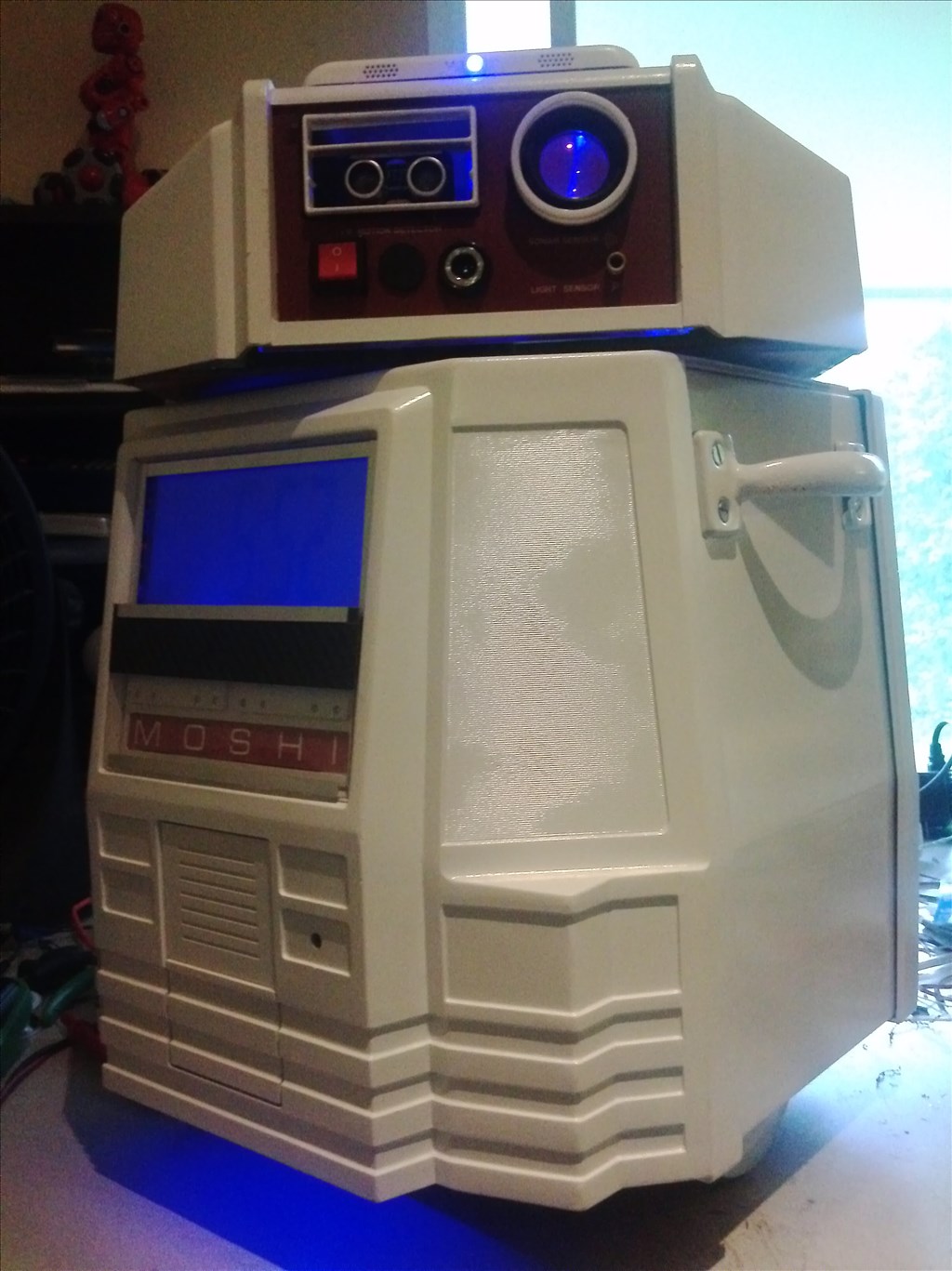
Rb550f's Moshi Is Alive
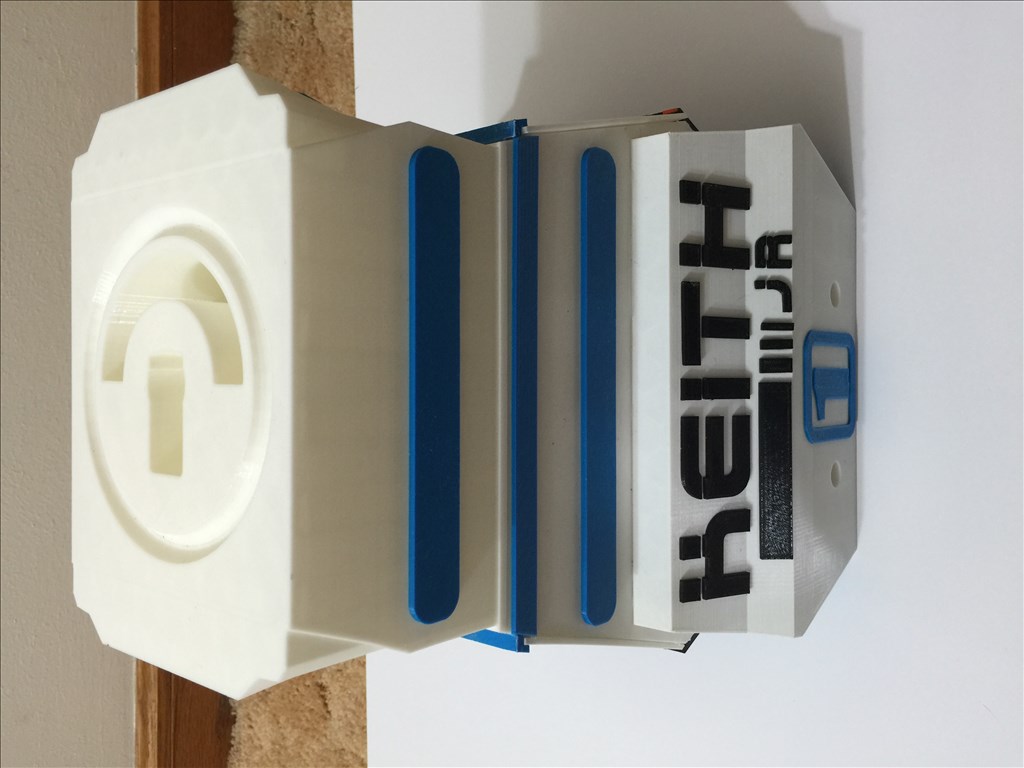
69Developer's Anyone Interested In Seeing Some Pictures And...
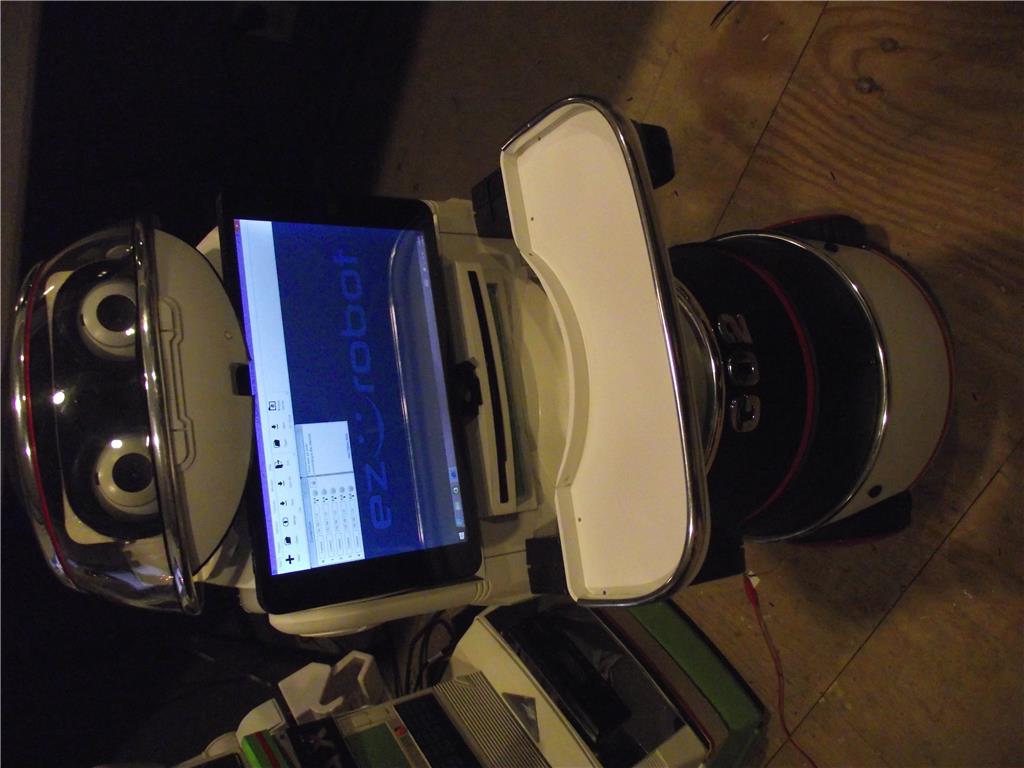
Hi Matt, do you happen to need the remote control or circuit board? Regards, Mike
Matt, it looks like you have things under control.
Hey Mike,
Unfortunately it didn't come with a remote (it came with a fascia for a remote, but not a actual complete remote).
I don't need any of the internals if you need anything from there? though there was a scorch mark on the top of the plastic between the main circuit and the tape deck, so am thinking that it might have burnt out (was under where a big chip sits). The only bit I have that I think might be re-usable/saleable would be the tape deck and probably the LCD + panel, though again, because it wasn't in working condition when I got it, I can't guarantee anything.
Whoop! The screen for his chest just arrived and it looks like it will fit perfectly
Unfortunately I'm out tonight, so will have to wait till tomorrow till I get to play with it.
The screen itself has a weird connector on the bottom, but came with a wire harness that has the more standard RCA connectors, so I'll look to just gut the whole thing down and solder it on permanently. I should then be able to just hook it up to the raspberry pi, which is configured and ready to go
Once I have it working, the next step is figuring out how to mount it. I could just stick it on the front, but would be cool if I could make a cut out for it. I'm not sure how confident at doing that I am though. Anybody any tips?
Matt
Ok, well, as I knew I couldn't play with it this evening, I thought I'd spend my lunch time giving it a quick test
Looks like I might have to create a custom skin for the UI as the fonts are really hard to read, but will look at that last (Not sure how much I should post about that here seeing as that is raspberry pi based, so will keep it to a minimum unless people ask).
Hi Matt, Great looking monitor! Regards, Mike
Thanks Mike.
So with a little bit of soldering this morning, I managed to get the wiring down to this:
A lot cleaner
I kept the audio RCA jacks just incase I ever decide to connect them up, but have just wrapped them up and cable tied them for now.
Ok, so last night I went ahead and cut the hole for the monitor
I may have cut the sides a little too deep though
I'm thinking though, maybe put masking tape around the monitor edge and fill in the gap with some body filler. Does that sound like a good idea? I've not really done that before though, so any tips / suggestions?
The next thing to work out is how to fix the screen into place
Because of the cable coming out of the bottom (though I could move it) it currently needs to be mounted from the rear. I would like to try and keep it so that the screen could be removed should I need to, so I'm not too sure on a good way to mount it. Anybody got any suggestions?