Let me introduce you my Inmoov version ,
(my 4 year grand daughter called it : ROBOTO)
The work is not yet complete , but I think promising.
I intend to take a break during the summer and will get back to my project later.
Surely if it rains outside I will probably start writing scripts
(it is so easy to get addicted to this kind of project)
By Aerius
— Last update
Other robots from Synthiam community
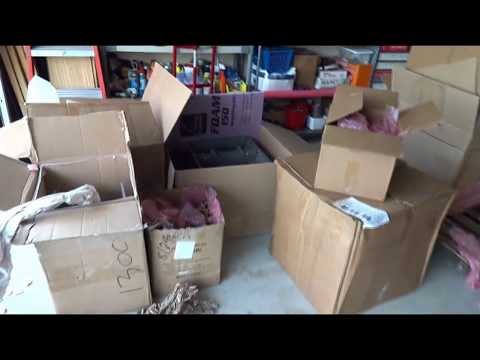
Dave's Resurrection - Another Full Sized Lost In Space B9...
There is no control yet in this robot. However with the upgrades Im planning for this robot, Synthiam arc and the EZB...
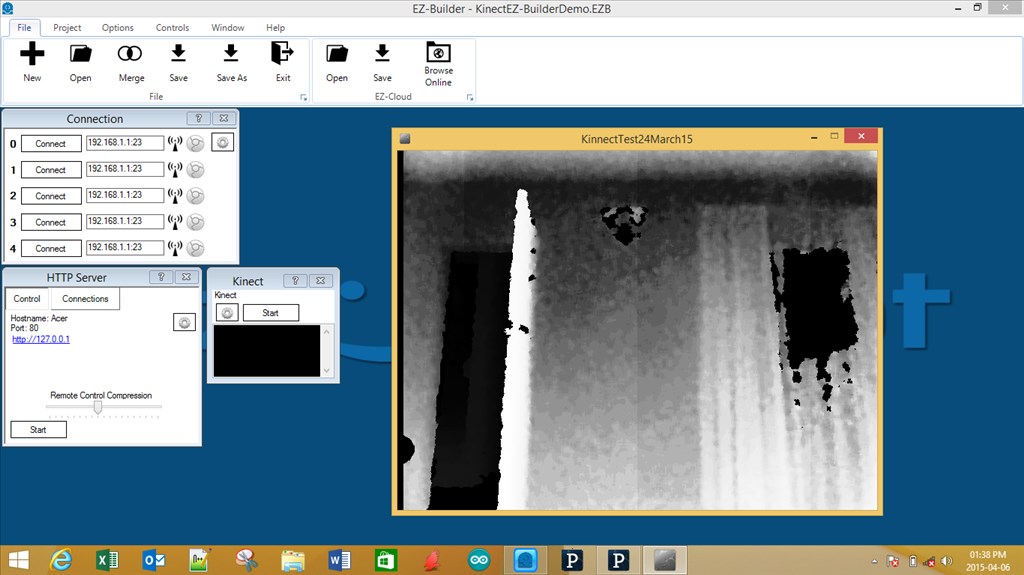
Ianmbrick's Project To Link A Microsoft Kinect Xbox 360...
Overview ------------- In this post I present a project that I set up to link a Microsoft Kinect Xbox 360 sensor with...
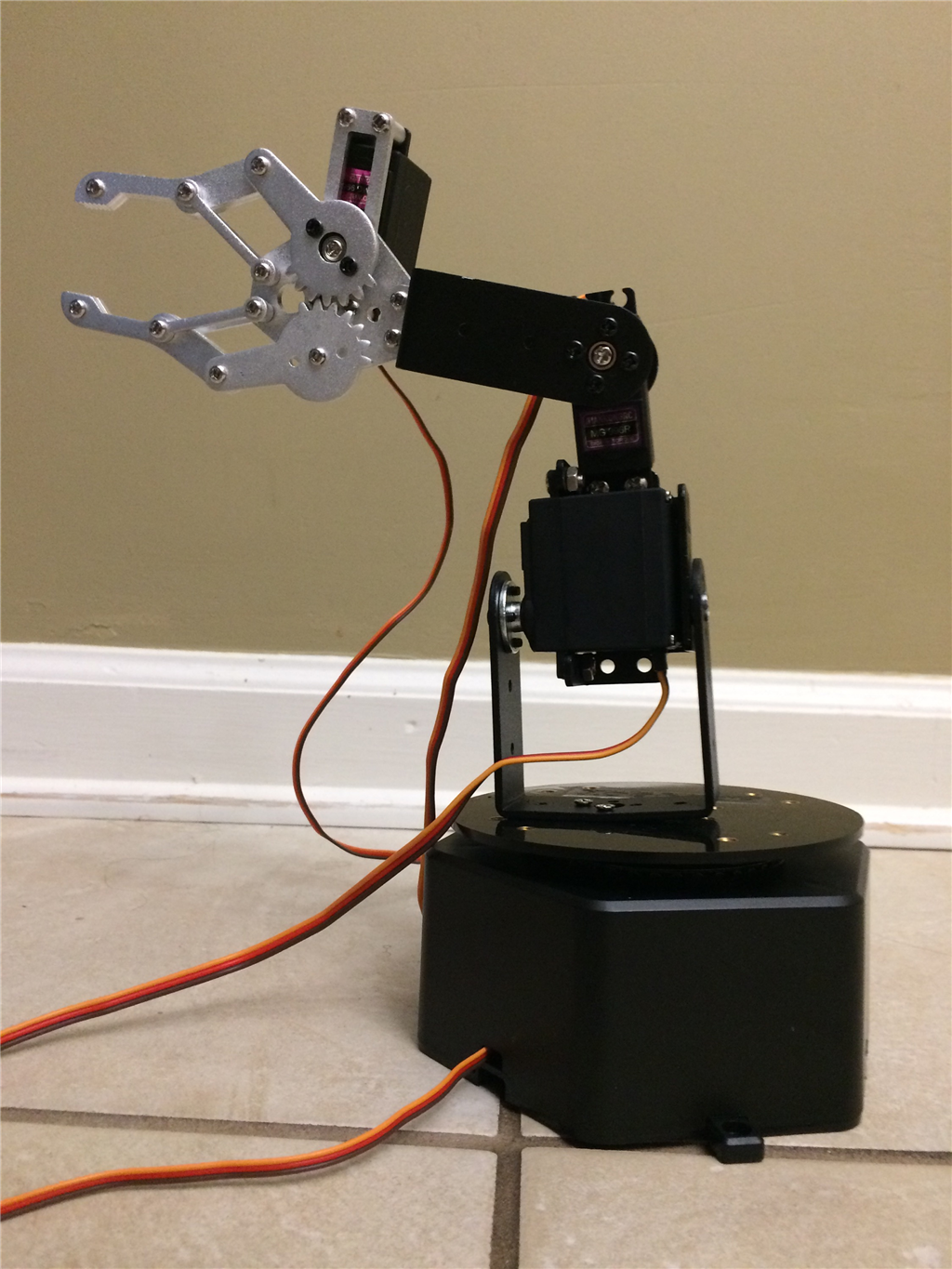
Ezang's My New Robot Arm On ARC
My new robot arm on Ez- builder - video next week coming - he has a gripping personality
I love the look of him. I am about to start one myself. I have a few shelves worth of parts just waiting. Thanks for the photos!
I'll be glad to help If you have any question when you do the assembly
I am sure that I will come across something and just say "WHAT?" Thanks for the offer!
@Aerius. WOW! That looks fantastic. I like the colors. A two color printer really helps to add the accents. What printer do you have?
That is fantastic! I really dig the colors as well - man, all of you are getting me jealous.
Might have to create our own InMoov here at ez-robot
@ bhouston tanks! I am using a Flashforge Dreamer. When printing i can interrupt the job, unload the filament, load an other color and resume printing. That's the way i did print the stomach circle and the ears.
Guys your good words make me proud and help me to go foward. Tanks
@ dj what my Inmoov is holding in is hand will make the real difference.
@Aerius Great work.... your parts fit nicely.... very clean build indeed ....