Hi Friends!. well I'm finally ready to put my full size R2 to roll... But I need a tip from you. What kind of H-Bridge or controller do I need (or can I use) to use with my ez-b ? I believe that the regular one will not be able to power this Scooter motors that i'm using.. am I wrong ?!
By tevans
— Last update
Other robots from Synthiam community
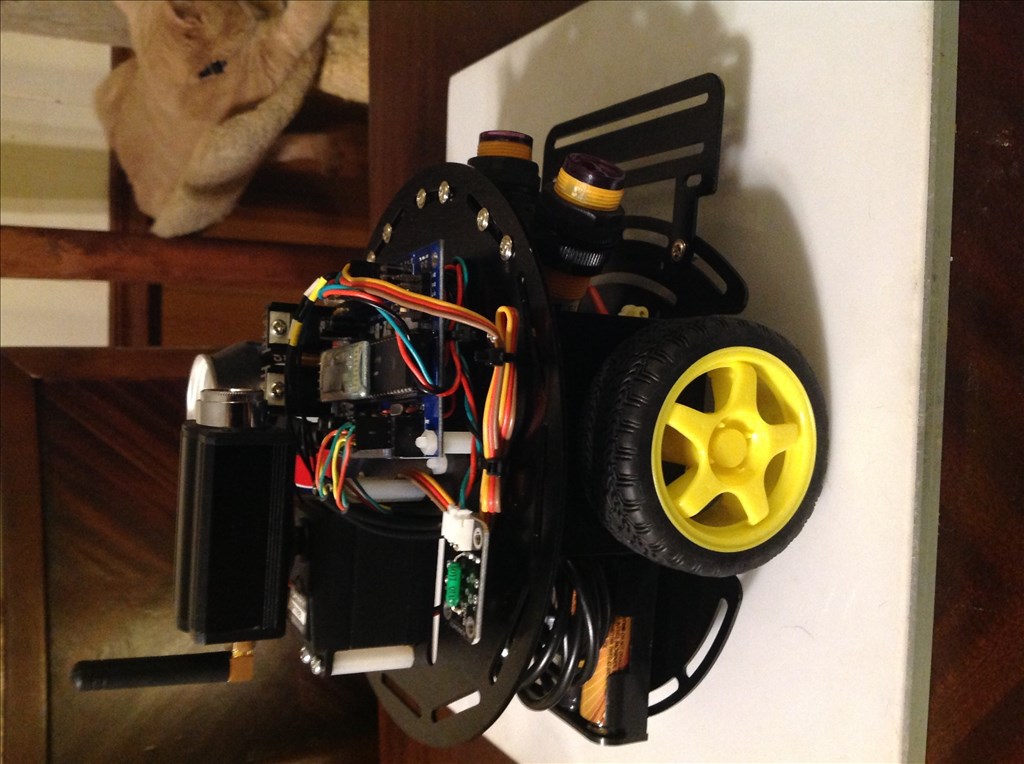
Grimjack73's The Presentation Piece
After the recent close if the Ez store, I needed to find a platform to present the EZ-kit with. A quick look through the...
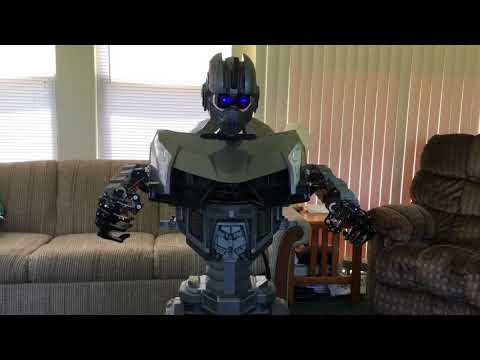
Steve's Artamus, The Rambo Knight Robot Hack
Artamus, the Rambo Knight Autobot Robot Hack #1 Soft Hack Includes a Hack of the RC Controller only. Requires no...
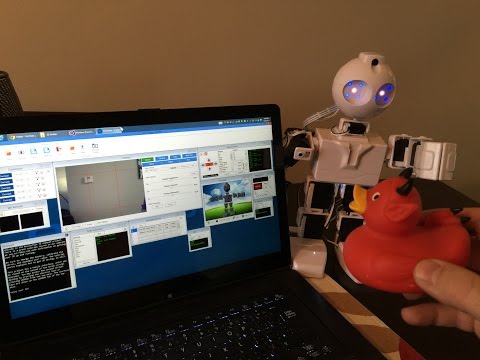
DJ's Jd Wants His Rubber Duck
Should I give it to him? lol
Sabertooth 2x12 is probably a good option. Without knowing the specs on the motors it is impossible to know though.
If you go the sabertooth route, and if your motors have encoders, I would also add a kangaroo.
I second what David said... A sabretooth is even easier to use than a cheap H bridge....
Thanks guys! Hey.. By the way, I'll be traveling to California for the next days (finally got my 12 days vacation ! ) Do you know some good store where I can buy robotic supplies ? Since is kink of hard to find it in Brazil, I'll use some time in my tripe to dig some stuff.... I'll be in LA and San Francisco ( and in the road between..) lol Thank for any hint!
@tevans i went with the sabertooth 2x25 for my R2 it is hybrid wood and aluminium and other scraps so its not very light... from the looks i have the same motors you have and the sabertooth does fine at 12v
Thanks @jayutmb! It seems the sabertooth is the choice of you expert guys! So I'll look for that to buy.. ??
Hi friends! I took your advice and installed a saber tooth. It's great! It's working fine. Now... I installed anothe h-bridge do run the 12v motor that drives the dome. My question for you my genius friends is: how do I set position on this motor... Since it is not a servo... .? I'll post a phot of the sistem so you can have an idea..
You can use a potentiometer connected to one of the ezb's analog ports... A 5 or 10k pot should work fine... Connect it to the center of the dome (so that it rotates with the dome) and it should read the dome's position no problem....