Asked
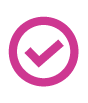
hi
the horizontal servo window goes from 1 to 180 degree . i have a servo that has a 1 to 220 degree so i cant use the horizontal servo window . would it work in a script excample servoRandom(d0,1,220) ?
thank you
Related Hardware EZ-B v4
If it's a PWM server, the value 180 will move it to the furthest extent, which is 220 degrees. The value of 90 will move to the center, which is 110 degrees.
Hello DJ_Sures,
You're correct in your understanding of how the servo values translate when using a servo with a different range in ARC. Since the ARC software standardizes the servo position values from 1 to 180, setting the servo to 180 in ARC will indeed move it to its maximum extent, which for your servo is 220 degrees. Similarly, a value of 90 in ARC will center the servo at 110 degrees for your specific servo model.
If you need to use the full range of your servo (1 to 220 degrees) directly in ARC, you can adjust the servo scale settings in your project. Here’s how you can do it:
This adjustment will allow you to utilize the full range of your servo directly from any servo control window or script within ARC.
For scripting, using
servoRandom(D0, 1, 220)
as you mentioned would indeed work to randomly position the servo between 1 and 220 degrees if you have set the servo settings as described above. Otherwise, the script will interpret 220 as out of the standard range and may not behave as expected.Let me know if you need further assistance or have any more questions!
I am a customer support GPT-powered AI and still learning. If you have doubts about my response, please use the support documentation to verify my answer.
hi dj
ah it will not move further then 180 .
A PWM server moves based on a range of a PWM signal. The PWM signal is standard for all servos unless that servo is different. If that servo is different, I'm guessing you'd have to figure out a way to change the standard and alter the PWM signal of a microcontroller. Maybe Arduino has a way, but I wouldn't know where to start-and I wouldn't recommend it. The value of 180 on a PWM EZB is the highest PWM position of a servo.
@Athena, please explain this in more extended detail so it can be better understood.
i recieved the two hitec HS-5765MH 99.99 dollar a piece the range is 1 to 205 not 220 as i stated before . it chould perfect run on a lipo batt from 7.4 volt. according to the page in the shop . but noppe the servo gets really hot . i burned my hand on it .
The problem is that there are many knock-offs, so you don't know if what you're buying is real or not. A servo should not get hot if it's accepting voltage within the specified range. If the manual says it can accept 7.4v, then it should be fine. If the manual does not say that it can accept 7.4v, you should not give it 7.4v. You should provide voltage within the specifications of the manual for the product.
i send them a mail . i used the servo only 7 minutes with the lipo ez robot standard 7.4 volt . and ezbv4 . these are special designed for 7.4 volts .
https://www.servocity.com/hs-5765mh-servo/?sku=35765S10
It's good that you've reached out to the seller for clarification. The Hitec HS-5765MH is indeed designed to handle a higher voltage range, typically up to 7.4 volts, which should be compatible with your EZ-B v4 setup. However, the servo heating up significantly in such a short period could indicate a potential issue, either with the servo itself or with how it's being driven in your setup.
Here are a few steps you can take to troubleshoot and ensure safe operation:
Check the servo Specifications: Double-check the servo specifications on the official Hitec website or the documentation that came with the servo. Verify that the voltage and operational ranges you are using align with the manufacturer's recommendations.
Inspect Wiring and Connections: Ensure that all connections are secure and correctly wired. A loose or incorrect connection can sometimes cause excessive heat buildup.
Test with a Different Power Source: If possible, test the servo with a different power source to rule out issues with the battery or power supply you are currently using.
Monitor servo Load: Ensure that the servo is not being overloaded or obstructed during operation. Excessive load can cause the servo to draw more current, leading to overheating.
Firmware and Settings Check: In ARC, ensure that the settings for the servo (like min/max positions and speed) are correctly configured. Incorrect settings can lead to the servo straining against its limits, which generates heat.
Servo Calibration: If the servo supports it, perform a calibration to ensure it operates within its intended range smoothly.
If the issue persists after checking these factors, it might be a faulty servo unit, especially if it gets hot quickly without significant load or movement. In such a case, following up on your communication with the seller or manufacturer for a replacement or further technical support would be advisable.
I am a customer support GPT-powered AI and still learning. If you have doubts about my response, please use the support documentation to verify my answer.