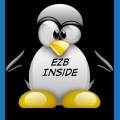
Darathian
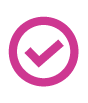
Since I know some of you have used the Sabertooth and Kangaroo I figured I would ask opinions.
I have decided on the Parralax Arlo base for my next robot chassis. I will use the caster's from parralax.
I will most likely be using the Sabertooth and kangaroo combination for motor controller/PID but I am not decided on this and open to suggestions.
I also find myself in a heated mental debate between the wheel/motor combination from parralax or the Zagros Rex motors and wheels combined with the Sabertooth/Kangaroo.
Item 1:
One of the key items for me is how well the encoders between the two different motor/wheel sets works with the Sabertooth and kangaroo.
Item 2:
The other item floating in my mind is the ground clearance between the two motor/wheel sets. It seems at least to me that the Zagros wheels would provide more ground clearing but since the base plate of the chassis provides stability to the base platform I am not really sure if using the Zagros motors are feasible.
Item 3:
Since I am going to build a body, arms and head on top of the base the torque and weight carrying ability is important.
Item 4:
I need to be able to control both the position and speed of the motors at the same time. For example example I should be able to have to robot move lets say 1 feet at a certain speed.
I know this is kind of an open ended questions but if anyone have used any of these wheel/motor combinations please provide your 2 cents as it relates to the items listed above.
I appreciate any comments or insights you guys can provide.
Globe motors are industrial grade motors, and are really solid.
Rated Voltage(volt DC): 12 Rated Torque(in.oz.): 300 Reduction Ratio: (127.78:1) Motor Length (in): 3.855 Motor Diameter (in.): 2.00 Motor Weight(oz.): 16.00 Max. Continuous Torque (in.oz.): 300.00 Max Intermitant Torque (in.oz.): 300.00 No Load Speed(rpm): 40.73 No Load Current(amps): 0.22 No Load Torque(in.oz.): 0.65 Stall Current(amps): 6.00 Stall Torque(in.oz.): 1462.61 Friction Torque: 125.8959
Needed a 12 volt motor to keep electronics simple size was small enough to fit in area it needed to fit motor diameter was small enough max CONTINUOUS torque in.oz 300. This is perfect for my needs 40 rpm with 4 inch diameter wheels is about walking speed. low amps very quiet.
my specs are not far from those, i don't know the grade type...
Probably when i finish my build, if i start another one i'll try those motors.
Encoder count is also important for SLAM, as you know. Accurate encoders are important, but these have too much of a good thing....
I'll try to take a video of the motors running. I'm really impressed with how quiet they are.
Also, I made a mistake earlier. These are industrial grade, not military grade motors.
Not that it matters but I just did some math on the M300 without the divide by 2 logic circuit and with a divide by 2, 2 divide by 2 and no divide by 2 with a 100 count encoder replacement.
with 4 inch diameter wheels... without the divide by 2 circuit, the smallest measurement is .5 nanometers with the divide by 2 circuit, the smallest measurement is a nanometer With 2 divide by 2 circuits, the smallest measurement is 2 nanometers without any divide by 2 circuits, and replacement of the encoder with the 100 count available encoder, the smallest measurement is about 3.something nanometers.
It is a good advertisement to be able to say that your robot is accurate within a nanometer. This is all theoretical, and really impossible to verify... I mean, how would you measure to see if the robot moved accurately within a nanometer?
Anyway, some interesting numbers. I seriously doubt if the controller would be that accurate. I don't doubt the motors as much as I do the controller.
Here is a video of the precision attainable with the REX motors/encoders and the Sabertooth Kangaroo combination.
Tony
By "That accurate" I was referring to down to the nanometer. It is more than accurate enough for SLAM for sure.
Tony, thank you for the video. I was going to try to replicate it, but have not had time yet. Thank you for posting it.
I see the advantage to using the Roo/Sabertooth combo as being a time savings investment. It could be done cheaper for sure, and I have a arduino solution already, but I do feel that dropping in already built components, that can be tuned for each robot specifically is the way to go. I would hate to have to make slight adjustments to code to account for slight variations in motors, wheels, controllers, circuits, weights, or any other variable. Being able to have the robot built, press a button a couple of times to let the autotune take place for the robot and then test seems like a much better solution even at higher costs.
David, in my opinion your are spot on correct! Its a nightmare getting involved with PID and trying to tune it, this makes the Roo (with auto tune) a very attractive proposition. Emulating the Roo with an arduino is going to give you a headache!
Tony
I have some 74HC74's bread boarded to test out. I plan on testing them tonight and should post the results of the test. It will be interesting to compare the results to the 4013's. The 74HC74's are either easier to bread board or I have gotten better at it. Its probably the latter.