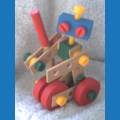
dodi
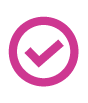
The servos looked almost good, so I skipped the hardware calibration for now. Both arms show a bit to the right, fixed by fine tuning to max. 12 units. Q: what's a unit?
When turned on, the servos move to strange positions. The head is fully thrown back, one arm almost straight, the other one down. This position seems to be reproducable, so I'd guess it's stored somewhere. Q: how to influence the servo turn-on positions?
The "Dance" script seems not to honor fine tuning? The arms seem to have an right offset (like uncalibrated), and the left arm strikes the head while moving. The "Stop" script moves the arms into the expected (straight) position. What am I missing?
Finally, after Stop, the servos tend to produce noise (humming), which sometimes can be reduced or eliminated for a while, by manually lifting the claws a bit. But after some time the noise starts again, well amplified by resonance of the entire body :-( I suspect that this behaviour will stress the battery, and it also stresses my ears. Are the shoulder servos too weak for supporting the weight of the entire arms?
Apropos noise: the Dance music is very nice, but a bit too loud for me. I'm missing a volume control with the soundboard. Even if I know (now) that SetVolume can be used to influence the sound volume, I'm missing according instructions/settings with the project/controls.
@dodi...
All hobby servos when power is first applied to them will jump to a random position until a controller sends a first position command....
The shoulder servos produce over 200oz in of torque so they are for sure not too weak..Most servos will hum to one degree or another... it's normal unless they are binding on something causing seriously excessive noise and/or smoke is pouring out of them...
You won't stress the battery... only thing it may do is drain it faster... The stress is in the servos if they are stuck or as mentioned binding on something... Make sure all the cables are loose so that the servos are not pulling on them...
As Richard said...
You are unable to change or specify the positions of servos when you power them up. Follow the tutorial for the robot, these explain this and the correct procedure for powering up.
If the dance script causes parts to collide then your calibration or fine tuning needs looking at. Calibrate properly as per the tutorial then fine tune. 12 "units" is too much for a fine tune! FYI - units are positions, generally 1 position is around 1 degree but it's not an exact thing and will vary from servo to servo.
Noise from servos holding a position is normal, it shows they are working. There is nothing wrong with this.
The soundboard should have a volume control as part of it. If it doesn't, reinstall the latest version of ARC.
Begin by following the required tutorials within the learn section. Most of your questions are answered within them.
dodi
here is the volume
AFAIK servos are steered by PWM, so that it's unclear that they do without a signal. But when most of my servos start up near the 90° position, the neck servo is far away from that. Do you think that a replacement should behave better?
The noise indicates to me that they cannot keep the position, instead they keep the arms swinging around the set position. As I mentioned, that noise is so loud that I have to turn off the robot whenever possible.
After another look at the cables I suspect that the cable outlet is too long and too stiff, applying force to the brackets. All my servos deviate from the straight (90°) position as pressed by the cables. May it help to cut off part of the stress relieve, and glue the cables to the servo, so that they keep away from the brackets?
Sorry for my poor English, I meant draining the battery. As beforementioned, the cables do not affect servo movement, except immediately at the place where they come out of the servos.
Thanks, the slider color is so light that I didn't notice the control at all :-(
A replacement will not make a difference as you servos are acting normally. While they are controlled by PWM on initial powering up they will jump to a random position. There is nothing that can be done to avoid this. This is normal behaviour.
The noise indicates that they are working. Keeping position or not should be the only indication of if they cannot hold position. The more stress the harder they work and the more noise they will make. This is normal and nothing to be concerned about.If a servo is being used it will drain the battery. There is nothing you can do to avoid this.
Everything you have posted is normal behaviour and you have no issues. All have been explained many times in this forum and also all over the internet for most of your "issues".
dodi
picture is says more then words.keep asking if you have questions. i am newbie too.
About noise and oscillations: After many experiments I found out that the servos are not incapable of holding a position, instead in detail the shoulder servos are incapable of reaching certain positions. When a position cannot be reached, the arms can oscillate up-down with an claw amplitude of several mm (the mechanical clearance). By slightly pressing an arm upwards, the shoulder servo can lock into up to 3 discrete positions, before it reaches a stable position. Similar behaviour can be observed in the Fine Tune window, where most servos react only on changes by 2 units.
Thus the noise and oscillation seems not to be a matter of force, but a matter of the closed-loop control inside the servo, with different granularity and phase between the position sensor and the actor. Temparature also may influence the control, making noise (oscillations) appear and disappear over time.
The cable outlets (strain relief) force the cables against the brackets, what may be good or bad. That applied force and friction may e.g. reduce the chance for oscillations. Otherwise the friction could be eliminated by an change of the cable outlet orientation and fixing the cable to the servo in a direction, that does not require two 90° bendings of the cable.