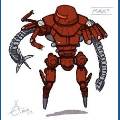
rgordon
USA
Asked
— Edited
This looks handy. Not only for InMoovs but for other bot builders as well.
Any InMoov builders using this?
This looks handy. Not only for InMoovs but for other bot builders as well.
Any InMoov builders using this?
I'm using an hdmi cable and hdmi breakout board instead of this. I run power to my servos on a separate feed.
I would highly recommend not using a ribbon cable for the servos. That is very dangerous and will most likely melt the coating and hopefully burn the very small wires before lighting on fire.
The Extension Cable that we offer is best for this application because, as Richard R said when he saw them "those aren't cheap China extension cables" - he's correct, we chose very high quality cables.
Good catch! My bad....wasn't thinking....as usual....:D Nuff said....
@d.cochran...
What is the wire gauge in the hdmi cable?
You can't use very large gauge and get it through the joints in the inmoov. I am limiting the hdmi cables to 3 feet because of this. Also, and I can't stress this enough, I am running the power through 14 gauge wire to the location of the 6 hand/wrist servos. This isn't going through the ezb but uses a common ground to the ezb. Each ezb in my build has no more than 9 servos attached to it with only 4 of them getting power directly from the ezb. These 3 of these 4 don't have extensions as they are close to the placement of the ezb. Only one servo has an actual extension which is the one in the elbow.
I should also say that the ezb could probably handle the load of the 9 servos without an issue. I just am trying to keep from having a lot of wires passing through the joints.
My InMoov is running all of it's servo (except fingers) through the ez-b. It can do it, but if you want more efficiency, I would recommend running separate power such as d.cochran is doing.
Also, the hdmi cable is not good for power - obviously, but it's great for signal
That's what d.cochran is doing as well. He's running only the signal through the hdmi cable and the power is separate.
@d.cochran... Thx for the info
It's true, I have "those" cheap Chinese servo extension cables off of eBay.... They are barely good enough for sensors let alone servos... I saw the ones Jeremie was using and they are solid... My next order with ez robot I plan on buying a couple of 10 packs of them....
@David, I really should be adopting your method of a central power hub for the servos... However, saying that, I did have all the large servos (12 in all) plugged in directly to my ezb's ports.... It handled it like a champ....
I was using an ssc-32 for the hand and wrist servos.... maybe not the best or most elegant way, but it did take the load of the ezb... However, now that ARC supports the ssc-32 everything can be added to the auto positioner control... It makes the ssc-32 much more usable...