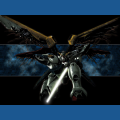
budel0
I have made this thread because I use them (for about 4 months now in my robot) and I have noticed lots of people struggling with h-bridges. So I hope you all can use it and understand what I'm trying to tell. (THEY ARE EASIER!!)
What is an Rc ESC? An Rc esc is a motorcontroller used in about every electric Rc Car/plane/boot and every other Rc vehicle in the rc world that is more advanced than your standard $5,- toy. ESC stands for Electronic Speed Controller, it uses the same plug as your standard servo. And will work with the EZ-b.
ESC types: There are 2 types of ESCs, this is because there are 2 types of electric motors. You have brushed and brushless motors. The differance is that brushless motors last longer and provide greater speed. Brushless motors also have 3 wires to control it, this means that there is a special type of ESC for it. A brushless motor has 3 wires because it has 3 coils inside. They are also known as a three-phase inductionmotor (they are brushless because they generate a rotating magnetic field which makes the anker, the thingy that is attached to the axle of your motor rotate).
How they work: ESC's for brushed motors puls of the maximum voltage to the motor, the faster the pulses the faster it will rotate. ESC's for brushless motors work in a simular way but they let the brushless motor create a rotating magnetic field by powering 3 coils, The faster the field is rotating, the faster the axle will rotate.
Brushed:
Brushless:
NOTE: there is a third type of esc but this one exists within brushed and brushless ESCs. These ESCs are different because they make the motor rotatie only one way, these are mainly used for rc airplanes and helicopters (where only one way of rotation is required).
How to wire it: Every esc has wires specified for the motor and the battery. So with brushed motors you will have 4 wires, 2 for an electric motor and 2 for the battery, a servo plug and an on/off switch. With brushless motors you will have 5 wires, 2 for battery and 3 for the motor and ofcourse a on/off switch and a servo plug.
So... Connect the red wire to the + pole of the motor and the same for the black wire. Same for the battery. There is almost noway to do this wrong! As usually one side of the ESC is for the battery and one side is for the motor and if not it will be written on it. Yes it's soooo easy! Note: never mix up the battery with the motor, you might fry the esc. Next up is connecting it to the EZ-b. And tadaaaa you have everything connected.
How to use it in ARC: As an electric motor can rotate two ways (back and forth), the neutral stance will be the middle of a vertical/horizontal servo control in the ARC. And that is 35, since the v13 update. To make the motor rotate move the bar up or down. Note: it will not work automaticly with the modified servo panel. It does work with Movement Panel but then you will need scripts.
As we now have achieved to make it rotate you can also use it with the movement panel, for everyway of motion I have created scripts to slowly start it up and slow it down. As it will jump directly to the speed you have set. There are 5 scripts required for each direction if you want to use the modified servo panel.
Script (when using 2 esc): servo(d0, 35) servo(d1, 35) sleep(50) servo(d0, 39) servo(d1, 39) sleep(50) servo(d0, 42) servo(d1, 42)
If you notice that one of your set of wheels is rotating the otherway around, then deduct the amount that you are adding to the 35 of the 35 ( 40-35 = 5 --> 35-5= 30)
Pros:
- Masive speed, up to 160mph (fastest Rc boat, I've seen, maybe even faster).
- Automatic lipo cut-off, this protects you lipo batteries from getting drained to far.
- Brushless motors
- Low prices.
- For every motor there exist an ESC.
- Most ESC's have an automatic BEC, BEC stands for Battery Eliminator Circuit, in the RC world the BEC is used to power the receiver(they usually give of 5v at 1 or 2 amps). In my experience with the EZ-b I have noticed that the batteries powering the EZ-b have lasted longer when I have my ESC's turned on, instead of off.
Cons:
- You will need scripts to control them with a movement panel.
- There aren't as much ESCs for brushed motors as there are for brushless motors, because brushless are so much better (in the rc world though).
- They only work from a certain value to a certain value, when used like a servo in ARC .
Important things when using a ESC:
- Always power up the EZ-b before the ESC.
Most ESC's their neutral position is set buy the first signal they receive from the
object it's connected to. And here is where the config of the connect button comes in, you can use that to creat a boot sequence which would set your servo position to 35 ,which is the neutral position. - Always turn of the ESC before the EZ-b, it can suddenly run of! If not, just do it, else you EZ-b wont turn off. This is because the BEC, BEC stands for battery elliminator circuit, when it's used in a rc car you don't want to carry batteries around, so they came up with BEC you could then ditch the receiver battery and use the battery you use to power your electric motors.
How to pick an ESC: ESCs are available in about every size up to 320A up, maybe even more. ESCs are rated in Amps, so you first pick your motor and then the esc that matches it.
Example: I have a 25A motor. Then you could buy a 25A ESC, but it could occour that you wheels or what ever get jammed and your motor could drain a bit more like 30A or more, this would fry my ESC... So I am choosing a 30A ESC for a tollerance of 5A. You could choose a higher tollerance, thats up to you. Almost all ESCs are able to burst power for 5 sec and 1 sec. Ofcourse the 5 sec burst is less powerfull than the 1 sec. In a burst they can double their output current, but briefly to prevent damage. Note: An ESC can get very hot, for rc racing cars they have ESCs with a small fan on top of it. Also if you pick a higher tollerance, it will take longer to get hot or wont get hot at all.
Next thing you look at are the batteries for it. They are displayed in the amount of battery cells or in voltage. When displayed in cells there are 2 ways, for Lipo and nihm. Most of the times they are displayed both so users can stay within budget as Lipo batteries are expensive.
The lipo way: 1 lipo cell is 3,7 volt, this means 2 cells are 7,4 volt and so on. They are displayed on the ESC like: 2s-3s or 2-3 lipos, this means it alteast requires a 2 cell or atleast 7.4 volt to work.
The nihm way: 1 nihm battery cell is 1,2 volt, this means that 2 cells are 2,4 volt. On the ESC they are displayed like: 8s -12s or 8-12 nihm.
The difference between Lipo and Nihm: Lipo batteries provide a larger amount of current per second than nihm batteries, this means you can go faster with Lipo batteries.
Things you look at when buying an ESC:
- Brushed or brushless, this compleetly depends on the motors you are using. NEVER and I mean NEVER try to connect a brushed esc to a brushless motor or viceversa!! Only if it is specified on the esc that you CAN use a brushed and brushless motor!
- Is it able to rotate 2 ways, it will be displayed as "reverse" if it's not displayed or you can't find it in the specs, contact the seller or try to find more information on that ESC.
- Does it have a auto cutt-off. This is VERY important when using Lipo batteries! You can destroy your Lipo batteries if it doesn't have this function. This function will stop your motor when the voltage that the is supplying falls under a certain amount (the minimum per cell is 3v, lower than that and it will DIE!!) and it will drain only a ver small amount to keep the ESC alive. Also handle Lipos with care. They can explode or start a large fire.
How to pick batteries: ESCs channel the voltage of the battery to the motor, so if your battery is 7,4 volt your motor wil receive 7.4 volt (not sure about the channeling part, I'll try to find out how that exactly works)
The lipo way: Using the examle of 7.4v you will need a 2s lipo, but there is more. A has 3 points of interrests:
First: the amount of cells (s). The more cells, the more voltage.
Second: the amount of energie stored inside (mAh). The more mAh the longer it'll last
Third: the amount of coulomb (C), those who know know what coulomb is ,but for those who don't know what it is. Coulomb = Amps per second. The more C the larger the amount of current per second that will go to your motor, this also means the more C you have the faster your battery will be empty (depending on the amount of mAh).
A forth point to always keep in mind: will it fit in your robot!
The Nihm way: Still using the example of 7.4v. When using nihm batteries you will never be able to get 7.4 volts, thats why it is written on the esc how much nihm cells you would need. Usually it's 6 cells or 7 to reach 7.2v or 8.4). When buying nihm batteries you should look out for:
The amount of cells. The amount of mAh, the more, the longer they last. The size.
For now I think I have told everything you need to know if you want to use an ESC, how to control it, how to pick it and even how to pick batteries. If you have questions, just let me know. Also check out my robot, it uses ESC to power it's motors.
Good work Can you provide a buy link
Oh thanks man, I've been typing for over an hour
.
But you can get Rc ESCs at lots of places:
My personal favourit places to get rc stuff:
-Ebay, just type in rc esc or brushed rc esc or somthing like that. -Towerhobbies ,they have lots and lots of ESCs and more. -HobbyKing, this store also has lots and lots.
The ones I'm using in my robot: Back to ebay, They're still working great, the have a reverse, auto cut-off and they are also available in larger versions.
But the ESC you need will always depend on the motors you want to use. It isn't one size fits all. That's why there are so many
and thats why I created somthing where some one could learn from how to pick one.
Great write-up
Hi,
In case your still interested here are a few links of RC ESC's like I use. The only disadvantage I encountered is that they produce a reasonably amout of heat.
http://www.flickr.com/photos/phg1961/6381887759/in/photostream/lightbox/
http://www.graupner.de/en/service/search.aspx?usterms=navy+V15R
Best regards,
Philip
Budel0 good work! I find very interesting your work, I also use rc esc for my planes, but was not sure I could use with EZ-b. I have a draft: robot with brushed motors and have a good prices and stores to find them. But then work with the servo panel moviminto changed? although you have to do a script for each direction To my knowledge there are two panels of motion: 1: panel modified servo motion 2: h bridge motion panel I seemed to read that panel does not work with modified servo motion and then if it works, I do not understand or is this script to make 5 up front, back, left, right and stop, each responds when actions panel arrows to move. Sure it effectively explained, but the technology leaves some Herror google translator in the translation I can not understand. Thanks in advance, if I can clarify this, I see a bright future for the two-way pair esc our robots, especially by a speed accuracy. eek
I plan to buy two esc like this:
www.r2hobbies.com/eng/proddetail.php?prod=rcvp3310002
Hi , You can use the "modified servo movementpanel" once you created individual scripts for: forwards, backwards, left, right and stopping. Then you can use the "movement script" to start the scripts via the "modified servo movementpanel".
"But then work with the servo panel moviminto changed?" The control via the Movement Panel hasn't changed. In one of the threads I saw or believed that I saw DJ recomending an ESC (atleast I thought it was an ESC), which later turned out to be a h-bridge.
About the modified servo window, I haven't tested an ESC since v12 with the modified servo window... So I am going to test it later today! I just saw that instead of the slow, slowest, fast, fastest there are 255 values... It didn't work because of only 4 values... Now that there are 255 it might work! This might also mean that I have to reprogram
or not
TO BE CONTINUED!
Here is the next episode:
I have tested it with the modified servo window and I have found that it does not work... With the vertical/horizontal servo it does work but not with the modified servo. I had tried lots of values so...
@PhG You can always add a small heatsink or fan to your ESC's! Mine are mounted to a gigantic heatsink, I call it my robot
, the chassis is made from aluminium. They will never get hot! Maybe if I run them for days, or 5 hours, as I calculated the maxium time my batteries would last! It could also be 20 minutes, not sure yet
the third wire of the esc is because it's a three phase motor. It's not controlling where is it but it gives the current to continue the rotation. Otherwise it will turn only by 60.
I'm using some on my robot and I think there's no way to control the rotation degrees but only the speed.
@DJ. I think a great function you could add is an esc servo controller