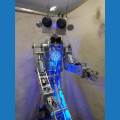
Rob-bot
USA
Asked
— Edited
Hi All,
if you are using a 12vdc linear actuator without feedback and you use a servo control board (6v - 7.2v) with a pot connected to the actuator for feedback, where would the linear actuator's 12v leads connect to being the motor outputs of the servo control board are a lower voltage?
Would you also have to have an H-bridge connected to the servo control board?
Thanx.
I don't think you can't use a generic hobby servo control board for that actuator. I doubt it could provide enough current (not to mention volts) to move the actuator. You will still need some type of larger motor controller (i.e. H-bridge) in order to control the direction of the actuator (or motor).. The role of the pot is to give position feedback. The H-bridge will control direction...
This is how it would work... You connect the actuator to the H-bridge, The ezb4 would control the H-bridge. The pot would be connected to the ezb4 analog port. With some scripting you can read the pot for position status then control h-bridge for position and direction...
Thanx Richard. Like you said, I figured I would need to use a higher voltage/current controller.
Would you by chance have an example script similar to how I need to write for my situation?
Thanx again.
A better solution is...
Purchase an HDD servo HDD Servo
Remove the PCB and Pot. Disconnect the motor wires
Connect the PCB's motor wires to your own motor
Add the pot where ever it can be measured in your application. Or use a new pot if your actuator already has one built in.
Connect the servo to your EZ-B v4/2 Wi-Fi Robot Controller or EZ-B IoTiny
Use absolutely any control in ARC that supports servos... including Auto Position gait creator, camera tracking, WiiMote, mobile apps, etc...
@DJ,
Is the HDD servo PCB compatible with a 12v motor ?
Yeah - the specs of the mosfets are actually quite high. Jeremie can chime in on that.
@DJ,
That is very interesting
@Jeremie,
More details please: i.e. max amps @ 12v
hello, i am jeremie. I don't log out of public computers.
*Edit: I'm logged out now, thanks @DJ
Hahaha.... so PTP, jeremie says the mosfet is rated for 16 volts, or something in the servo... BUT, the voltage regulator for the rest of the electronics might not be that high (maybe 8.4v). He's going to check first to verify.
The thing is, a 12v motor can still run decently off 8.4 volts, it'll just draw more amps