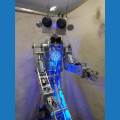
Rob-bot
USA
Asked
— Edited
Hi All,
if you are using a 12vdc linear actuator without feedback and you use a servo control board (6v - 7.2v) with a pot connected to the actuator for feedback, where would the linear actuator's 12v leads connect to being the motor outputs of the servo control board are a lower voltage?
Would you also have to have an H-bridge connected to the servo control board?
Thanx.
I see what you guys are saying, but how do I get 12vdc from the servo control board if my EZ-B is only powered by 6vdc?
The other issue is that if I were to use the lower voltage from the EZ-B to the servo control board like DJ said, the motor would definitely draw more amperage, but I believe the motor would also run much slower.
@Rob-bot You need two separate power sources or a step down power converter to take 12v to 6V This is how you do it... 12v connects to the servo board and 6V connects to the ezb4... make sure you have common grounds between them
Do you need 6v for anything (like regular servos) because the ezb4 will happily work with 12v?
Like Richard said. You only need 6v if you’re using components that require 6 volts, like servos.
If you need 12v and 6v then have two power sources. Share the same ground.
Lastly, if you’re worried about the motor moving too slow at 6v then I would simply connect an hbridge to the servo pcb motor wires. Power the servo pcb by 6 volts and the hbridge by 12.
The servo pcb will be controlling the polarity of the two output wires that also controls the input of the hbridge.
"12v connects to the servo board"
Richard, your saying I can put 12v straight into the servo board?
"Lastly, if you’re worried about the motor moving too slow at 6v then I would simply connect an hbridge to the servo pcb motor wires. Power the servo pcb by 6 volts and the hbridge by 12. "
"The servo pcb will be controlling the polarity of the two output wires that also controls the input of the hbridge."
DJ, I see your point. Which inputs should I put the servo PCB motor wires to, on the hbridge?
@Rob-bot
I got word from our manufacturer, 8.4V is the maximum voltage the HDD servo electronics can operate at. 12V is too much.
Thanx for clarifying Jeremie. That was what I thought, but I think I confused Richard.
So, I think my only choice is to wire the service PCB to Hbridge, like DJ said.
I just need to know which inputs I should use on the Hbridge.
So, this is the easiest/cheapest solution I came up with to making feedback on a linear actuator...
I siliconed a 100mm 10k slide potentiometer ($3 ebay) to the flat side of a 100mm common linear actuator ($30) and drilled a small 3mm hole through the top end of the shaft at the closest part that is exposed when the shaft is retracted inside the body and used a 90 degree bent piece of wire coat hanger with small 3mm shaft collars ($1 ebay) to keep it from coming out and drilled a 3mm hole through potentiometer slider tab and using 2 part epoxy, I added a 3mm ball joint ($2 ebay) to the other end of the wire coat hanger and screwed it to the slider tab with a 3mm machine screw and nut with some liquid thread lock to keep the nut from loosening.
It gives perfect feedback to add to a servo control board and/or hbridge to use as a linear servo to connect to your EZ-B without paying over $130 for one.
I believe you can now buy those with built in feedback ability.