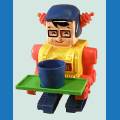
Mulberry
USA
Asked
— Edited
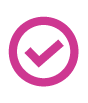
I'll make this as succinct as possible
Can the H Bridges sold by EZ and discussed in the tutorials handle standard 12v actuators? I'm talking low speed, slide out/slide in.
Thanks,
Daniel
Do you have a datasheet or example of the actuator?
All actuators run off a motor and the motor will have a current draw. The current draw is dependent on what HBridge would be useful.
@Mulberry we need a link to the actuator your are thinking about using... Depends on the linear actuator... Some are servo or RC type ( they won't need an H-Bridge), some are analog, some have pots and some have end stop switches... So as mentioned it depends on which actuator you are talking about....
Sorry for the delay in responding. Work, kids, and life :-P
So this is a 12 volt dc, 15 lbs actuator from progressive automations that I use to slide my B9 arms out along drawer tracks. If possible I'd like to avoid an H bridge. Here are the specs:
Input Voltage 12VDC Current: 5A at full load Load Capacity: 35lbs, 50lbs, 150lbs Stroke Length: 1 to 40 Screw: ACME Screw Duty Cycle 25% Operational Temperature: -25ºC~+65ºC Limit Switch: Built-in Non-Adjustable
Full details are here: http://www.progressiveautomations.com/mini-linear-actuator
Any advice would be greatly welcome.
Thanks,
Daniel
It looks like it uses limit switches... Which means you don't have much control in how much you extend and how much you retract... So basically It will move in and out until it hits a limit switch... If you want to only extend it half way you can use a sleep command to count and then stop after a required amount of time... Although this won't be very accurate...
To drive it you will have to use an H-bridge or some other motor controller... There is no other way to reverse as once it is extended you will have to then retract buy reversing the polarity somehow... Other than physically swapping the battery wires, a motor controller like an H-bridge is pretty much your only option....
Could you use a pulse counter on the shaft? I have used a pair of relays to reverse polarity to the motor. Its a clunky way to do it. confused
@Mullberry I use high amp dc window motors for my robot's shoulders, and I'm using a homemade h bridge to control, and it works fine for me. I then use a potentiometer (100k) to read position feedback. I used GetADC to read it. It works for me. You can use this setup and install a wheel on your pot, to read the slide in/out of the actuator arm.
Here's what I did. Hope it helps.
Thanks all. Deep in my gut I knew I had to use an H bridge
I hate H-bridges.
Daniel