Hello all, I am getting back in the saddle making robots now that I am moved into my new home and settled into my new job as a technician maintaining the Fiber Optics network in Chattanooga TN.
IM BACK !
By jstarne1
— Last update
Other robots from Synthiam community
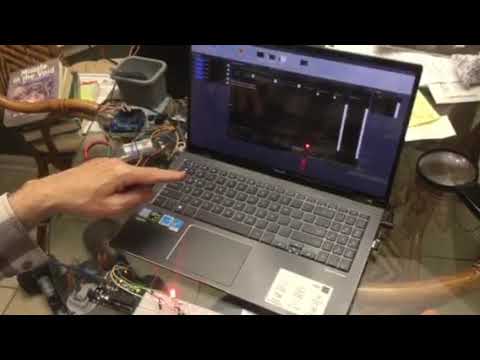
Ezang's RGB Arduino, Python Code With ARC
Here is an example of using the ARC serial monitor I am using an Arduino, Python code, with ARC - watch the R G B light...
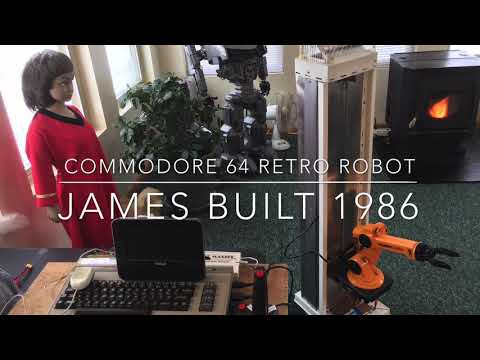
Steve's James, Commodore 64 Retro Robot That Learns And Uses...
Been trying to keep busy, so I dragged my 35 year old Retro Robot upstairs, and got him operating again. With the 6...
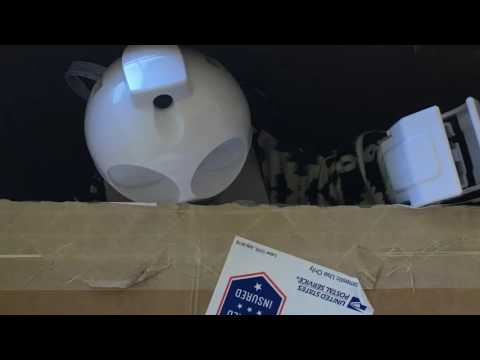
Pashley's Jd Days
A package arrived in the mail a few days ago. I must admit this might not be exactly how the un-boxing went. I seem to...
This project is screaming for Robotzone servo Power Gearboxes!
HAHA, I already have two of them chilling somewhere I can use. I believe I have the 5 to 1 gear ratio , servo gearbox with 3 inch aluminum arms.
OK so I need a drive train. I am considering using the trucks power wheels gearboxes and then the hubs already connected to the wheel, I will just need to see how that fits. My second option which I believe is stronger and more reliable are two Ryobi Drill motors and gear boxes. I can connect a sprocket to the chuck and a sprocket to the wheel as a drive mechanism for each side.
Inside this drill
Useing the drill motors is a fascinating idea. Cant wait to see how you work them into the drive train. Thous little motors sure are powerful. What voltage are the motors and what are you planning to supply to them? I imagine if they are 18v drills and you supply 12 that wouldn't hurt the motors, just slow them down a little.
Edit: Looking back at your shopping list I see you have 40v batteries and the drill motors are 18v. OK, then you can step down the 40v to 18. Any thoughts on what you plan to use to do that?
I have a couple options when it comes to lowering the input to voltage to the drill motors. First is using a voltage step down or buck converter. Second option - I am already going to need a motor controller (unless I used relays) , I can use PWM to lower the input voltage. The lower the PWM signal / duty cycle , the lower the effective voltage applied to the motors. I would clearly not have a PWM that allowed the voltage to go above what it was designed for. Most likely I would reduce voltage a couple volts to keep heat down.
Ok this step down converter with a claimed rating of 350 watts is on the way. Of course I probably wouldn't trust it past 200 watts. I have two on order that will be here in 7-10 days.
Module properties: non-isolated Adjustable Auto Buck Boost Converter(non-synchronous rectification) Input Voltage: DC10-50VOutput Voltage: DC10-50V(default 19V shipmet,adjust the blue adjustable resistance to change output voltage)Output Current:Max 20A(Because of the limitation of Max output power,the output current Max 20A)Output power: 350W Max Output voltage current LED meter display: Double four digital 0.28" tubeOutput voltage meter:Blue LED display 0-100VOutput current meter:Red LED display 0-20A Fan:DC 12V Double Ball Bearing Fan(The fan Automatic Control for Thermostat,Automatic start or stop)Operating temp:-40 ¡ãc +85 ¡ãc Input anti-reverse protection:Yes (can be long time to reverse,do not burn module)Output over voltage protection:No(output voltage exceeds 50V)Over temperature protection:YesDimensions:length 113mm x wide 78mm x high 56mm including the fan
OK here is the proposed controller to run the two drill motors. I have one already on hand. If anyone has objections let me know. Thanks!
The Sabertooth 2X12 is one of the most versatile, efficient and easy to use dual motor drivers on the market. It is suitable for medium powered robots - up to 30lbs in combat or 100lbs for general purpose robotics.
Out of the box, the Sabertooth can supply two DC brushed motors with up to 12A each. Peak currents of 25A are achievable for a few seconds.
Overcurrent and thermal protection means you'll never have to worry about killing the driver with accidental stalls or by hooking up too big a motor.
Sabertooth allows you to control two motors with: analog voltage, radio control, serial and packetized serial. You can build many different robots of increasing complexity for years to come with a Sabertooth. Sabertooth has independent and speed+direction operating modes, making it the ideal driver for differential drive (tank style) robots and more.
The operating mode is set with the onboard DIP switches so there are no jumpers to lose. Sabertooth features screw terminal connectors - making it possible for you to build a robot without even soldering.
Sabertooth is the first synchronous regenerative motor driver in its class. The regenerative topology means that your batteries get recharged whenever you command your robot to slow down or reverse. Sabertooth also allows you to make very fast stops and reverses - giving your robot a quick and nimble edge.
Sabertooth has a built in 1A Switching 5V BEC that can provide power to a microcontroller or R/C receiver and a couple of servos. This built in BEC is almost identical in performance to our ParkBEC. The lithium cutoff mode allows Sabertooth to operate safely with lithium ion and lithium polymer battery packs - the highest energy density batteries available.
Sabertooth's transistors are switched at ultrasonic speeds (32kHz) for silent operation.
Solid choices. Hey, I have 4 or 5 (or more. I have to check) brand new Sabertooth 2x12 units. Two are slightly used. I switched all my Tooth's over to the 2x32 because I'm running my B9 off a power supply and they let me clamp the regeneration voltage instead of needing a voltage dump battery. If interested I'm willing to sell one or more to you for $60 USD each, plus postage. If you buy them all I'll ship free.
Let me know if you are interested. If not I'm putting them on ebay (someday,lol).