Hello all It's been a while since I posted, been busy catching up on back orders for IKON so that took up most of my time.
I finished Doombot's skeleton/frame and I took him apart to make molds so I can reproduce the parts in aluminum and carbon fiber and kevlar. Its gonna be one mean deadly machine.
Anyway in the meantime I created Dirgebot, a smaller, less menacing and simpler to program (less moving parts) machine that's somewhat kid-friendly (for me). I wanted something my kid can play with (she wont even go in the room where Doom was parked).
Anyhoo here is the progress. Depending on how this proto goes I may market this model as a complete, not a kit, but something that can be used out of the box with no guesswork. I'm looking for an ARC programmer who can work with me, in exchange for stake in the future company. I recently established Bertone Industries, LLC and I have access to a warehouse and it will be manufactured here in the US using rotocasting techniques. Please contact me if interested here: [email protected]. Thanks guys!
:D
This still uses the V3 board and a webcam, alongside the W3 Iconia mounted on its chest. I will upgrade soon. Please be nice to us dinosaurs! haha
He stands at 3' 4" currently.
Testing the arm
Head armature
Sketching the head
Chestplate attached
Nearly finished sculpt. I'm gonna make a tutorial for making molds and casting fiberglass panels. This head is gonna be produced in fiberglass, alongside the rest of the robot when the sculpting is done. Hope you all like it.
Other robots from Synthiam community
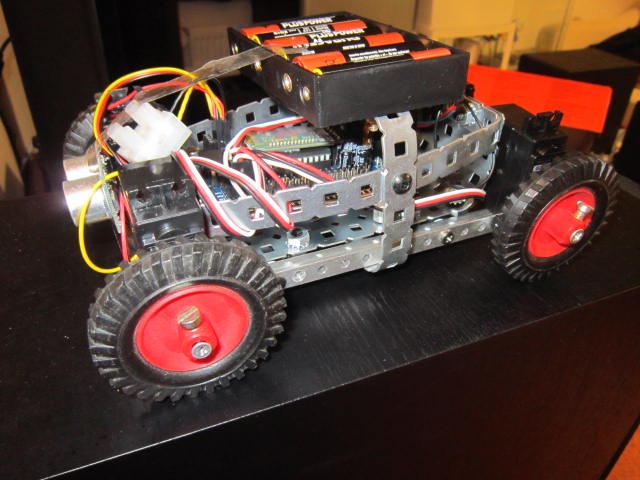
Cosplaying's Project Mini Rover
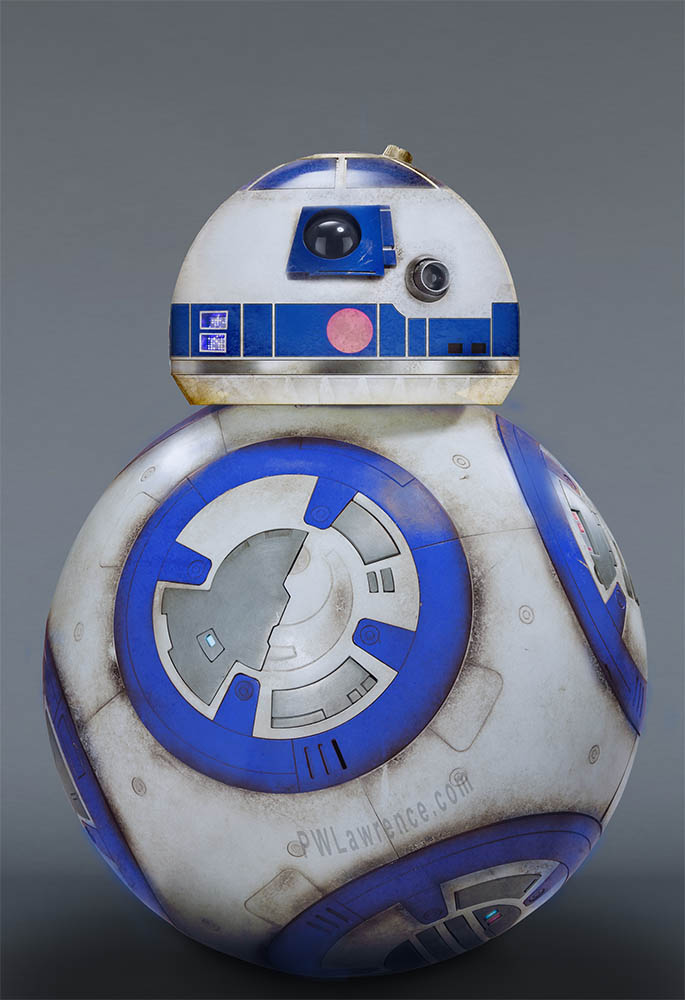
Sulla's R2d2 Bb-8 Mashup Robot Project
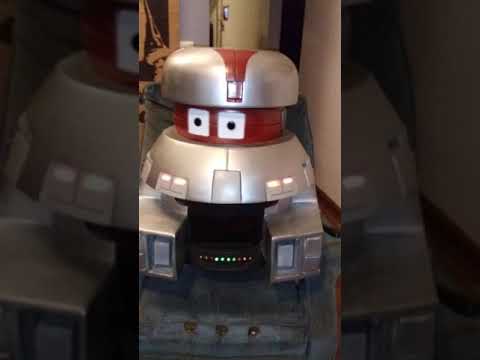
oops, I think I messed up on the pics. Here they are againeek
Welcome back... Your bots are always so menacing looking... Love them...
Thanks @Richard R!
Jeez still "menacing"? This is about as commercial as I get haha
@Anthony Thanks brother! I think this is the first time you ever commented on my work...I love the new Chappi design you're working on. Especially the body.
Welcome back! I was just wondering the other day how your first bot was coming along. Now I see a second one about to come into being. Very exciting and impressive. I'd love to see some videos of those big arms working and know what motor and feedback you used to make them move. Love your style.
Thanks @Dave Schulpius!
I saw your arm and boy is that heavy duty! A ton of high dollar parts on that! Are we using the same window motors for the shoulder joint?
Its not on the photos yet, but I have a potentiometer hooked up on the other end of the shoulder to read feedback. I'm still deciding on what hbridge to use.
I can't wait to unveil Doombot. He's evolved into something nasty, almost military-esque.
Lookin forward to this..... !
Looks very cool.
Alan