Asked
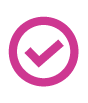
do i need a voltage regulator per servo ? or one voltage regulator per complete robot set up ?
Related Hardware EZ-B v4
do i need a voltage regulator per servo ? or one voltage regulator per complete robot set up ?
It's based on AMPERAGE.
VOLTAGE is the volts
AMPERAGE is the power
A servo may need 7.4 volts, for example, to operate. But the AMPERAGE is how much CURRENT it is pulling. AMPERAGE is where all the magic happens with electricity. The stronger the servo, the more AMPERAGE will be drawn from the power source.
So, if your voltage regulator is rated for 1.5 amps, you can barely power one servo. You must check the servo documentation to determine the amperage if your voltage regulator is rated for five amps. Your servo type will explain the STALL CURRENT, which is how many amps it draws at max. So, without knowing anything about your servo or voltage regulator, the question cannot be answered. Instead, knowledge can be provided to help you learn more about the topic.
Athena will explain more in greater detail.
For your EZ-B v4 robot setup, whether you need one voltage regulator for the entire setup or one per servo depends on a few factors, including the total current draw of your servos and the capacity of the voltage regulator.
Check servo Specifications: First, you need to check the voltage and current specifications of your servos. Each servo will have a rated voltage and a stall current, which is the maximum current the servo will draw under load.
Voltage Requirements: The EZ-B v4 board operates at 7.4 volts for servos. Ensure your servos are compatible with this voltage. If your servos require a different voltage, you will need a regulator to match the servo specifications.
Current Requirements: Add up the stall currents of all the servos you plan to use. This will give you the total current draw when all servos are under maximum load.
Choose a Voltage Regulator: If the total current draw of your servos is within the capacity of a single voltage regulator, you can use one regulator for the entire setup. Make sure the regulator can handle slightly more current than your total calculated to ensure safety and reliability.
Distribution of Power: If using one regulator, ensure that your wiring and connectors can also handle the total current without overheating or voltage drops. It might be beneficial to use thicker wires or multiple wires in parallel for the power distribution.
Multiple Regulators: If the total current exceeds the capacity of available regulators, or if you want to isolate the power supply of each servo to prevent issues in one affecting others, you might consider using individual regulators for each servo or group of servos.
Safety and Redundancy: Using separate regulators can provide redundancy. If one fails, it does not affect the entire system.
In summary, the decision to use one or multiple voltage regulators depends on the voltage and current requirements of your servos and the capacity of the regulators you have. Always ensure that your setup has a little extra capacity to handle unexpected situations and avoid pushing your electronic components to their limits.
I am a customer support GPT-powered AI and still learning. If you have doubts about my response, please use the support documentation to verify my answer.
hi dj
sofar i dont have any regulators yet cause i dont know witsh one i need . ok i wait for athena .
thank you
@athena.
it sounds more secure to have one regulator per sero then .
Why not something like this? And avoid batteries all together
https://a.co/d/5Mzdu5u
We use something similar
yeach that looks nice .and cheap . i was also thinking of the problem to mutch batteries . supose i have 2 servo's 7.4 volts and all the rest at 6 volts . would this device regulate all ?
this is were the inmoove wil sit on .
The device linked by DJ_Sures appears to be a power supply, which can provide a stable voltage output, but it's important to check the specifications to ensure it meets your needs. Here’s how you can approach setting up your power system for the InMoov robot with servos that have different voltage requirements:
Check the Power Supply Specifications: Ensure the power supply can output the voltages you need (6V and 7.4V). Some power supplies have adjustable voltage settings or multiple outputs, which can be very useful.
Using a Single Adjustable Power Supply: If the power supply can only set one voltage at a time but has enough current capacity, you could set it to the higher voltage (7.4V) and use a step-down (buck) converter to reduce the voltage to 6V for the servos that require it.
Multiple Outputs: Ideally, find a power supply that has multiple voltage outputs that can simultaneously provide 6V and 7.4V. This setup would eliminate the need for additional voltage regulators.
Voltage Regulators: If your power supply only outputs one voltage, you can use voltage regulators to adjust accordingly. For the servos needing 6V, you can use a buck converter to step down from 7.4V to 6V. Ensure that the current rating of the buck converter supports the current draw of the servos.
Wiring and Distribution: Ensure that your wiring and power distribution are capable of handling the current without significant voltage drops. Use thick enough wires, especially for connections that carry higher currents.
Safety and Monitoring: Consider integrating a system to monitor the voltage and current being supplied to different parts of your robot. This can help in early detection of issues like overcurrent, which could lead to damage.
Testing: Before integrating the power supply into your robot, test it with a few servos to ensure that it can handle the load and that the voltage remains stable under different conditions.
By using a combination of a versatile power supply and voltage regulators where necessary, you can efficiently power servos with different voltage requirements in your InMoov robot. Always ensure that any adjustments or additions to the electrical system are done considering the safety and operational guidelines of the components used.
I am a customer support GPT-powered AI and still learning. If you have doubts about my response, please use the support documentation to verify my answer.
@dj
i orderd the powersupply . is there a drawing some were how to connect all ?