
bmarkert1985
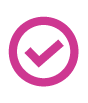
Hi,
I am working on creating a full scale humanoid robot using the EZ-B V4 controller and the servos from the JD robot. The servos are attached to a 3D printed skeleton. The battery would only last about 1 minute before the "my battery is low" warning came on. I thought I damaged the battery. So I purchased a new battery charged it for 1 1/2 hours, installed it into the controller and the controller did the same thing, the battery lasted about 1 minute. So now I suspect the load is very high on the servos and drains the battery quickly. It there any way to connect the charger directly to controller without a battery? I see other custom robots on community site and they don't appear to be battery powered but using EZ_B V4 controllers.
Thanks for your help, Brooks
First off I think you need to understand ohm's law first before going any further. And know the difference between amps as it pertains to current vs capacity.... You need a power supply not a battery charger.... Be aware you need one that has a minimum of 20amps for running multiple servos. I use a 6v 50amp power supply to run my inMoov. 6V because it uses 6v Hitec servos not 7.4v ez robot servos.....
Thanks so much for your help. I'm running 8 servos. I will search for 7.4V 20amp power supply. I can then connect it directly to the power input cable of EZ-B V4?
It's hard to say what is going on with your battery. Not enough information. What kind of batteries? What size? How many servos are you using and are they all from the JD? Are you using all of them?
If I had to bet I'd say you have to much amperage being drawn from the batteries and perhaps the wrong type of batteries.
You do not want to just hook up a battery charger to your robot to keep the batteries charged. Charge the battery with the robot powered down. You do not want to use a battery charger to power your robot. That's not what the battery charger is intended to do.
You can use either the right type and sized battery or an external power supply. However without a relay switching system to change from one source to the other it's hard to use both. There are simple ways to manually switch from one to the other but it sounds like you are not at that level yet.
Lets talk power supply, load and distribution. First you need to know that voltage and current (amps) are not the same thing. Amps are drawn by the devices in your circuit. Devices like your servos. If your devices are trying to draw too much current then the power supply or wires and connectors can handle a number of bad things can happen. Moistly heat. a device only knows it wants current so it can run as designed. It will keep pulling that current till it gets it or something in the chain breaks. The worst case is things will get hot, burn and catch fire. Best case is your power supply will shut down (Power converters) or drain (batteries). You must have your power supply, wires and connectors sized large enough to handle the current (amps) that all your motors, lights and devices will draw.
To insure that you have a properly sized power circuit you first need to add up how many amps all your motors, lights and devices pull at peek load. Once you know that you can decide how big the wire and connectors need to be to transmit your power and how big of a power supply you need.
Now that you have that knowledge you can decide if you want to use external power or battery power. You can certainly use either or both as I said earlier. If you go with a power converter and know how many amps you need to draw there are many choices. If you have a small load (maybe less then 2 amps) you may be able to go with a little wall wart. They say right on them how many amps they are designed for and the voltage they will put out if plugged into the wall. Forget using them for motors. Lets say your robot can pull up to 20 amps. You will need a quality AC to DC power converter. Get one that is able to handle at least 25% more load then what your peek amps are going to be. So in this case I'd get a 30 amp power supply (Because that's the next larger one available). Feed it with power from your home outlet and attach your devices to the lower voltage DC side of the converter. One more thing; Make sure you get the proper voltage power converter your devices will need. They usually come in different voltages from 3.3vdc to 48vdc. Here's a 12V 30A Switching Power Supply that may work with our scenario above if your devices use 12vdc:
AC to DC power supply (I do not have an opinion on the PS i have linked to. I't just an example).
Now Batteries? Mostly the same applies as far as designing your circuit and power feed. However what does differ is the type and size of battery. A lot of people use Lipo batteries now because they will handle a motor's amp draw better then most other type's of batteries. I'm not a good person to give advice on batteries. However I do know that if you are just using a AA battery pack on your full sized robot with a ton of servos then that is your problem. You need the proper size and type of battery.
I hope this helps in some way. Good luck and have fun.
What ever voltage you power the EZB v4 with, you will also have coming out of the powered digital ports. The EZB can handle between 4 and 17 vdc.
You are not going to find a power supply that will give you 7.4 vdc. You are going to have to get a higher voltage PS and buck it down with a converter. They have very affordable and adjustable power converters available. Just make sure you get one rated for the amps you are going to draw through it.
Thank you Dave for your time and in depth explanation. It's very much appreciated! I'm using 8 servos from the JD robot. I'm using the Lipo 1300 mAh EZ ezrobot battery that comes with the JD.
The battery that comes with jd should last an hour or even much longer - entirely depending on how much activity the servos are moving.
Perhaps the battery isn’t wired correctly to the ezb? Which is hard to imagine but you never know. Or what are the servos lifting? If it’s lots of weight? Or is the charger given enough time to complete the charge?
is the battery puffy?
these are things you might want to check the ezrobot learn section about. Check the learn section on ezrobot website about proper battery care of their product. It would be unsafe to use a battery that has been neglected and puffy. It could explode - so they provide warnings on the website and in the packaging to properly review the tutorials and manual.
The op did say he bought a new battery and charged it for 1.5 hours. That seems quick.
Yeah - 1.5 hours is not long enough, unless the battery was already mostly charged. Once the EZ-B says "my battery is low", it would usually take a number of hours to charge (4-8 hours)