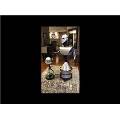
Ellis
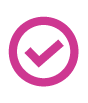
I appreciate any help in understanding what I am doing wrong. I have a modified servo panel and a logitech joystick control installed. I have the wheels on d0 and d1. I have two servos with one on d3 and d4. The wheels are running correctly on the joystick but the two servos are running totoally intermittent on the second stick on the joystick controller. I have tried to program joystick 2 and 3 and actually both at the same time. I am all over the place. Sometimes the X servo works sometimes the Y servo works. Sometimes neither and sometimes both work. I am at a loss at what I am doing wrong. Can anyone help.
Also when I got them both running one time using joystic 2 and 3. I tried to first locate the servos with the Servo(d2, 50) and Servo(d3, 50) and then slow them down with ServoSpeed(d2, 25) and ServoSpeed(d3, 25). I put this script in the initiation File. It slowed down the servos to a crawl and they wouldn't work until I used the joystick. They also did not seem to want to find position I requested. I know this is something I am doing but to the life of me I cannot figure it out according to the ARC manual or the EZ-Script manual. Do I need to add ControlCommand script? Any advice you can give would be greatly appreciated. Thanks Ellis
what are the wheels mounted on Servos or Motors? and are the servos on D3 and D4 modified also, or standard servos? can you post a screen shot of your configuration for the Joystick control and servo Panel?
Also Modified servos wont find position it removed with modified..
Maybe you can explain a little more of what you are trying to do... You can only have one Movement Panel linked to a joystick (left joystick)... This would be for driving the robot around... The other channels of the joystick you can use for regular 180 degrees servos only.... However you can use all the joystick channels to drive just standard 180 deg servos if you don't have a Movement Panel in your project... Put all the servo speeds back to normal and try again...
Part of the problem is the values you are using for servospeed. The range is 0, the fastest, to 10, the slowest.
Alan
Answer to questions:
Two HB-25 motor controllers hooked to pins d0 and d1. These are used for forward, reverse, left and right movement of the robot.
Two 180 degree standard servos for horizontal and vertical head movement on d2 and d3. I am using these to control head movement and future camera.
I am controlling these with a Logitech wireless controller.
I have set speeds and location back to 0 rebooted and it did make vertical servo move up and down correctly using the right joystick. I have tried programming this joystick with joystick 2 and three. I do not know if it makes a difference but neither would control both axis at the same time. I programmed joystick 2 and three at the same time and both worked but acted random.
As for the values on speed I have tried various speeds from 10 to 0. It will slow servo down to crawl but doesn't seem to do this proportionately. 2 seems to be the same as 8.
I have looked on the samples and am going to add some code like you have done on different units to see if I can get it to work correctly.
Any Ideas.
I will be receiving a Logitech Joystick in a couple of days and if you haven't resolved this by then, I'll do some experimentation to see if I can figure it out.
Alan
Why do you need to slow down the 180 deg servos (vertical and horizontal head movements)... When I use a joystick control for a pan and tilt head or camera mechanism I like the servos to move at full speed...
Ok as far as the HB-25s are concerned... Do you have a h-bridge movement control (Not the Modified servo movement control) in ARC set up for them? These are parallax motor controllers right? For regular DC motors (not servos) right? The left joystick control will drive the Movement Panel which in turn would control your 2 HB-25s (and the dc motors connected to them)....
If you're are using modified 360 deg servos to drive your robot then you don't need the HB-25s... You're Movement Panel will then be the Modified servo movement control....
Yes my HB-25s are connected to control two 12 v dc motors. I used a modified servo panel to set them up. I used the modified servo panel because they are connected with a standard servo connection. They do not use the center pin as they use a separate 12 v power input to run motors. The HBs are supposed to be hooked up as standard modified servos. They are working fine with the left joystick. They do not ramp up to speed yet but l will try to in the future. They are presently a little jerky since they are powerful motors.
I am trying to slow the servos down because I am using an elongated iPhone car mount to provide the head. Since it has a long neck it amplifies the movement.
I may be doing several things wrong but I am in the process of learning this whole system.
Thanks for helping me in such a fast fashion.
Thanks also to Alan. Let me know what you find out.