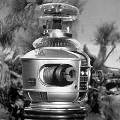
steve.neal
Australia
Asked
— Edited
I seem to be having trouble with one of my Sabertooth/kangaroo motor controllers. The red error light is on and the the motor will not work. Up until now it has been working fine. I suspect what may have happened, (not sure if this is a thing or not), I had the motor/encoder unplugged from the sabertooth and had run the initiation script while testing other things on the robot. I have tried re-auto tuning but this does not help. How do I reset the red error light? Everything seems to be connected. I cant see an obvious reason for it not to work.
Steve
There's a short or a misconfiguration in the wiring. The kangaroo cannot output 15 volts - and that 15 volts is most likely from a 12v battery.
Good news is that is the problem - there is a short or wire connected incorrectly. This could be inside the motor encoder, or simply a wire of incorrect color to the wrong place. So you do have some direction to take.
Bad news is it's pretty difficult for us to help diagnose the wiring, it's up to you
What you can do is disconnect the motor/encoder entirely from the kangaroo. Then probe the wires at the kangaroo without the encoder hooked up. You should get 5 volts and 0 volts, never 15.
Also probe the motor encoder wires unhooked from the kangaroo. If you get 15 volts, then the issue is at the encoder.
I'm happy to help Steve. I know how frustrating this stuff can be. When I first started to use the Kangaroo I had many weeks of trial and error getting my first tune to complete. The problems always ended up not being in the roo but in my system. Wiring or connector problems mostly.
Oh, that reminds me, Double check your crimps at the molex connectors that attach to the encoder and limit switch pins on the roo. I found one or two that I thought were good but actually crap squeezes by me and caused problems. I've made a thousand of these connections over the years but once in a while I squeeze a bad one.
OK, I also asked myself why you're getting 15 volts at pin A&B. Wish I knew. Only things think I can think of:
*You're testing wrong (sorry) *Bad tester (low battery?) *One of your circuits is shorted to your 12v circuit somewhere and back feeding through the encoder to the roo. *God only knows
Too bad you didn't save your last working tune. You could jump start your roo with it. Don't fee bad I made the same error at first. Cost me a lot of time to get back to where I was. I've attached a zip file with my working tune of my radar. You can install into your roo and it may help get you started. Before you start it up your going to have to load it into the DeScribe software and change the feedback from Analog (Pot) to Digital (Encoder). Your using a different motor then me also so the other settings wont work well and the end points will be wrong. However this will be a way to see if your set up at least starts up. Let me know what happens.
Radar2.zip
EDIT: I see DJ answered while I was typing and getting the ZIP file ready. He as usual is giving good advice and in a more elegant way then I could. Good luck.
Another Edit: If you are in fact back feeding 15v into the roo's A&B pins you may have damaged the roo. tired
Hi DJ,
There is no battery in the robot at all, just a power supply that puts out exactly 12 volts. I'm certain as I can be the wiring is connected correctly, but stranger things have happened and I will check it all again for the umpteenth time
.
I am intrigued to measure the voltages of and find out what the second motor will return, (which is actually the original motor I had in the robot and swapped to try and fix this problem). Maybe the brand new motor/encoder, which is in the robot at the moment has a faulty encoder.... hard to imagine though as the same problem was there with the original motor too, but the original one is the one that works if I connect it directly to the sabertooth...... ARRRRH, my brain is melting. I will do some more testing when I get home tonight and keep you guys posted. Thanks for all the advise.
Steve
OK, here's where I'm at, With The original motor encoder connected to the roo, and the original motor power wires connected to the tooth M1 terminals, and the limit switches in the robot connected to the roo, I can get the auto tune to start. Of course I have to pull the fuse to stop the motor as it is not running the radar, it is just sitting on the CSS. I measured the terminals on the rear of the roo and the results are as follows. (All voltage results are with the power on and the motor NOT running)
GND to A = 12.3 volts GND to B = 4.98 volts
Keeping in mind that this motor works with the tooth/roo, I'm still very confused. No zero volts in sight.
To further my confusion, I lengthened the encoder wires with 1 metre servo extension leads. The motor still will start an auto tune but with the longer leads, the voltage measurements are slightly different.
GND to A = 13.47 volts GND to B = 4.97 volts
Not sure why the voltage goes up on the GND to A pin. I would have thought if anything it would have gone down with voltage drop caused by the thin gauge longer wire.
I have also tried unplugging the encoder on both motors and with the multimeter set to ohms, I measured from the VCC pin to both the A and the B pins and the readings were the same for both motors
VCC to A = 5.08 ohms VCC to B = 5.10 ohms A to B = 10.19 ohms GND to all the other pins = 0 ohms
I'm going to have to resort to dismantling the radar section, yet again and cut all my hard work to remove the new motor.., again, and first see if it will work connected directly to the sabertooth as the other motor does. If not I will have to put the original motor back in the radar and try to get it working by temporarily connecting it and then trying the permanent wiring a section at a time.
tired Steve
If you're only taking voltage readings while the motor is running then according to my tests you should see voltage at these two pins on the roo. When the motor is stopped and the Roo is powered up you should see 0v at each of these pins. I don't think the different voltages on each pin is a problem and may be proper. However that 12v+ reading is still blowing my mind. It really seems like you're somehow getting the motor's 12v power feed through the encoders 5v circuit feed from somewhere.
Did you try DJ'S suggestion of pulling off the connection at the roo and voltage testing both encoder side and roo side while energized to see what your voltages are? That will tell you what direction the problem is at least. However I'd be surprised if you got any voltage from the encoder side because it should get its power from the 5v pin of the roo. But that is what testing is all about.
Did you see my previous post where I attached a zip file with a working copy of my Radar roo tune? Try adjusting it like I suggested and uploading it to the roo to see if you get any changes. Don't forget to power cycle the roo after the upload. If you can get this tune to move the motor at least you can have a little control hopefully.
One last thing for now. Take another look at the limit switches. Physically discount them from the roo, clip on a continuity tester and physical open and close them. Watch and listen. Make sure they are operating properly with clean open and closes. I've had more than a small share of new micro switches malfunction. Old switches will fail like this more often after a few thousand operations. I'm always replacing micro switches on my pinball machines because of this.
Hi Dave,
I was only taking measurements with the motor not running. I did try DJ's suggestion to remove the encoder signal wires, I removed them from the plug that plugs onto the roo while leaving the +5 volts and ground wires in the plug so I would have supply to the encoder and I could read what was coming back from the encoder on the signal wires. Unfortunately I didn't wright down the results at the time and now I cant remember for the life of me. It definitely wasn't zero, it was something high again. Wish I could remember but this fault is really beginning to get to me and my brain is beginning to shut-down, possibly as some sort of self defense mechanism.
Thanks for the Zip file of your radar tune. I haven't tried it yet, if all else fails I will have to try and work out how to load it into the DIScribe software and adjust it for my needs and see if that will work.
As for the limit switches, I have proven their functionality with a continuity tester multiple times and I also have by-passed them by putting a direct short on the limit pins on the roo by using a modified 4 pin plug with shorted wires to simulate NC contacts
I'm just about to start ripping the new motor out of the radar and I want to test it out of the robot to see what happens. I'm starting to wonder if this is all just because kangaroos just don't like Hall Effect encoders.
Steve
Can't write much as I'm getting ready for work after a good night's sleep. Lol.
I truly understand the flusteration you're going through and feel for you. Been there and done that. I'm impressed by how you're sticking with it. Understandable why you shut down sometimes. Keep up the good fight. Your not only helping yourself but others down the road.
I'm not sure but I don't think you should be getting a higher voltage back from the encoder. You may be right that the roo doesn't like that type of device. Have you tried calling DE yet? They may have some answers.
Hi Dave,
I'm quietly..... (very quietly), confident that I may have found the gremlin in the system..... I think..... I hope. I removed the new motor out of the radar, the one that refused to work. I connected it directly to the tooth/roo and it worked. So with that in mind I wanted to see if EMF is the culprit. I connected the encoder and limit switches using the VGA plug and the power to the motor run completely separately and it worked. If I reconnected the motor power through the VGA plug, it stopped working. It seems it was EMF after all.
I'm now going to redesign the disconnect-ability of the head section ... again and plan to use separate shielded cables and plugs for the encoder and power. This time I'm going to do some bench testing to confirm that shielded cables will work as they will still need to reasonably close to each other inside the collar so I don't have tangling problems with the other cabling in there for the ears and brain lighting which needs space to move when the radar turns and the bubble goes up and down.
I'm afraid I'm not going to have much time to work on the new design till next week but at least I think there is a light at the end of the tunnel with this problem. If it works I will finally be able to start moving forward again. YAYYYYY.
I will keep you posted on how it works out. Thanks for keeping me from loosing my mind
Steve