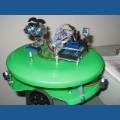
MovieMaker
USA
Asked
— Edited
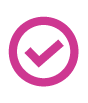
Ok, I don't really know how to word this question.
I re-built my Sunshine robot. Her arms and shoulders were very weak. so, I replaced the servos with ones that are very strong.
I setup the robots, I thought to the right positions.
When It came time to test her, I started with her right shoulder. It seemed to work Strong, but, it did not go into the correct position. It HIT itself onto her body really hard. It broke the right arm and shoulder in two places. I had noticed the shoulder was flimsy. Then, I noticed that the elbow was broken.
Maybe I could put some PWM into it and make them run very slow until I get them set to where i want them.
I guess I need some advice and direction. What would you do?
Thanks in Advance.
Mel
Assuming you are using horizontal or vertical servo controls for these, you can add a servo Speed control for each of the servos (you can also control servo speed in scripting).
You can set the minimum and maximum values in the servo control to keep the servo from going too far as well.
I would always suggest bench testing new components before putting them in the robot so that you know the characteristics. Testing outside the robot, you would have seen how fast (granted, unloaded, but it would give you an idea) and how many degrees the new servos turn.
Alan
Remember that if you read the EZ-Script manual regarding the ServoSpeed() command, that you must set a servo() position before using servospeed().
Ie you must initialize the servo port before setting the speed.
In other words, you must start the engine before hitting the gas
thanks, Guys.
Aside from the servo speed issue, if the servos may break your joints you may want to consider strengthening them. It may add some weight to the arms but it will make the arms last longer. A sudden movement could break the mounts, brackets etc. but over time so will the stress placed on them.
Also... In the future try and set up your servos to a neutral position.... So when you initially apply power to them they don't move to a position that would cause binding or in your case, damage.... Once you first call your servo position in ARC, you can then set the speed at which they move at....
To add to Richard's good explanation;
When servos are first powered up they usually go the the neutral spot (Center) by themselves. It's a good idea to power them up and set the max and min travel values in ARC before you attach the horn to the servo and install.
So, find the servo's natural "Center", set the Min/Max values, operate it through ARC with either scripts or the servo movement panels and make sure when you power it down it is at it's center. Then you can mount it in your robots "At Rest" position. This should keep it from twitching, jumping or running away when you power up Sunshine.
Thanks to all of you.