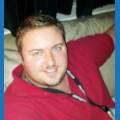
jstarne1
Ok dc to dc converters can allow us to drop a battery voltage saaaay like a 7.2 v rechargeable down to the 6volt the servos and ezb need. Motors can handle a little overvolt sometimes. This is useful for dropping voltage for lights and LEDs too so your not wasting lots of power through tons of resistors. In my case I have a 12v motherboard and everything else runs lower voltage so the motherboard PSU goes straight to 12v and everything else is dropped to 6v as seen in the picture. Dc to dc converters range from 2 to 10th dollars on ebay. I opted for the nicer one with built in led display to show both input and output voltage which.is great for setups and trouble shooting without using a meter on every connection. Dc to dc converters are up to 96 percent efficiency meaning 4 percent is lost through heat.
Nice schematic! This will come in very handy. Thank you.
Excellent. Really appreciate this.
Alan
Nice drawing! What are you using to create your drawings? I'd like to get mine drawn up like this. I like the DC to DC converters.
Lol this is just paint shop the free program with Windows.
@brett , Alan. Your welcome guys. Im drawing schematics so ill have a planned Map instead of winging it. Just too many wires for that inside my bot. After I finished this one I thought others might find it useful.
@jstarne when using dc-dc converters you need to watch the max current it can handle and add each servo stall current most common servo's draw up to 1 amp stall and your 2 amp rated dc-dc converter can handle only 2 dc-dc conveters not always the best to use ,unless you are looking to isolated other boards and stuff,when you use them you lose some power,better idea is LDO ( low drop out regulators) ,also adding weight so more draw on power
i see you are using 2 AMP dc-dc converter to 10 amp esc it will burn out same for driving four 2 amp esc with a 2 amp dc-dc converter also one you are using draws alot more then most dc-dc converter all those leds
If I need more power ill wire in higher amp converters. For now I have 2amp versions but there are 5a and 10a versions. I will check things with a good meter individually and exchange the dc to dc converters as needed. Dj used a 1.5a controller on his omnibot so even though mine handles 10a it should draw very little , but that's testing stage. I've set it up this way for easy swaptronics (change out a identicle yet better board)
@jtarne it does matter igf you use a 10 amp esc thats good part it what each motor has at stall current you need to be worry a bout , stall current and drive current is 2 different types stall current is when you hold the shaft from turning about 1/2 min or so and measure the current or look at the specs on the motor,mostly your motors have atleast 4 amps if using the same motors that came with the omnibot thats 8 amps stall on servo's on a standard servo its most 1 amp stall,because of the h-bridge cut-off if if using 4 servo's 4 amps and so on ,now on normal operating current is much less at my work we have a motor tester to check rpm,stall drive depending on the load (torque) current under a certain load wthat we can adjust and high cost torque meter that measure the current if you have a 10 amp ESC then you need a 10 dc-dc converter ,also good idea is to add a simple current monitor and comparator to turn off the motor when it hits a bump or gear gets stuck,contact switches or bumber switches on help but dont solve itthen should add a simple temperature cut-off too on motor simple circuit using a diode and op amp and few parts
are you a stock motor for main drive
here is a link to mabuchi motor for spec,another company is johnson motor company
mabuchi motor company
For those interested: I found those DC to DC converters for only $9.99 free shipping here!