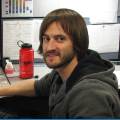
bstaehling
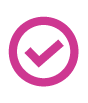
@EZ-Robot I'd like to float the idea of creating a daughter card that interfaces with the EZB-v4. The main purpose would be to allow a voltage bus selection via dip switch for each IO (ADC0-ADC7, D0-D19). It is a common issue where some devices require 5V (HC-SR04 ping sensor) and others you'd like to use higher voltage like 7V (servos), or even connect direct to the unregulated battery (H-bridge). For example, in my own situation I have a 6V battery for my Omnibot, a buck converter set for 5V, and a boost regulator set for 7V. Now, to distribute these voltage buses would require cutting and modifying numerous peripheral cables, then manually routing them to the correct sensor, while also splitting them off so the signal goes to the EZB. I think a much more elegant approach would be to design a mating daughter card that accepts the various bus voltages and allows voltage bus selection for each IO via dip switch. Furthermore the daughter card would provide a quick disconnect means. You could easily remove the EZB from one set of hardware and move it to another without all the tedious rewiring and later wondering which cable was supposed to go where.
I would very much like to design such a card, but would need the following:
- mechanical drawings showing accurate placements of connectors
- the pinouts of the connectors
- the connector types
...so I can source mating connectors and locate them on the daughter card properly. As I can see the value in this for many in the community and assuming it works out well, I'd be willing to share the design files/gerbers with the community as well.
The daughter card would mate to the face of the EZB and connect to all pins on that face. I2C, camera port, etc. would simply mate with the EZB and route directly to the other side of the daughter card on the same type of connector or else there could be holes milled in the board to allow direct connection to these ports.
This would be something I would be interested in... For now I am in the process splicing 5V buck regs into a bunch of 3 wire servo cables... An inline 5V voltage reg for sensors was discussed and supposed to appear in the store many months ago... Maybe EZ Robot forgot? I am not sure, but I decided to make my own for now....
i didn't cut my servo wires, i spiced 6" and 12" extenstion servo wires...
@Anthony, how many amps can the power board you've designed take? Do they have on board regulators? Or is it straight through like the perf boards I've used in Melvin here?
Since servo extensions are dirt cheap they are ideal to cut and use for this task.
I was just thinking about something like this last week. I was thinking more just a quick connect for leads on the EZ-B. All leads connected to one "adaptor" for switching out the EZ-B from bot to bot or to the work bench. There's nothing more time consuming then trying to relocate your leads, even if they're all labelled. I think this could be good for soldering to or having some kind of screw terminals for running regular wire instead of using jumpers and/or servo plugs. Just throwing more ideas out there.
For my big bot where I am going to need several different voltages (12 or 24 for the motors, 12 for the computer (originally planned for 19), 7.5 for the EZ-B, 5 for the sensors, etc), I was thinking of building a power distribution board with several regulators and perf boards or pin strips that I can plug servo extension wires into.
My only question is would it be better to daisy chain each lower voltage to the previous higher one, or have each one come off the original 12 or 24 v and regulate down from there.
(a few other questions about using 2 12v batteries too, but I'll cover them when it is closer to the time I need answers).
Alan
It's good to hear what every one else has done and is planning to do to distribute power and use various bus voltages. I know it's an issue I keep going back and forth with in my mind. Just before taking a set of clippers to my 3 wire servo cables, I keep thinking there's got to be a cleaner way. What if I cut up all my cables and realize, oops there's a mistake or carelessly wire a peripheral to the wrong voltage bus and let out the magic smoke? What if I want to make some quick changes down the road or substitute some sensors without having to dig through bundles of wire? I'm hoping EZ-Robot has a chance to consider the daughter card idea and is willing to provide the needed info, because I think it would be a fun little project that could add some value here.
@thetechguru My personal preference on power distribution is for each regulator to take its input directly from the feeding voltage bus (your 12V/24V). Cascading regulators can have benefits in some situations, but doing so can also create a bottleneck in how much current each regulator can supply. This can lead to unexpected sub-system interactions/unexpected brownouts if not carefully planned. When using switching regulators, I'd always recommend connecting them direct to the feeding voltage bus (assuming they are rated to handle the full input voltage). When using linear regulators, be conscientious of how much POWER the regulator dissipates to maintain its output voltage. This is how much heat will be dissipated and is THE physical limitation of what the linear regulator can do. If the amount of overhead voltage between the linear regulator's input and output is high (for example dropping 24V down to 3.3V = 20.7V overhead), the voltage may become more of a limiting factor than worrying about how much current is being bottlenecked in a cascaded configuration. It all comes down to calculating the max power dissipation in the regulator. There's more than one way to skin a cat, so do what works for you, just my 2 cents. Hopefully there's at least a little helpful info in there though.
I would really be interested in something like this. I just ran into this issue with one of my omnibot builds and have been unsure how to tackle this. All this is really unfamiliar to me so iv'e been reading some electrical engineering books and watching some youtube vids to get a better grasp of it. I hope this doesn't derail or highjack this thread but would some of the posters mind posting pictures of there current setups for something like this?
Just the other day I was talking about making something like a shield that plops on top of ezb v4 then you can apply a external power to each row of servos , even different voltages for each row.