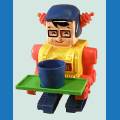
Mulberry
USA
Asked
— Edited
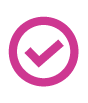
Afternoon All
I'm stumped.
I'm trying to make a connection with a non-EZ GWS servo but am having no luck. I've tested the EZ with standard servos that came with the kit and they function fine. This GWS is rated at 4.5 volts to 6 volts and I've tested it at these and even lower. The port is correct, the board is properly selected, I restarted the EZ, insured I have the latest version but still get no movement or indication a signal is reaching the servo. It doesn't appear locked because I can turn the gears by hand. I'm hesitant to take it apart just yet.
Any suggestions?
Thanks,
Daniel
It's an obvious question but it's best ask, have you connected the servo to the EZ-B the correct way round? Also trying a servo under its rated voltage won't help at all. If anything you could try a slightly higher voltage. A 4 to 6 volt servo will work ok with a 7.4 LiPo battery for example. Also have you checked the min and max values?
Are you sure the servo is plugged in correctly? White servo wire to white port
Have you made sure the min and max settings in your servo are 1 - 180 respectively? Yep
Assuming you are using an EZB4 1 - 100 if using an ezb3 EZB4
Do you have another one to test in case this one is defective... Nope but the standard servos that came with EZ work from that port
Are you sure your connected to ARC Yep 5)What battery are you using? Adjustable Work Bench tester. I've been hesitant to increase the power beyond 7.5.
Daniel
I wouldn't go beyond 7.4 volts. You say you are using a bench power supply. I would ask if it's suppling enough amps, but I take it that's what you used to successfully control the EZ Robot servos?
Have you got a multimeter laying around to check if the servo/servo wire is ok?
You may need to use a battery... If your work bench power supply can't provided enough amps then the servo won't move.... Can you confirm that the ez robot servos do indeed work with your current setup... Also double check you haven't plugged in the GWS servo backward... White to white may not match up as the signal wire...
I had another look at the servo in question... White to white looks correct... Check again that an ez robot servo works then plug the GWS in again....
Your servo may be defective... Your setup should work unless as mentioned the servo is duff.... However, try a battery in case the servo needs more juice than the EZ Robot servos do.... 7.4v battery briefly should be ok.... As DJ said, he has never had a servo that couldn't take 7.4V....
Thanks for all the advice guys. Here is where it stands:
Switched to a battery and got no response. So I changed all wires but still nothing. Then I connected the servo directly to the EZ board including power and ground (all 3 wires) and got momentary control but then the board broke the connection with my laptop. Repeated testing had the same problem including when I tried a second board.
All EZ servos work fine so I'm assuming the board is operating.
Perhaps I should be making additional ground connections between the EZ port, my battery, and the servo?
Daniel