
woodylv
USA
Asked
— Edited
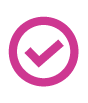
Hello All.
I need a suggestion for a motor controller to drive 2 arms that are connected to 2 screw drive actuators. (Aproximately 2 amps each)
I wanted to get some advice before I purchase anything.
I bought some other controlers with out thinking and they ended up not working.
I already have a sabretooth driving the wheels so I need something else that would work with a joy stick or a button pad.
Thanks for any advice.
Michael
The 2.5A Controller from the EZ-Robot store would do it, and is simple to set up. It's the same as the L298n H-Bridge
Although don't give up on your other one yet, I'm sure we can make it work.
Rich,
Thanks as always for your input.
I can tell you what happens is when I try to connect my other motor controler using the pwr in (The 12 v for the motors) Nothing happens
When I switch it to the Vin(From the EZB) It causes a power circut issue which has been blowing boards.
And it makes my bot run in circles
Figured it would be easier to get a board that is a recognized board and has good documentation on it.
Plus for $15 its not worth the hassel.
But if you have any more sugestions I am open to them.
How can I use the PWM and Digital controls to work with a joy stick ?
If I use the wiring harness:
Servo Power Boards
Do is till need the regulator:
Servo regulator
And, can't I control the arms without a motor controller? I will use the dual H-bridge for the base.
That's the plan anyway.
Ah yes, that's a good point. Personally I'd use something which is documented (or that is easy to figure out).
The L298n is 2.5A. I don't know if that's total shared or per motor - you may need 2 if your motors use 2A and you plan to move both at the same time. Try it on one first, it should only brown out if it can't drive both.
Using it with a joystick may be a little bit complicated as you already have a Movement Panel so can't add a second. You will need to write scripts for each movement i.e. left arm up, left arm down etc. Then call those scripts in the joystick configuration for when a button is pressed. I don't use joystick so am not sure if you can map anything to the stick that isn't a servo or Movement Panel though, but I'm confident we can get something sorted on it.
Once it's wired up and working we can tackle the joystick part.
To check it's working just write a few scripts and run them for each movement.
Assuming D0, D1, D2, D3, D4 and D5. D0 - In1 D1 - In2 D2 - In3 D3 - In4 D4 - PWM Motor 1 D5 -PWM Motor 2
Motor 1 Forwards Full Speed
Motor 1 Forwards Half Speed
Motor 1 Reverse Full Speed
Motor 1 Reverse Half Speed
Motor 1 Stop
Motor 2 Forwards Full Speed
Motor 2 Forwards Half Speed
Motor 2 Reverse Full Speed
Motor 2 Reverse Half Speed
Motor 2 Stop
If you save all of those as separate scripts in the script manager control you can call them as required with ControlCommand(). You can assign each one to a button press on a joystick, and on button up assign the stop script. If that doesn't make sense I will do a quick tutorial with screenshots to show it when I have ARC in front of me.
It's always a good idea to put in limit switches if using motors and a H-Bridge to control things like arms. This way if, for any reason, the motor doesn't stop moving the switch will kill the movement saving you from damaged robot bits. I think Dave as something like this set up on his B9 build.
@Mel, you would still need the regulator.
However I'm not quite sure where the external servo power board comes in to play on this topic. @woodylv is planning to use motors & a H-Bridge to control arms not servos. I assume he has his reasons for doing so.
I am currently working on the omnibot3000 that is shown here in the forum.
thanks,
I just threw together a bunch of scripts in a script manager called H-Bridge Scripts for easy importing in to your project. Full instructions are in the notepad on the project too but here they are again.
Download it here
Rich,
As always thanks for the consice input.
The reason I am trying a motor controler is that the devices connected to the arms are actuator type screw drive motors.
I was not involved in the design of this.
So if I put 12v to the wires the arms go up. When I reverse the polarity they come down.
I was assuming that a motor controler was the only way to go but maybe I am mistaken.
Do you think I should use a H Bridge or Motor Controler or do you have other options ?
I think that calling the script from the buttons will work just fine.
I am wondering how to put the limit switches on the screw drives since its sealed but maybe you can help on that too.
I think I am at the near end of this issue just need to buy the controler.
Let me know what you guys think.
And thanks again everyone for your input.
Later,
Michael