Asked
— Edited
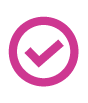
is it possible to move (9V~12V) servos?
I have really cool high quality servos.. but its difficult
regards
is it possible to move (9V~12V) servos?
I have really cool high quality servos.. but its difficult
regards
The V4 digital ports are not voltage regulated. to add to this, the V4 can be powered by up to 19V if I remember correctly. You might want to check the data sheet though.
I think you are confusing the signal voltage with the power voltage. You can provide up to 16v to the EZ-B and it will pass it on to the power pin on all digital ports. (or if you will have a mix of power requirements, you can keep the EZ-B at 7.4v and separately power the servos as long as you have a common ground).
The signal pin outputs 3.3v and can accept 1-5 volts input for applications where the pin is listening for signal (ping sensor, UART). 3.3v output for signal should be standard regardless of the power requirements of the servo, but if you have datasheets for the specific servos you are thinking of you can confirm this.
Alan
@thetechguru
Oh oops, okay, yes I confusing the signal voltage with the power voltage.
I want to move this "KRS-2552RHV ICS" Servo:
Technical specifications> (at 11.1 V)
Maximum torque: 14.0Kgf · cm Maximum speed: 0.14S / 60 ° Dimensions: 41 × 21 × 30.5 mm (without protruding parts) Weight: 41.5 g (without servo horn) Maximum operating angle: 270 ° Maximum power consumption: 1.3A Transmission type: metal Housing material: Resin Translation ratio: 312.4: 1 Supply voltage: HV specification (9V ~ 12V) Communication standards: ICS3.5 (serial / PWM selection formula) Communication speed: 115200/625000 / 1250000Bps Initial setting: ID0 / BR115200 Signal level: TTL Rotation mode: Yes
Just use a 11.1V Lipo battery with your ezb4 instead of a 7.4v battery... Problem solved... You could even use a 12V SLA battery too if you want...
@Richard R
ok, the servo runs but it has "Signal level: TTL" so I think its not possible "to control" the servo by the EZ-Robot Board..
I thought it's possible to move it at once.. in Single.Mode.. But does not..
To daisy chain, you will need to use serial mode, and a custom script. In PWM mode, one per EZ-B digital port, they should work.
Alan
@Smarty... The servo stats say they accept PWM so as Alan mentioned plugging them in separately to individual ports on the ezb4 should work....
@thetechguru @Richard R
thanks