
ed_eilers
Netherlands
Asked
— Edited
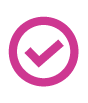
I would like to get some help on serial bus servo's that use almost the same protocol as dynamixel.
BUT all the dynamixel instruction packets and status packets start with:
0xFF 0xFF and then you get ID> Length> Instruction>Parameters>Checksum
like this
The servo's I want to use are Lobot LX-16A that use the same protocol with one difference: the packets start with 0x55 0x55 and then ID> Length> Instruction>Parameters>Checksum
so my servo's don't react on the dynamixelplugin How can I or someone change the 0xff too 0x55 in the plugin? Is it possible too get the source code for the plugin? or is there another solution? I can't afford real dynamixels and this seemed a good alternative
thanx in advance for your help
Hmm, the plugin description indicates it is open source, so you should be able to modify it, but if there is a link to the source code, I am missing it (other open source plugins have a link in the description).
@DJ is this one open source and am I right that the link is missing?
Alan
Get the source code here: https://synthiam.com/redirect/legacy?table=plugin&id=39
Thank you for this fast response techguru and dj Sures
I hope that I can get this to work will take some time but if I got it working i will post it for other people too use.
I think these are nice servo's and it will open some new possibilities for my Ez robot Can tell you that I'm very happy with Ez robot and the effort that is put in it.
thanks guys
Thanks for the kind words
I picked up some LX-16A nice servos, lots of torque. There is a directory here with the program and PDF's
https://www.dropbox.com/sh/b3v81sb9nwir16q/AACkK-tg0q39fKJZcSl-YrqOa/LX-16A%20Bus%20Servo?dl=0
The communication protocol is fairly well documented https://www.dropbox.com/sh/b3v81sb9nwir16q/AACkK-tg0q39fKJZcSl-YrqOa/LX-16A%20Bus%20Servo?dl=0&preview=LewanSoul+Bus+Servo+Communication+Protocol.pdf
haven't managed to get to work with EZB yet. Tried the dynamixel plugin but no luck as per above it initialized with 0x55 not 0xFF
I opened source to change to 0X55 but two pages of errors in visual studio ... I think I will go play with the UART
Errors if you opened the plugin because it’s not configured for the ARC and ezb dll resources for your installation. It’ll be different for every computer.
Follow the tutorial on creating a plugin to familiarize yourself with visual studio and programming. It’s fun, even if it takes a while!
Not sure if i got the packet correct, but you can give this a shot: https://synthiam.com/redirect/legacy?table=plugin&id=252
I ordered a servo to test with.
Thanks DJ - lights are on but :-) I guess 0x55 was not the only difference or I am doing something wrong.