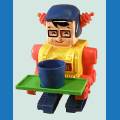
Mulberry
USA
Asked
— Edited
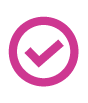
Evening All
I'm working with H-Bridges and am having trouble finding the controls to regulate speed. I've followed the tutorial which directs me to use the PWM slider to regulate speed however I can't locate this control. When I open the Control tab this is all I see:
Any suggestions? My board interface is different from the one in the tutorial.
Thanks,
Daniel
It's all changed since the tutorial videos were made.
H-Bridge PWM Movement Panel is what you need.
Then configure the left and right PWM ports
Alternately, you can add a PWM slider and use the 4 Wire H-Bridge without PWM control Movement Panel
And set it up for the correct port
Excellent. Thanks Rich. I'm getting closer. I can run my motor via the H Bridge now however using the PWM isn't working to control speed. I suspect I'm missing a connection wire. The video tutorial has a PWM wire soldered across two terminals however my H Bridge is missing those (I think its newer than the one in the tutorial). I used the diagram published on this page to create my connections:
https://synthiam.com/Tutorials/Help.aspx?id=70
Can you post a close-up pic of your actual board?
Read the instructions please:) the button must be pressed
@Mulberry you'll need to have the enable lines on the motor driver board hooked up to a couple (or just 1) digital pin(s) in order to use the PWM sliders to adjust speed, it is shown on the tutorial video but not the diagram. The Diagram shows the enable lines tied to +5V (always enabled) with jumpers but DJ uses wires connected to the EZ-B in the video example. It is possible to PWM the input lines in order to trim speed but you would have to write your own custom EZ-Script to do it. That being said, a custom script is pretty straight forward. If you'd like to go that route and meet any challenges just post again and the community is sure to give you the advise you need.
Jeremie, he'll need both (not 1) pwm if using the hbridge speed control - otherwise the robot won't turn
Just meant that you soldered 2 enable connections to 1 wire in the video so you could only use 1 Digital to control PWM. Sorry man, should have been more clear.