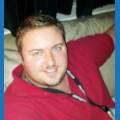
jstarne1
USA
Asked
— Edited
I ordered a Solidoodle 2 Pro which arrived today. I also ordered with that 2 rolls of filament. It should be 4 total pounds of material to start with.
Update , robot doc , yes it was torqued down so I went to home depot and purchased nuts to match the thread. 5/16 -18 course threads. Then threaded two on and locked them together by turning the first backwards. I then used a wrench to gently turn the Z axis until it was unstuck.
https://www.youtube.com/watch?v=4OsSRnAiTf4&feature=youtube_gdata_player
Test after I lubed the Z axis and the y and X axis rails as well.
https://www.youtube.com/watch?v=_yN4mdQ1VtQ&feature=youtube_gdata_player
I wanted to share this , this print was the last one before the Z axis locked. It was a 9.5 hour print of a Hand piece I was attempting as a solid piece with lots of detail. I used supports. The supports printed great but the object itself is practically none existent. Only the repulser actually printed. Some say it was the walls themselves were too thin and the machine could negotiate that in mid air. Never the less I have a giant loofah worth keeping just to laugh about.
It's almost a epic misprint , it pretty much printed everything but the object yet due to a optical illusion, you think the glove is inside. This demonstrates good reasons why I need to learn to use the autodesk software.
Cool updates. At least your printer appears to be working again.
Josh, I'm sure you're aware that there are multiple slicer programs out there that may help get some of your more busy 3D prints to actually print on your printer. You may have to experiment a bit to find one that is right for your detailed prints.
Yea i have tried makerbot and it didn't like the g code , it just wouldn't initiate the prints. Anyways I finished a print which was 90 percent good but I notice my rows don't squish together so I'm researching how to fix this in the firmware.
you can see in some areas the layers are not stuck together well on the horizontal plane. Apparently this has to do with amount extruded and individual layer hieght. Making the layer shorter causes squish I really need.
I did a acetone bath to adhere the seperate layers together , you can pour it on or dab it on with a cloth.
The parts do seem to be more stable but you need to let them sit a few hours so all the acetone evaporates and abs rehardens. I will let them sit overnight and update everyone tommorow. You can do this with heat , like a butane torch or propane to glaze the surface of the pla.
This seems like the best acetone vapor method I've see.
@anthony , yup makerbot is better , if I could find one for about 1200 I would sell solidoodle and get another one. That being said overtime the prints have gotten better but there's so much manual adjustments physically and in the firmware to make it do a great job.
Yes I do think the slicer is partially to blame.