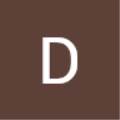
Knusel
This Video Show my problems
I have problems with my hexapod. The robot makes uncontrolled movements every time the ezb is restarted. (as soon as I control a motor)
Or as soon as the engines need power. With both, it always ends with the ezb restarting. Now I don't know exactly where the problem lies. I suspect servos or voltage. I'm currently using a power bank (9v 3a), but I've also tried a power supply (also 9v 3a) with the same result.
But the same problem also occurs with another robot of mine, where I use a different ezb and different servos.
Am I doing something fundamental wrong? or is the ezb just suitable for small robots with small motors?
I Used this servos:
https://www.amazon.de/dp/B07T756ZYC/ref=cm_sw_r_apan_glt_i_S26QNBSS312FF2Y1XE00?_encoding=UTF8&psc=1
all servos work individually. (Apart from the fact that they move uncontrollably for a short time when they are controlled for the first time)
My hex bot is using mostly the older Original Ez robot HD servos and it can be a power hog but I find that if I use a bigger Lipo 7.4 battery (5000 ma) and not let servos go to maximum speed, just walking around .It will explore a fairly long amount of time, with 1 sonar,camera or RGB lit eyes. It always curls up when it starts but no big deal there.
First, thanks for the quick response. But you can see in my video at 0:45 that I have already set my servos to very slow. But if the servos start to move uncontrollably then ignore the settings. The same at the first start. As soon as the servos get power, they move at maximum speed for the first moment, no matter what I have set.
And I guess because all the servos are "jumping" at the same time, it takes too much power at once and the ECB shuts down... but what can I do about it (if that's the problem)?
Okay I saw the video, that is a much bigger Hex bot compared to my EZ robot Hex, There is someone else in the Forum that built a large one like that . IF You research this forum and look for a thread about Gargantua , I believe it was called, you may get some good fix ideas.
Hi there - that's an easy one. The EZB is rebooting because it isn't getting enough amperage for all the servos to move simultaneously. There's a good read with more detail here: https://synthiam.com/Support/Get-Started/how-to-make-a-robot/power
Check out the recommended options for power supply. There's also a real good (albeit more extended read) tutorial on that page about how power works with the robot.
The "slowness" of the servos moving isn't going to prevent the current spike from causing the EZ-B to brownout. As you can see by how quickly the servos "jump" to their position, it is because that has to happen before the servos can begin moving.
I know there's a lot of reading, but here's how servos work: https://synthiam.com/Support/Advanced-Fundamentals/servo-motor
Your Script I had to pause the video to see your script, but the reason only the first servo runs is that the port increment syntax is incorrect.
It can read one of these two ways to do it...
or
Also didn't Will make a large hex robot Gargantua his user name is fxrtst..Link here...https://synthiam.com/Community/Robots/Project-Gargantua-or-Gar-230
Oh, one more thing... When the EZ-B is first connected, it will not know the servos' positions. That means if the servos are resting at a position 120, and you specify to move to position 90, they will JUMP to 90 no matter what speed is set. This is because these types of servos are not "Smart" and therefore do not report their position on power-up.
That's okay because there is a workaround. The most simplest workaround is to initialize each servo into a position when the EZB starts up. You can do this by creating a script, calling it INIT, and running it when the EZ-B starts. It can do something like this.
I use JavaScript
In this example, servos ports are not linear, or the init positions are different per servo/joint. Also, tweak the sleep() time to give each servo enough time to move into position. It may require one full second (1000 ms) per servo.
In this example, the servos are all the same degrees, and ports are linear
Wow great info DJ! I will do this too for all my bots!
Awesome, robo rad. You can read more because i stole it from here: https://synthiam.com/Support/Tips-to-Make-a-Robot/initialize-servos
:)