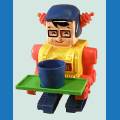
Mulberry
USA
Asked
— Edited
Morning All
Does anyone have experience or an opinion on putting an EZ Board in a project enclosure box (like the ones from Radio Shack)? I want to protect from damage and dust inside my B9. My thoughts were to cut side vents for heat ventilation. I plan to get as large a box as possible to insure circulation.
Thanks,
Daniel
You could drill some breathing holes and put one or more fans inside or outside of the box.
There have been discussions about similar in the past. The waterproofing of it it discussion may be of some use.
The main concern would be the heat generated by the regulators and even if it's not much it will all mount up.
Add in some vents and a fan and it should be good to go.
Better yet, the EZ-Case 3D Printed case may be just what you need.
@Mulberry , what kind of project are you doing? Are servos going to be connected to the EZB?
Thanks All
Hi J. It's a life size B9 robot from Lost in Space. The unit has several servos including some strong ones powered by 12 volt batteries so I'm using Pololu H-Bridges. I'm now considering simply a cage of sorts to avoid damage. Perhaps a mesh desk organizer flipped over (see below) and a fan as Rich recommends. The various robot sections are quite cumbersome when you move them about so I need something to protect electronic components.
Daniel
A metal cage might act as a faraday cage and block the Bluetooth or WiFi signal (depending on if you are using a V3 or V4 board). I would stick with plastic.
I think you will be fine if you cut some vent holes in a plastic project box, and mount in a low voltage fan like a CPU fan.
Alan
Good point Alan.
Thanks,
Daniel
Small cardboard box with vent holes? Just an idea. Any which way that's a cool B9.
Thanks Technopro. He's 98% complete now. That photo is about a year old. I have one EZ board currently running the lower section and will use another for the upper section once the new boards start shipping.
Daniel